¿Cómo se fabrican los compuestos de fibra de carbono? | Guía experta de Supreme Carbon
¿Cómo se fabrican los compuestos de fibra de carbono? Comprensión de los procesos principales
Fibra de carbonoLos materiales compuestos se sitúan a la vanguardia de los materiales avanzados, revolucionando industrias desde la aeroespacial hasta la automoción, desde las energías renovables hasta la de artículos deportivos. Su inigualable relación resistencia-peso y rigidez los hacen indispensables para aplicaciones de alto rendimiento. Para los usuarios de la industria que participan en la reaprovisionamiento, un profundo conocimiento de sus procesos de fabricación es crucial para garantizar un rendimiento óptimo, rentabilidad y fiabilidad. Desmitifiquemos cómo se materializan estos extraordinarios materiales.
¿Cuáles son los materiales fundamentales utilizados en los compuestos de fibra de carbono?
El rendimiento de uncompuesto de fibra de carbonoLa pieza comienza con sus materiales constituyentes: las fibras de carbono y la resina matriz. Las fibras de carbono proporcionan resistencia y rigidez, mientras que la resina las une, transfiere la carga entre ellas y las protege de las agresiones ambientales.
- Fibras de carbono:Estas fibras se derivan típicamente del poliacrilonitrilo (PAN) o precursores de brea mediante un complejo proceso de estabilización, carbonización y grafitización. Las fibras se clasifican según su módulo (rigidez) y resistencia. Por ejemplo, las fibras de alto módulo (HM) se utilizan donde la rigidez es fundamental (p. ej., estructuras de satélites), mientras que las fibras de alta resistencia (HS) se prefieren para la resistencia al impacto (p. ej., fuselaje de aeronaves). Un tamaño de cable común en aplicaciones industriales es 12K (12 000 filamentos por cable) o 24K.
- Resinas de matriz:
- Termoestables:Estas son las más comunes y su curado es irreversible. Las resinas epoxi dominan el mercado, representando aproximadamente entre el 70 % y el 80 % de las aplicaciones de compuestos avanzados, especialmente en el sector aeroespacial, gracias a sus excelentes propiedades mecánicas, adhesión y estabilidad térmica. Otros termoestables incluyen el poliéster y el éster de vinilo (para aplicaciones de menor coste y menor exigencia), las resinas fenólicas (para resistencia al fuego) y las resinas de celulosa/poliimida (para entornos de alta temperatura, que a menudo superan los 200 °C).
- Termoplásticos:Materiales como el PEEK (poliéter éter cetona) y el PEI (polieterimida) ofrecen una tenacidad superior, resistencia al impacto, una vida útil ilimitada para los preimpregnados y reciclabilidad. Si bien su procesamiento es más complejo y requiere temperaturas más altas (el PEEK se funde a unos 343 °C), están ganando terreno en sectores de alto rendimiento.
¿Cuáles son los principales métodos de fabricación de compuestos de fibra de carbono?
La elección del método de fabricación influye significativamente en las propiedades, la complejidad, el volumen de producción y el coste de la pieza final. Estas son las técnicas más comunes:
- Colocación manual/Colocación húmeda:El método más sencillo consiste en colocar manualmente telas secas en un molde y luego saturarlas con resina líquida mediante brochas o rodillos. Requiere mucha mano de obra y es económico en cuanto a herramientas, pero presenta una calidad irregular y un alto contenido de huecos (a menudo del 5 al 10 %). Ideal para prototipos o piezas de bajo volumen y no críticas.
- Envasado al vacío/Infusión al vacío (VARTM/LRTM):Una mejora con respecto al laminado manual. Las telas secas se colocan en un molde, se sella una bolsa de vacío sobre ellas y la resina se introduce en el laminado mediante presión de vacío. Esto reduce significativamente el contenido de huecos (normalmente entre un 1 y un 5 %) y mejora la relación fibra-resina en comparación con el laminado manual. Ideal para piezas de tamaño mediano con complejidad moderada.
- PreimpregnadoLaminado y curado en autoclave:Considerado el estándar de oro para compuestos de alto rendimiento. Las láminas de fibra de carbono preimpregnadas (fibras ya preimpregnadas con una cantidad medida de resina y parcialmente curadas) se colocan en un molde. A continuación, el conjunto se envasa al vacío y se cura en autoclave a temperatura y presión controladas. Este método ofrece las mejores propiedades mecánicas, el menor contenido de huecos (a menudo inferior al 1-2%) y un excelente acabado superficial. Ampliamente utilizado en la industria aeroespacial y el automovilismo.
- Moldeo por transferencia de resina (RTM) / Moldeo por compresión:Las fibras secas se colocan en un molde rígido cerrado. Posteriormente, se inyecta resina a presión (RTM) o se comprime una mezcla de resina precatalizada entre las mitades del molde (moldeo por compresión). Estos métodos son adecuados para la producción en grandes volúmenes de formas complejas con un buen acabado superficial en ambas caras. El costo de las herramientas es elevado.
- Bobinado de filamentos:Las fibras de carbono continuas, preimpregnadas o impregnadas con resina, se enrollan en un mandril giratorio siguiendo un patrón preciso. Excelente para la fabricación de piezas huecas con simetría rotacional, como recipientes a presión, tuberías y ejes de transmisión, ofreciendo una excelente relación resistencia-peso en direcciones específicas.
- Pultrusión:Un proceso continuo en el que fibras impregnadas de resina se estiran a través de una matriz calentada para formar perfiles de sección transversal constante (p. ej., varillas, vigas, tubos). Altamente eficiente para piezas compuestas largas y continuas con un alto contenido de fibra (a menudo, del 60 al 70%).
- Colocación automatizada de fibra (AFP) / Colocación automatizada de cintas (ATL):Los sistemas robóticos colocan con precisión cintas o estopas de preimpregnado individuales sobre la superficie de un molde. Estos métodos altamente automatizados se utilizan para estructuras grandes y complejas (p. ej., alas de aeronaves, fuselajes) donde la precisión, la repetibilidad y el alto rendimiento son cruciales. Requieren una inversión de capital considerable, pero ofrecen ahorros significativos en mano de obra para grandes series de producción.
- Actuación:El curado en autoclave de preimpregnados ofrece las mejores propiedades mecánicas, un mínimo contenido de huecos y una consistencia superior, lo que lo hace esencial para la industria aeroespacial (p. ej., el Boeing 787 utiliza más del 50 % de su peso en materiales compuestos). La infusión al vacío ofrece un buen rendimiento a un menor coste que el autoclave, ideal para componentes marinos o automotrices. El moldeo por RTM/compresión proporciona un buen acabado superficial y ciclos más rápidos para piezas de volumen medio a alto.
- Costo:El laminado manual ofrece el menor costo de herramientas y configuración inicial, pero genera un alto desperdicio de mano de obra y material. El preimpregnado en autoclave requiere una inversión significativa en autoclaves, salas blancas y herramientas sofisticadas, lo que aumenta el costo por pieza para volúmenes bajos, pero se justifica para componentes críticos de alto rendimiento. Los procesos automatizados (AFP/ATL) tienen la mayor inversión de capital, pero ofrecen economías de escala para volúmenes de producción muy grandes.
- Consistencia y repetibilidad:Los procesos altamente automatizados y controlados, como el curado en autoclave de preimpregnados, RTM y AFP/ATL, ofrecen una consistencia y repetibilidad superiores, lo cual es fundamental para los componentes críticos para la seguridad y la fabricación a gran escala.
- Diseño y herramientas:Diseño de la pieza y creación de moldes (herramental) que resistan las temperaturas y presiones de curado. Los herramentales pueden fabricarse con diversos materiales, como invar, aluminio o materiales compuestos.
- Preparación del material:Corte de telas de fibra de carbono o preimpregnados para darles forma mediante cortadores CNC, a menudo en un entorno de sala limpia para preimpregnados para evitar la contaminación.
- Bandeja:Colocación de las capas cortadas en el molde. Esto puede ser manual, semiautomático (guiado por proyección láser) o totalmente automático (AFP/ATL). La orientación de las fibras es crucial para la resistencia.
- Impregnación de resina (si no es preimpregnada):Para la colocación húmeda o infusión al vacío, se aplica o infunde resina en la pila de fibras secas.
- Ensacado (para procesos asistidos por vacío):Sellado de la pieza con una bolsa de vacío para evacuar el aire y compactar el laminado.
- Curación:Se aplica calor o presión en un horno o autoclave para polimerizar la resina. El ciclo de curado preciso (velocidades de rampa de temperatura, tiempos de mantenimiento, niveles de presión) es crucial y suele estar especificado por el fabricante de la resina.
- Desmoldeo:Retirada de la pieza curada del molde.
- Recorte y acabado:Recorte de material sobrante, perforación de agujeros y lijado. Esto suele hacerse con herramientas diamantadas debido a la naturaleza abrasiva de la fibra de carbono.
- Postcurado (opcional):Algunas piezas pueden requerir calentamiento adicional para desarrollar completamente sus propiedades mecánicas.
- Inspección de entrada de material:Verificar las especificaciones de la materia prima (fibra, resina, preimpregnado), los números de lote y las fechas de vencimiento (para los preimpregnados, la vida útil en el congelador es fundamental).
- Monitoreo de procesos:Monitoreo en tiempo real de temperatura, presión, niveles de vacío y ciclos de curado durante la fabricación. El incumplimiento de estos parámetros puede afectar significativamente la calidad de la pieza.
- Inspección visual:Comprobación de defectos en la superficie como huecos, delaminaciones, áreas ricas en resina o fibra, restos de objetos extraños (FOD) e imperfecciones en la superficie.
- Inspección dimensional:Uso de CMM (máquinas de medición de coordenadas) o escáneres láser para verificar las dimensiones, tolerancias y ajuste de las piezas.
- Ensayos no destructivos (END):Crucial para la detección de defectos internos sin dañar la pieza.
- Inspección ultrasónica:Las técnicas de pulso-eco o transmisión directa detectan huecos, delaminaciones y desalineaciones de fibras.
- Radiografía de rayos X/exploración por TC:Proporciona imágenes internas detalladas, útiles para detectar porosidad, objetos extraños o deformación de fibras.
- Termografía:Detecta defectos del subsuelo mediante el análisis de patrones de flujo de calor.
- Pruebas destructivas (DT):Periódicamente, se cortan pequeños cupones de piezas o paneles de prueba específicos para verificar las propiedades mecánicas (resistencia a la tracción, resistencia a la compresión, resistencia al corte, resistencia a la flexión) y la fracción volumétrica de la fibra. También se realiza un análisis del contenido de huecos.
- Trazabilidad:Mantener registros meticulosos de las materias primas, los parámetros del proceso y los resultados de la inspección de cada pieza, lo que permite una trazabilidad completa desde la materia prima hasta el producto terminado. Este es un requisito común en industrias reguladas como la aeroespacial.
¿Cómo afectan los procesos de fabricación al rendimiento y al coste de las aplicaciones industriales?
La selección de un proceso de fabricación es un equilibrio crucial entre el rendimiento deseado, el volumen de producción y el coste. Para la reaprovisionamiento, comprender estos impactos es vital:
¿Cuáles son los pasos críticos en el ciclo de fabricación de compuestos de fibra de carbono?
Si bien los pasos específicos varían según el proceso, un ciclo de fabricación general implica:
¿Qué medidas de control de calidad son esenciales para que las piezas de fibra de carbono sean fiables?
Garantizar la integridad y el rendimiento depiezas de fibra de carbonoEs fundamental, especialmente para aplicaciones críticas. Las medidas clave de control de calidad (CC) incluyen:
Para los usuarios de la industria que buscan volver a comprar piezas de fibra de carbono, la adhesión de un fabricante a un estricto control de calidad, demostrado a través de certificaciones (por ejemplo, AS9100 para la industria aeroespacial, ISO 9001), documentación detallada del proceso y un sólido programa de NDT, es un fuerte indicador de confiabilidad y consistencia del rendimiento.
EnCarbono supremoEntendemos que la integridad de sus componentes de fibra de carbono es fundamental. Aprovechamos procesos de fabricación de vanguardia, que incluyen laminado avanzado de preimpregnados y curado en autoclave, junto con rigurosos protocolos de control de calidad. Nuestro compromiso con el uso de materiales de alta calidad e ingeniería de precisión garantiza que cada pieza que entregamos cumpla con las especificaciones de rendimiento más exigentes, brindándole una confiabilidad inigualable y una ventaja competitiva en su sector. Al elegir Supreem Carbon, elige un socio dedicado a soluciones de compuestos de alta calidad.

La principal marca de accesorios de fibra de carbono para motocicletas de Asia
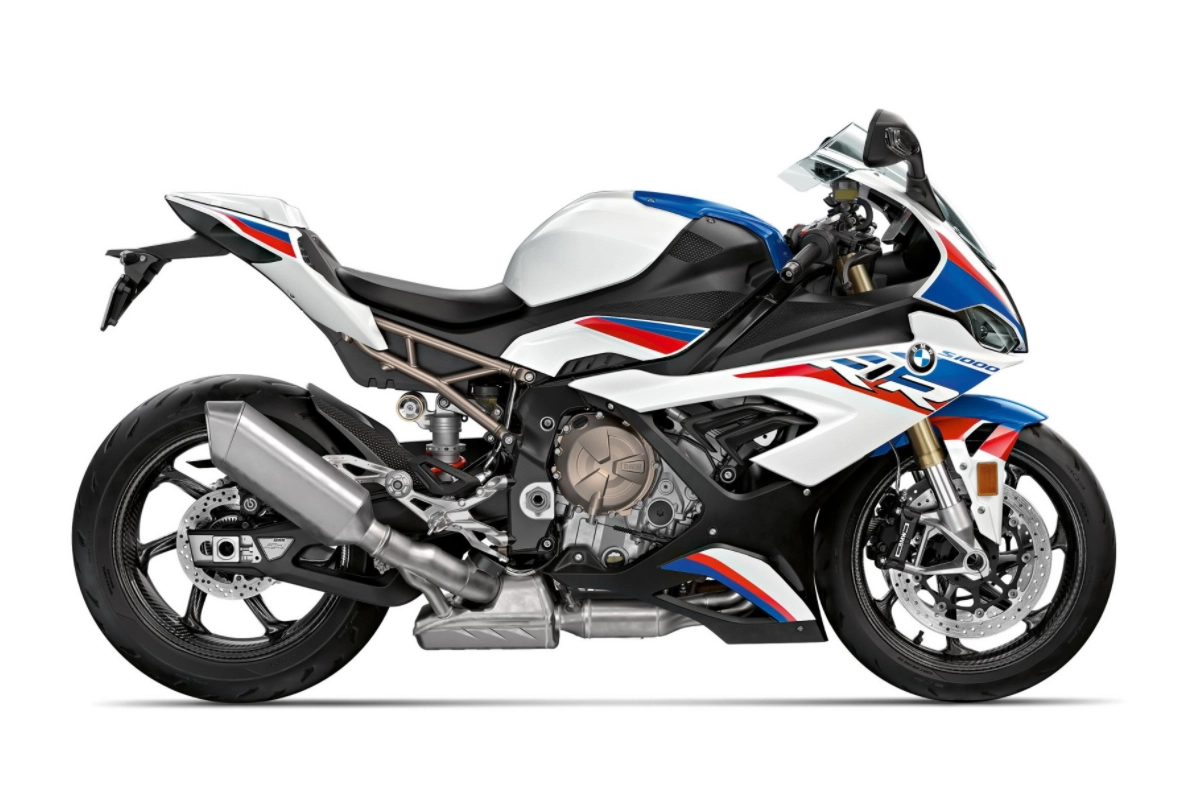
Acelera tu viaje: Supreem Carbon: las mejores piezas de fibra de carbono para motocicletas personalizadas de China
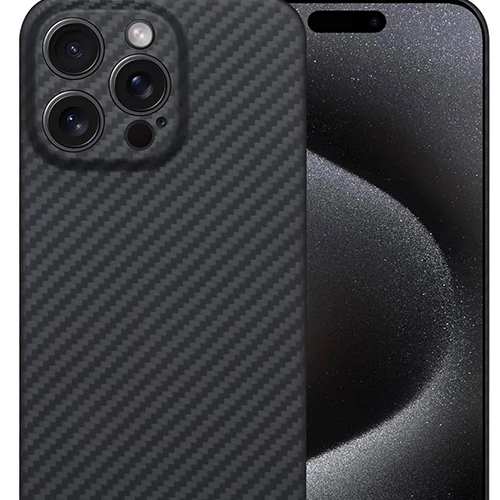
Las 5 preguntas que siempre has tenido sobre la fibra de carbono
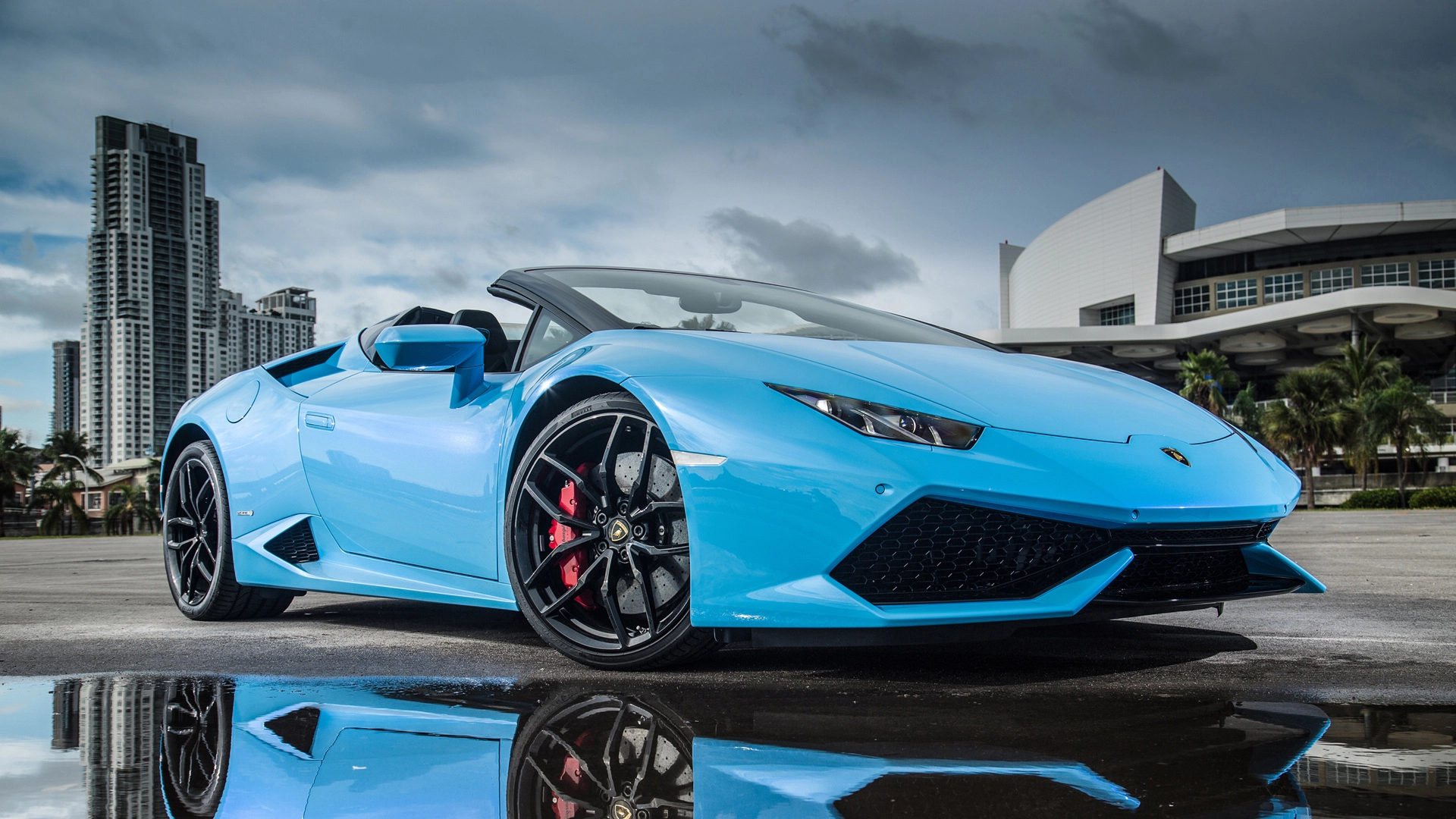
Investigación sobre las causas del amarilleamiento de los productos de fibra de carbono.
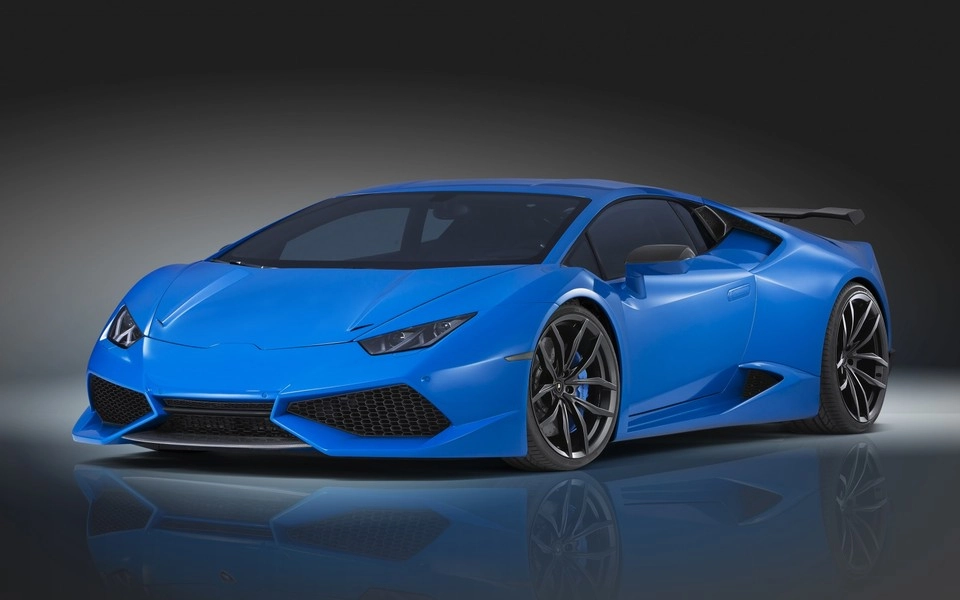
¿Es buena la fibra de carbono para los coches?
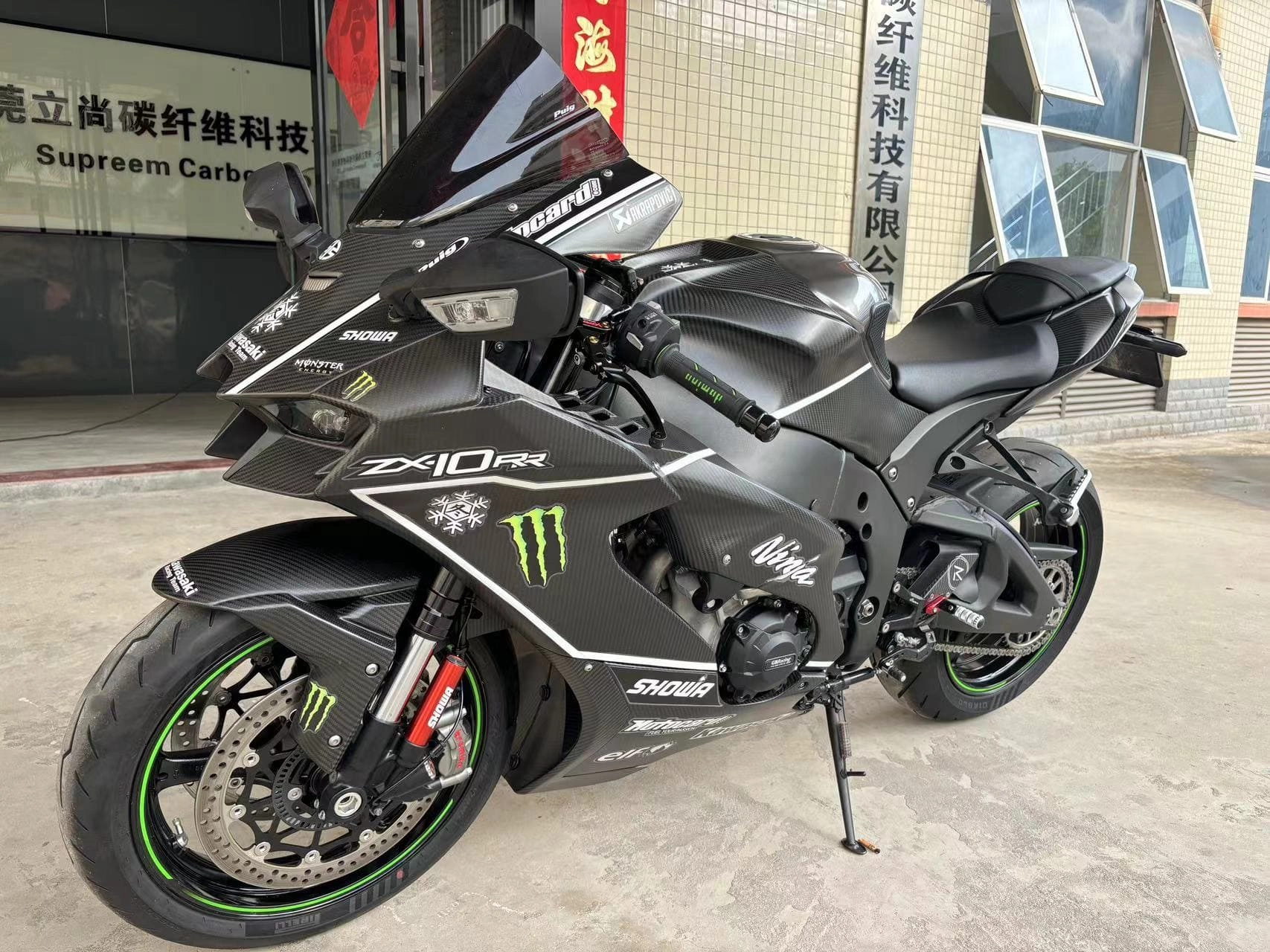
Kawasaki ZX10R Aspecto de nuevo patrón de fibra de carbono.
Para fábrica
¿Puedo visitar su empresa?
Por supuesto, estamos en la ciudad de QiaoTou, ciudad de Dongguan, provincia de Guangdong, China.
¿Cuando se fundó Supreme Carbon?
Nuestra empresa se estableció formalmente a principios de 2017.
Para productos
¿Qué superficie podría proporcionar para las piezas de carbono?
Acabado brillante, acabado mate, acabado satinado. Algunos recubrimientos de color según las necesidades del cliente.
¿Qué material de fibra de carbono puede proporcionar en producción?
1*1 liso / 2*2 sarga / carbono forjado / panal de abeja / kevlar, etc.
Para servicio postventa
¿Ofrecen el asesoramiento adecuado?
¡Por supuesto! Si tienes alguna pregunta, contáctanos en info@supreemcarbon.com.

Carenado trasero de fibra de carbono personalizado para Ducati Panigale V4

Carenados laterales inferiores de fibra de carbono personalizados para BMW S1000RR

Guardabarros trasero de fibra de carbono Yamaha R1/R1M
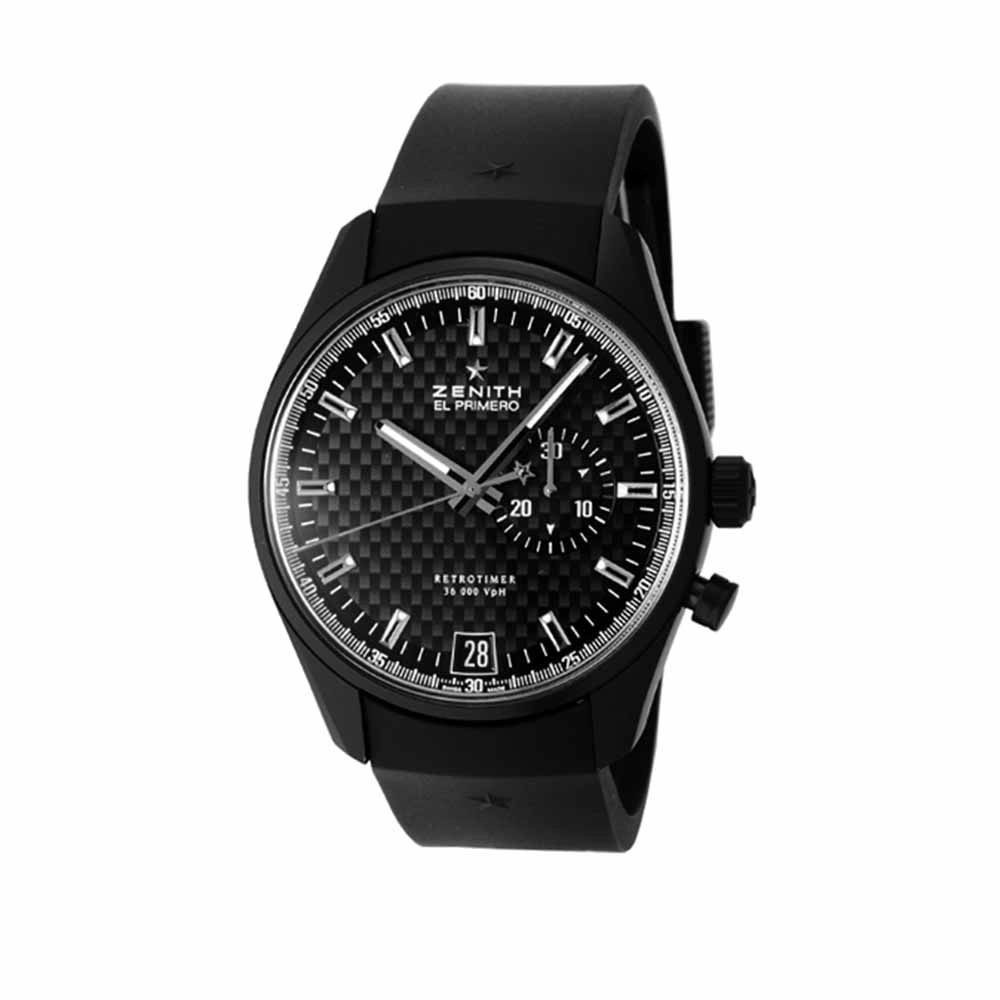
Reloj de fibra de carbono personalizado
Dejar un mensaje
¿Tiene alguna pregunta o consulta sobre nuestros productos compuestos de fibra de carbono? Déjenos un mensaje aquí y nuestro equipo se pondrá en contacto con usted a la brevedad.
Ya sea que esté interesado en pedidos personalizados, especificaciones técnicas u oportunidades de asociación, estamos aquí para ayudarlo.
Por favor, rellene los campos de arriba con su nombre, dirección de correo electrónico y mensaje.
© 2024 Supreem Carbon Todos los derechos reservados.
Facebook
Interés
LinkedIn
Instagram