Wie werden Kohlefaserverbundwerkstoffe hergestellt | Supreem Carbon Expertenratgeber
Wie werden Carbonfaser-Verbundwerkstoffe hergestellt? Die wichtigsten Prozesse verstehen
KohlefaserVerbundwerkstoffe gehören zu den modernsten Werkstoffen und revolutionieren Branchen von der Luft- und Raumfahrt über die Automobilindustrie und erneuerbare Energien bis hin zu Sportartikeln. Ihr unübertroffenes Verhältnis von Festigkeit zu Gewicht und ihre hohe Steifigkeit machen sie für Hochleistungsanwendungen unverzichtbar. Für Industrieanwender, die mit der Wiederbeschaffung befasst sind, ist ein tiefes Verständnis ihrer Herstellungsprozesse entscheidend, um optimale Leistung, Kosteneffizienz und Zuverlässigkeit zu gewährleisten. Wir entmystifizieren, wie diese bemerkenswerten Materialien zum Leben erweckt werden.
Welche grundlegenden Materialien werden in Kohlefaserverbundwerkstoffen verwendet?
Die Leistung einesKohlefaserverbundstoffDer Bau eines Bauteils beginnt mit seinen Ausgangsmaterialien: den Carbonfasern und dem Matrixharz. Carbonfasern sorgen für Festigkeit und Steifigkeit, während das Harz sie verbindet, die Belastung zwischen den Fasern überträgt und sie vor Umwelteinflüssen schützt.
- Kohlenstofffasern:Diese Fasern werden typischerweise aus Polyacrylnitril (PAN) oder Pechvorläufern durch einen komplexen Prozess der Stabilisierung, Karbonisierung und Graphitisierung gewonnen. Fasern werden nach ihrem Modul (Steifigkeit) und ihrer Festigkeit kategorisiert. Beispielsweise werden hochmodulige Fasern (HM) dort eingesetzt, wo Steifigkeit von größter Bedeutung ist (z. B. bei Satellitenstrukturen), während hochfeste Fasern (HS) für die Schlagfestigkeit (z. B. bei Flugzeugrümpfen) bevorzugt werden. Eine gängige Faserstärke in industriellen Anwendungen ist 12K (12.000 Filamente pro Faser) oder 24K.
- Matrixharze:
- Duroplaste:Diese sind die gebräuchlichsten und härten irreversibel aus. Epoxidharze dominieren den Markt und machen aufgrund ihrer hervorragenden mechanischen Eigenschaften, Haftung und thermischen Stabilität schätzungsweise 70–80 % der Anwendungen für Verbundwerkstoffe aus, insbesondere in der Luft- und Raumfahrt. Weitere Duroplaste sind Polyester und Vinylester (für kostengünstigere und weniger anspruchsvolle Anwendungen), Phenolharze (für Feuerbeständigkeit) und BMI/Polyimid (für Hochtemperaturumgebungen, oft über 200 °C).
- Thermoplaste:Materialien wie PEEK (Polyetheretherketon) und PEI (Polyetherimid) bieten überlegene Zähigkeit, Schlagfestigkeit, unbegrenzte Haltbarkeit für Prepregs und Recyclingfähigkeit. Obwohl die Verarbeitung komplexer ist und höhere Temperaturen erfordert (PEEK schmilzt bei etwa 343 °C), gewinnen sie in Hochleistungssektoren an Bedeutung.
Was sind die wichtigsten Herstellungsverfahren für Kohlefaserverbundwerkstoffe?
Die Wahl des Fertigungsverfahrens hat erhebliche Auswirkungen auf die Eigenschaften, die Komplexität, das Produktionsvolumen und die Kosten des Endprodukts. Hier sind die gängigsten Techniken:
- Handlaminat/Nasslaminat:Einfachste Methode: Trockene Gewebe werden manuell in eine Form eingelegt und anschließend mithilfe von Bürsten oder Walzen mit flüssigem Harz getränkt. Arbeitsintensiv, geringe Werkzeugkosten, aber schwankende Qualität und hoher Hohlraumanteil (oft 5–10 %). Geeignet für Prototypen oder unkritische Teile in kleinen Stückzahlen.
- Vakuumbeutel/Vakuuminfusion (VARTM/LRTM):Eine Weiterentwicklung des Handlaminierens. Trockene Gewebe werden in eine Form gelegt, ein Vakuumbeutel darüber verschlossen und das Harz durch Vakuumdruck in das Laminat gesaugt. Dadurch wird der Hohlraumgehalt deutlich reduziert (typischerweise 1–5 %) und das Faser-Harz-Verhältnis im Vergleich zum Handlaminieren verbessert. Ideal für mittelgroße Teile mit mittlerer Komplexität.
- PrepregLaminieren und Aushärten im Autoklaven:Gilt als Goldstandard für Hochleistungsverbundwerkstoffe. Vorimprägnierte (Prepreg) Carbonfaserplatten (Fasern, die bereits mit einer genau dosierten Harzmenge vorimprägniert und teilweise ausgehärtet sind) werden in eine Form gelegt. Die Baugruppe wird anschließend vakuumverpackt und bei kontrollierter Temperatur und Druck im Autoklaven ausgehärtet. Dieses Verfahren liefert höchste mechanische Eigenschaften, geringste Porengehalte (oft unter 1–2 %) und eine hervorragende Oberflächengüte. Weit verbreitet in der Luft- und Raumfahrt sowie im Motorsport.
- Harztransferformung (RTM) / Formpressen:Trockene Fasern werden in eine geschlossene, starre Form eingelegt. Anschließend wird Harz unter Druck eingespritzt (RTM) oder eine vorkatalysierte Harzmischung zwischen den Formhälften gepresst (Formpressen). Diese Verfahren eignen sich für die Großserienproduktion komplexer Formen mit beidseitig guter Oberflächengüte. Die Werkzeugkosten sind hoch.
- Filamentwicklung:Endlos-Carbonfasern, entweder vorimprägniert oder mit Harz benetzt, werden in einem präzisen Muster auf einen rotierenden Dorn gewickelt. Sie eignen sich hervorragend für die Herstellung hohler, rotationssymmetrischer Teile wie Druckbehälter, Rohre und Antriebswellen und bieten ein sehr hohes Verhältnis von Festigkeit zu Gewicht in bestimmten Richtungen.
- Pultrusion:Ein kontinuierlicher Prozess, bei dem harzgetränkte Fasern durch eine beheizte Düse gezogen werden, um Profile mit konstantem Querschnitt (z. B. Stäbe, Balken, Rohre) zu bilden. Besonders effizient für lange, durchgehende Verbundteile mit hohem Faservolumenanteil (oft 60–70 %).
- Automatisierte Faserplatzierung (AFP) / Automatisiertes Tapelegen (ATL):Robotersysteme platzieren einzelne Prepreg-Bänder oder -Kabel präzise auf einer Formoberfläche. Diese hochautomatisierten Verfahren werden für große, komplexe Strukturen (z. B. Flugzeugflügel und Flugzeugrümpfe) eingesetzt, bei denen Präzision, Wiederholgenauigkeit und hoher Durchsatz entscheidend sind. Sie sind zwar kapitalintensiv, bieten aber bei großen Produktionsläufen erhebliche Arbeitseinsparungen.
- Leistung:Die Autoklavhärtung von Prepregs bietet höchste mechanische Eigenschaften, minimalen Porengehalt und höchste Konsistenz und ist daher unverzichtbar für die Luft- und Raumfahrt (z. B. besteht die Boeing 787 zu über 50 % aus Verbundwerkstoffen). Die Vakuuminfusion bietet eine gute Leistung zu geringeren Kosten als die Autoklavhärtung und eignet sich für Schiffs- oder Automobilkomponenten. RTM/Pressformung bietet eine gute Oberflächengüte und schnellere Zykluszeiten für Teile mittlerer bis hoher Stückzahlen.
- Kosten:Handlaminieren verursacht die niedrigsten Werkzeug- und Einrichtungskosten, verursacht aber hohe Arbeits- und Materialabfälle. Autoklav-Prepreg erfordert erhebliche Investitionen in Autoklaven, Reinräume und anspruchsvolle Werkzeuge. Dadurch steigen die Stückkosten bei geringen Stückzahlen, sind aber bei kritischen Hochleistungskomponenten gerechtfertigt. Automatisierte Prozesse (AFP/ATL) erfordern zwar die höchsten Investitionskosten, bieten aber Skaleneffekte bei sehr großen Produktionsmengen.
- Konsistenz und Wiederholbarkeit:Hochautomatisierte und kontrollierte Prozesse wie die Autoklavhärtung von Prepregs, RTM und AFP/ATL bieten höchste Konsistenz und Wiederholbarkeit, was für sicherheitskritische Komponenten und die Massenproduktion von größter Bedeutung ist.
- Design und Werkzeuge:Entwerfen des Teils und Erstellen von Formen (Werkzeugen), die den Aushärtungstemperaturen und -drücken standhalten. Werkzeuge können aus verschiedenen Materialien wie Invar, Aluminium oder Verbundwerkstoffen hergestellt werden.
- Materialvorbereitung:Zuschneiden von Kohlefasergeweben oder Prepregs in Form mit CNC-Schneidern, bei Prepregs häufig in einer Reinraumumgebung, um Verunreinigungen zu vermeiden.
- Aufbau:Die zugeschnittenen Lagen werden auf die Form gelegt. Dies kann manuell, halbautomatisch (Laserprojektionsführung) oder vollautomatisch (AFP/ATL) erfolgen. Die Faserausrichtung ist entscheidend für die Festigkeit.
- Harzimprägnierung (falls kein Prepreg):Beim Nasslaminieren oder Vakuuminfusionieren wird Harz auf den trockenen Faserstapel aufgetragen oder infundiert.
- Abfüllen (für vakuumunterstützte Prozesse):Versiegeln Sie das Teil mit einem Vakuumbeutel, um die Luft zu entfernen und das Laminat zu verdichten.
- Aushärtung:Durch Anwendung von Hitze und/oder Druck in einem Ofen oder Autoklaven wird das Harz polymerisiert. Der genaue Aushärtungszyklus (Temperaturanstiegsraten, Haltezeiten, Druckniveaus) ist entscheidend und wird oft vom Harzhersteller vorgegeben.
- Entformung:Entnehmen des ausgehärteten Teils aus der Form.
- Trimmen und Fertigstellen:Überschüssiges Material abschneiden, Löcher bohren und schleifen. Aufgrund der abrasiven Eigenschaften von Kohlefaser wird dies häufig mit diamantbeschichteten Werkzeugen durchgeführt.
- Nachhärten (optional):Einige Teile müssen möglicherweise zusätzlich erhitzt werden, um ihre mechanischen Eigenschaften voll zu entwickeln.
- Materialeingangsprüfung:Überprüfen der Spezifikationen, Chargennummern und Verfallsdaten der Rohmaterialien (Fasern, Harze, Prepregs) (bei Prepregs ist die Haltbarkeit im Gefrierschrank entscheidend).
- Prozessüberwachung:Echtzeitüberwachung von Temperatur, Druck, Vakuum und Aushärtungszyklen während der Fertigung. Die Nichteinhaltung dieser Parameter kann die Teilequalität erheblich beeinträchtigen.
- Sichtprüfung:Überprüfung auf Oberflächendefekte wie Hohlräume, Delaminationen, harz- oder faserreiche Bereiche, Fremdkörperablagerungen (FOD) und Oberflächenfehler.
- Maßprüfung:Verwenden Sie KMGs (Koordinatenmessgeräte) oder Laserscanner, um die Abmessungen, Toleranzen und Passungen der Teile zu überprüfen.
- Zerstörungsfreie Prüfung (NDT):Entscheidend für die Erkennung interner Defekte ohne Beschädigung des Teils.
- Ultraschallprüfung:Mithilfe von Impulsecho- oder Durchstrahlungstechniken lassen sich Hohlräume, Delaminationen und Faserfehlstellungen erkennen.
- Röntgenradiographie/CT-Scan:Bietet detaillierte interne Bilder, die zum Erkennen von Porosität, Fremdkörpern oder Faserknicken nützlich sind.
- Thermografie:Erkennt Defekte unter der Oberfläche durch die Analyse von Wärmeflussmustern.
- Zerstörende Prüfung (DT):Regelmäßig werden kleine Probenstücke aus Teilen oder speziellen Testplatten ausgeschnitten, um die mechanischen Eigenschaften (Zugfestigkeit, Druckfestigkeit, Scherfestigkeit, Biegefestigkeit) und den Faservolumenanteil zu überprüfen. Auch eine Analyse des Hohlraumgehalts wird durchgeführt.
- Rückverfolgbarkeit:Die sorgfältige Dokumentation von Rohstoffen, Prozessparametern und Prüfergebnissen für jedes Teil ermöglicht eine lückenlose Rückverfolgbarkeit vom Rohstoff bis zum fertigen Produkt. Dies ist eine gängige Anforderung in regulierten Branchen wie der Luft- und Raumfahrt.
Welchen Einfluss haben Herstellungsprozesse auf Leistung und Kosten industrieller Anwendungen?
Die Auswahl eines Herstellungsverfahrens ist ein kritischer Kompromiss zwischen gewünschter Leistung, Produktionsvolumen und Kosten. Für die Neubeschaffung ist es wichtig, diese Auswirkungen zu verstehen:
Welches sind die kritischen Schritte im Herstellungszyklus von Kohlenstofffaserverbundwerkstoffen?
Während die einzelnen Schritte je nach Prozess variieren, umfasst ein allgemeiner Fertigungszyklus:
Welche Maßnahmen zur Qualitätskontrolle sind für zuverlässige Kohlefaserteile unerlässlich?
Gewährleistung der Integrität und Leistung vonCarbonfaserteileist von größter Bedeutung, insbesondere bei kritischen Anwendungen. Zu den wichtigsten Maßnahmen der Qualitätskontrolle (QC) gehören:
Für Industrieanwender, die Kohlefaserteile erneut kaufen möchten, ist die Einhaltung strenger Qualitätskontrollen durch den Hersteller, nachgewiesen durch Zertifizierungen (z. B. AS9100 für die Luft- und Raumfahrt, ISO 9001), eine detaillierte Prozessdokumentation und ein robustes NDT-Programm, ein starker Indikator für Zuverlässigkeit und Leistungskonstanz.
BeiSupreme CarbonWir wissen, dass die Integrität Ihrer Carbonfaserkomponenten unverzichtbar ist. Wir nutzen modernste Fertigungsverfahren, darunter fortschrittliches Prepreg-Layup und Autoklavenhärtung, kombiniert mit strengen Qualitätskontrollprotokollen. Unser Engagement für die Verwendung hochwertiger Materialien und Präzisionstechnik stellt sicher, dass jedes von uns gelieferte Teil die anspruchsvollsten Leistungsspezifikationen erfüllt und Ihnen so höchste Zuverlässigkeit und einen Wettbewerbsvorteil in Ihrer Branche bietet. Mit Supreem Carbon wählen Sie einen Partner, der sich auf erstklassige Verbundlösungen spezialisiert hat.

Asiens führende Marke für Motorradzubehör aus Carbonfaser
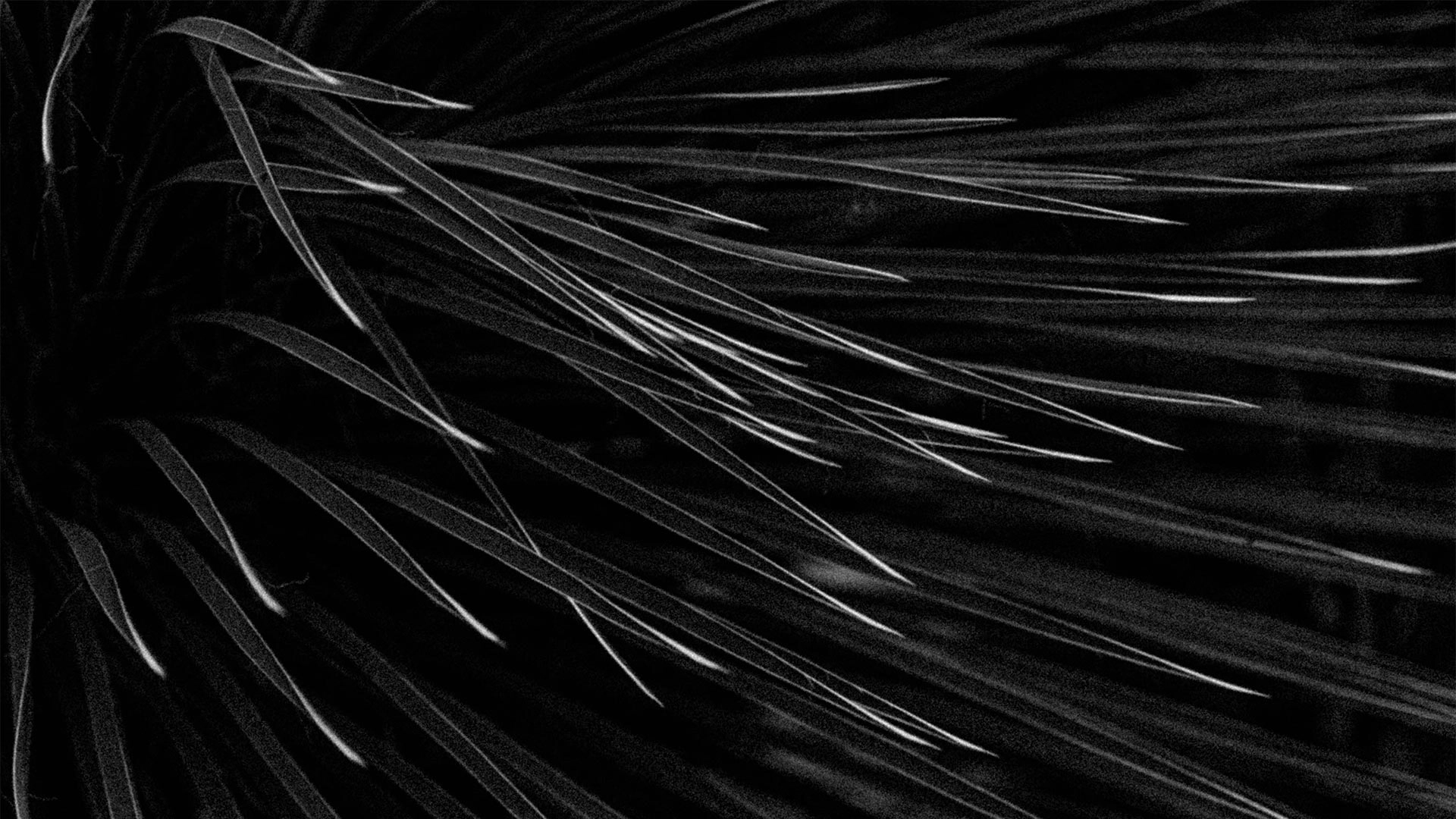
Enthüllung der Kohlefaser: 10 überraschende Wahrheiten und wie sie unsere Zukunft prägt
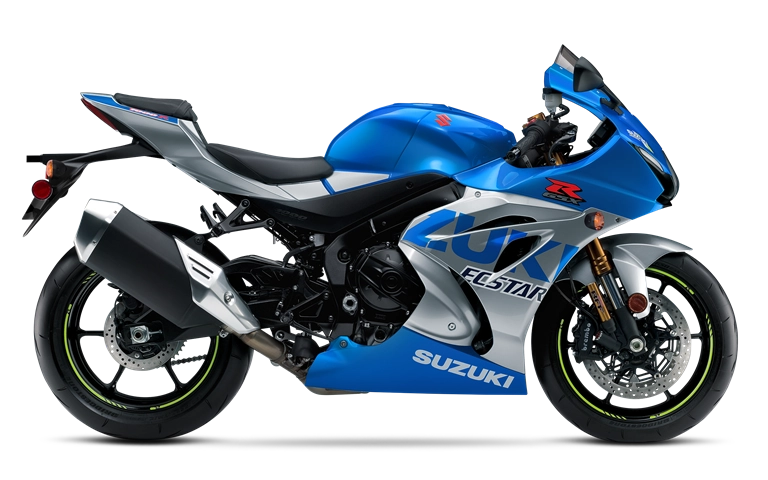
Entwicklungsplan für neue Kohlefaserteile für Fahrräder von Supreem Carbon.

Neu eingetroffen: Armaturenbrettverkleidung und Fenstertürverkleidungen aus 100 % Carbonfaser!

Neu eingetroffen: Vollcarbon-Sets für die BMW S1000RR 2020+.
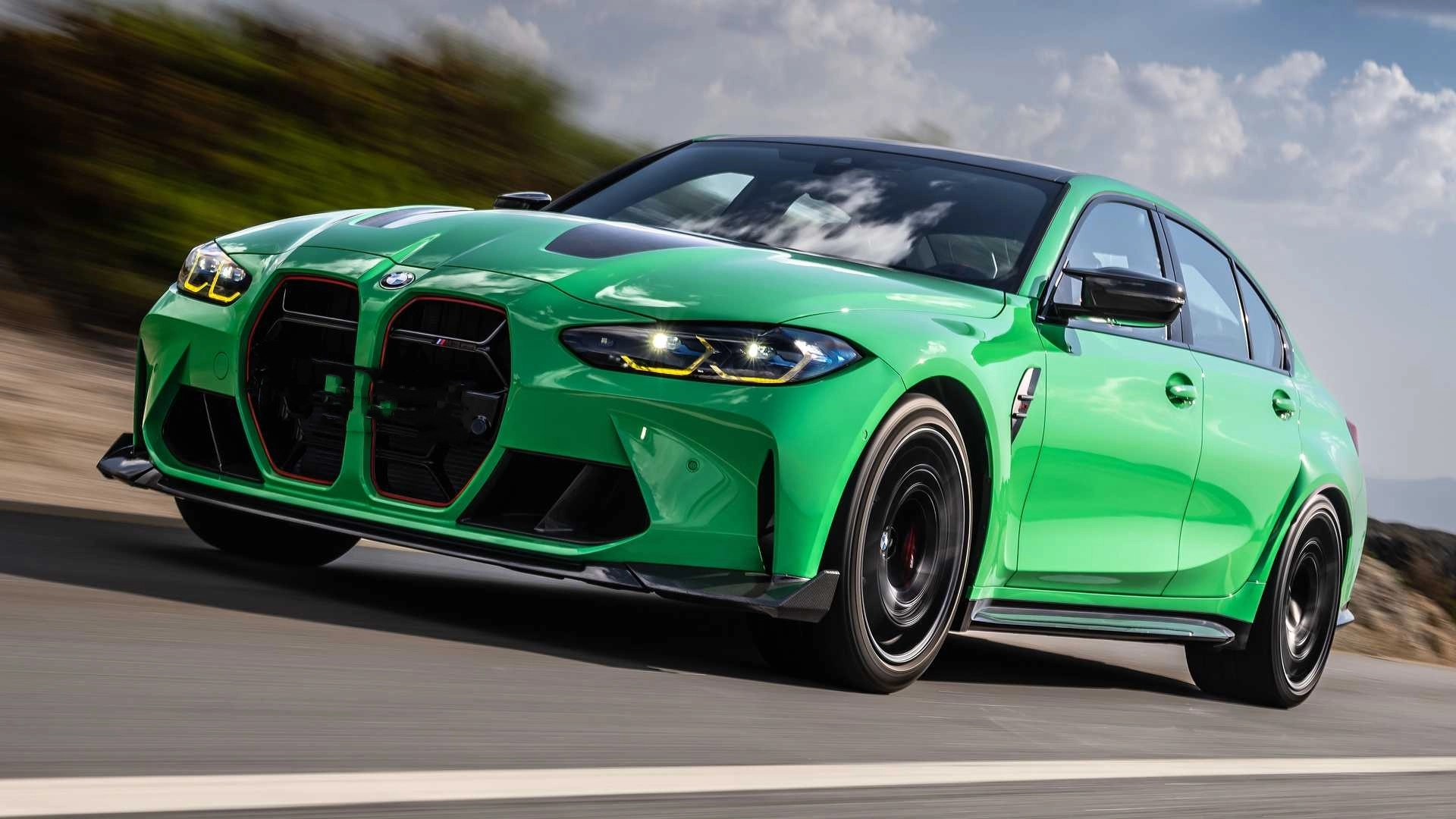
Die einflussreichste Marke eines Kohlefaserherstellers in Asien
Für den Kundendienst
Bieten Sie eine Garantie an?
Sechs Monate Standardgarantie auf alle Produkte. Schäden durch Installationsfehler oder Naturelemente sind nicht abgedeckt.
Wie kann ich die Bestellung stornieren?
Wir können Ihre Bestellung nur stornieren, wenn sie noch nicht ausgeführt wurde. Gerne unterstützen wir Sie bei allen Anpassungen, wenn Sie dies wünschen!
Für maßgeschneiderten Service
Was kann außer individuellen Kohlefaserteilen noch individuell angepasst werden?
Sie können Ihr Firmenlogo, die Verpackung und sogar die Farbe der Beschichtung usw. individuell anpassen.
Für Produkte
Welche Oberfläche könnten Sie für die Carbonteile realisieren?
Glanzoberfläche, Mattoberfläche, Satinoberfläche. Einige Farbbeschichtungen nach Kundenwunsch.
Wie kann ich eine Probe erhalten?
Derzeit stellen wir unseren Kunden keine kostenlosen Muster zur Verfügung. Sie können bei Bedarf jedoch eine Musterbestellung aufgeben.

Yamaha MT10 Auspuffabdeckung aus Karbonfaser

Chevrolet Corvette C8 Schaltwippen aus Kohlefaser
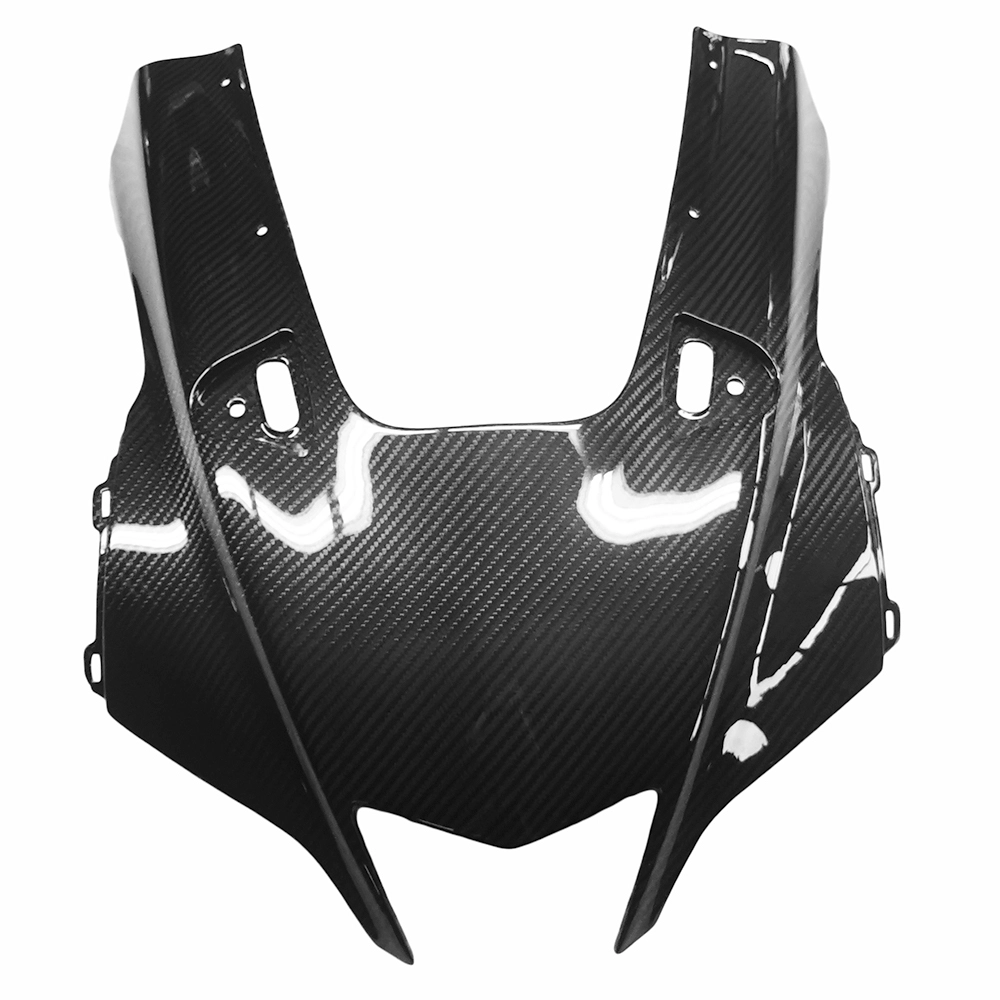
Yamaha R1 R1M Frontverkleidung aus Kohlefaser

Ducati Monster 937 Kettenradabdeckung aus Kohlefaser
Eine Nachricht hinterlassen
Haben Sie eine Frage oder Anfrage zu unseren Kohlefaserverbundprodukten? Hinterlassen Sie uns hier eine Nachricht und unser Team wird sich umgehend bei Ihnen melden.
Egal, ob Sie an Sonderanfertigungen, technischen Spezifikationen oder Partnerschaftsmöglichkeiten interessiert sind, wir sind hier, um Ihnen zu helfen.
Bitte füllen Sie die Felder oben mit Ihrem Namen, Ihrer E-Mail-Adresse und Ihrer Nachricht aus.
© 2024 Supreem Carbon. Alle Rechte vorbehalten.
auf facebook.
Pinterest
LinkedIn
Instagram