how are carbon fiber composites made | Supreem Carbon Expert Guide
How are Carbon Fiber Composites Made? Understanding the Core Processes
Carbon fiber composites stand at the forefront of advanced materials, revolutionizing industries from aerospace to automotive, and renewable energy to sporting goods. Their unparalleled strength-to-weight ratio and stiffness make them indispensable for high-performance applications. For industry users involved in re-procurement, a deep understanding of their manufacturing processes is crucial to ensure optimal performance, cost-efficiency, and reliability. Let's demystify how these remarkable materials are brought to life.
What are the foundational materials used in carbon fiber composites?
The performance of a carbon fiber composite part begins with its constituent materials: the carbon fibers and the matrix resin. Carbon fibers provide the strength and stiffness, while the resin binds them together, transfers load between fibers, and protects them from environmental damage.
- Carbon Fibers: These are typically derived from polyacrylonitrile (PAN) or pitch precursors through a complex process of stabilization, carbonization, and graphitization. Fibers are categorized by their modulus (stiffness) and strength. For instance, high-modulus (HM) fibers are used where stiffness is paramount (e.g., satellite structures), while high-strength (HS) fibers are preferred for impact resistance (e.g., aircraft fuselage). A common tow size used in industrial applications is 12K (12,000 filaments per tow) or 24K.
- Matrix Resins:
- Thermosets: These are the most common, curing irreversibly. Epoxy resins dominate the market, accounting for an estimated 70-80% of advanced composite applications, especially in aerospace, due to their excellent mechanical properties, adhesion, and thermal stability. Other thermosets include polyester and vinyl ester (for lower cost, less demanding applications), phenolic (for fire resistance), and BMI/polyimide (for high-temperature environments, often exceeding 200°C).
- Thermoplastics: Materials like PEEK (Polyether Ether Ketone) and PEI (Polyetherimide) offer superior toughness, impact resistance, infinite shelf life for prepregs, and recyclability. While processing is more complex and requires higher temperatures (PEEK melts around 343°C), they are gaining traction in high-performance sectors.
What are the primary manufacturing methods for carbon fiber composites?
The choice of manufacturing method significantly impacts the final part's properties, complexity, production volume, and cost. Here are the most prevalent techniques:
- Hand Lay-up/Wet Lay-up: Simplest method, where dry fabrics are manually placed into a mold and then saturated with liquid resin using brushes or rollers. Labor-intensive, low tooling cost, but inconsistent quality and high void content (often 5-10%). Suitable for prototypes or low-volume, non-critical parts.
- Vacuum Bagging/Vacuum Infusion (VARTM/LRTM): An advancement over hand lay-up. Dry fabrics are laid into a mold, a vacuum bag is sealed over them, and resin is drawn into the laminate by vacuum pressure. This significantly reduces void content (typically 1-5%) and improves fiber-to-resin ratio compared to hand lay-up. Ideal for medium-sized parts with moderate complexity.
- Prepreg Lay-up & Autoclave Curing: Considered the gold standard for high-performance composites. Pre-impregnated (prepreg) carbon fiber sheets (fibers already pre-impregnated with a precisely measured amount of resin and partially cured) are laid into a mold. The assembly is then vacuum bagged and cured under controlled temperature and pressure in an autoclave. This method yields the highest mechanical properties, lowest void content (often below 1-2%), and excellent surface finish. Widely used in aerospace and motorsports.
- Resin Transfer Molding (RTM) / Compression Molding: Dry fibers are placed into a closed, rigid mold. Resin is then injected under pressure (RTM) or a pre-catalyzed resin mixture is compressed between mold halves (compression molding). These methods are suitable for higher volume production of complex shapes with good surface finish on both sides. Tooling costs are high.
- Filament Winding: Continuous carbon fibers, either pre-impregnated or wet with resin, are wound onto a rotating mandrel in a precise pattern. Excellent for manufacturing hollow, rotationally symmetrical parts like pressure vessels, pipes, and drive shafts, offering very high strength-to-weight ratios in specific directions.
- Pultrusion: A continuous process where resin-impregnated fibers are pulled through a heated die to form constant cross-section profiles (e.g., rods, beams, tubes). Highly efficient for long, continuous composite parts with high fiber volume fractions (often 60-70%).
- Automated Fiber Placement (AFP) / Automated Tape Laying (ATL): Robotic systems precisely place individual prepreg tapes or tows onto a mold surface. These highly automated methods are used for large, complex structures (e.g., aircraft wings, fuselages) where precision, repeatability, and high throughput are critical. Capital intensive but offers significant labor savings for large production runs.
- Performance: Autoclave curing of prepregs offers the highest mechanical properties, minimal void content, and superior consistency, making it essential for aerospace (e.g., Boeing 787 utilizes over 50% composites by weight). Vacuum infusion offers good performance at a lower cost than autoclave, suitable for marine or automotive components. RTM/Compression molding provides good surface finish and faster cycle times for medium to high volume parts.
- Cost: Hand lay-up has the lowest tooling and initial setup cost, but high labor and material waste. Autoclave prepreg requires significant investment in autoclaves, cleanrooms, and sophisticated tooling, making the per-part cost higher for low volumes but justified for critical, high-performance components. Automated processes (AFP/ATL) have the highest capital expenditure but offer economies of scale for very large production volumes.
- Consistency & Repeatability: Highly automated and controlled processes like prepreg autoclave curing, RTM, and AFP/ATL offer superior consistency and repeatability, which is paramount for safety-critical components and large-scale manufacturing.
- Design and Tooling: Designing the part and creating molds (tooling) that withstand curing temperatures and pressures. Tools can be made from various materials like invar, aluminum, or composite materials themselves.
- Material Preparation: Cutting carbon fiber fabrics or prepregs to shape using CNC cutters, often in a cleanroom environment for prepregs to prevent contamination.
- Lay-up: Placing the cut plies onto the mold. This can be manual, semi-automated (laser projection guidance), or fully automated (AFP/ATL). Fiber orientation is critical for strength.
- Resin Impregnation (if not prepreg): For wet lay-up or vacuum infusion, resin is applied or infused into the dry fiber stack.
- Bagging (for vacuum-assisted processes): Sealing the part with a vacuum bag to evacuate air and compact the laminate.
- Curing: Applying heat and/or pressure in an oven or autoclave to polymerize the resin. The precise cure cycle (temperature ramp rates, hold times, pressure levels) is critical and often specified by the resin manufacturer.
- Demolding: Removing the cured part from the mold.
- Trimming and Finishing: Cutting away excess material, drilling holes, and sanding. Often done with diamond-coated tools due to the abrasive nature of carbon fiber.
- Post-Curing (Optional): Some parts may require additional heating to fully develop mechanical properties.
- Material Incoming Inspection: Verifying raw material (fiber, resin, prepreg) specifications, batch numbers, and expiry dates (for prepregs, freezer life is critical).
- Process Monitoring: Real-time monitoring of temperature, pressure, vacuum levels, and cure cycles during manufacturing. Non-conformance to these parameters can significantly affect part quality.
- Visual Inspection: Checking for surface defects like voids, delaminations, resin-rich or fiber-rich areas, foreign object debris (FOD), and surface imperfections.
- Dimensional Inspection: Using CMMs (Coordinate Measuring Machines) or laser scanners to verify part dimensions, tolerances, and fit.
- Non-Destructive Testing (NDT): Crucial for internal defect detection without damaging the part.
- Ultrasonic Inspection: Pulse-echo or through-transmission techniques detect voids, delaminations, and fiber misalignment.
- X-ray Radiography/CT Scanning: Provides detailed internal images, useful for detecting porosity, foreign objects, or fiber buckling.
- Thermography: Detects subsurface defects by analyzing heat flow patterns.
- Destructive Testing (DT): Periodically, small coupons are cut from parts or dedicated test panels to verify mechanical properties (tensile strength, compression strength, shear strength, flexural strength) and fiber volume fraction. Void content analysis is also performed.
- Traceability: Maintaining meticulous records of raw materials, process parameters, and inspection results for each part, allowing for full traceability from raw material to finished product. This is a common requirement in regulated industries like aerospace.
How do manufacturing processes impact performance and cost for industrial applications?
The selection of a manufacturing process is a critical trade-off between desired performance, production volume, and cost. For re-procurement, understanding these impacts is vital:
What are the critical steps in the carbon fiber composite fabrication cycle?
While specific steps vary by process, a general fabrication cycle involves:
What quality control measures are essential for reliable carbon fiber parts?
Ensuring the integrity and performance of carbon fiber parts is paramount, especially for critical applications. Key quality control (QC) measures include:
For industry users looking to re-purchase carbon fiber parts, a manufacturer's adherence to stringent quality control, demonstrated through certifications (e.g., AS9100 for aerospace, ISO 9001), detailed process documentation, and a robust NDT program, is a strong indicator of reliability and performance consistency.
At Supreem Carbon, we understand that the integrity of your carbon fiber components is non-negotiable. We leverage state-of-the-art manufacturing processes, including advanced prepreg lay-up and autoclave curing, combined with rigorous quality control protocols. Our commitment to using high-grade materials and precision engineering ensures that every part we deliver meets the most demanding performance specifications, providing you with unparalleled reliability and a competitive edge in your industry. When you choose Supreem Carbon, you choose a partner dedicated to superior composite solutions.
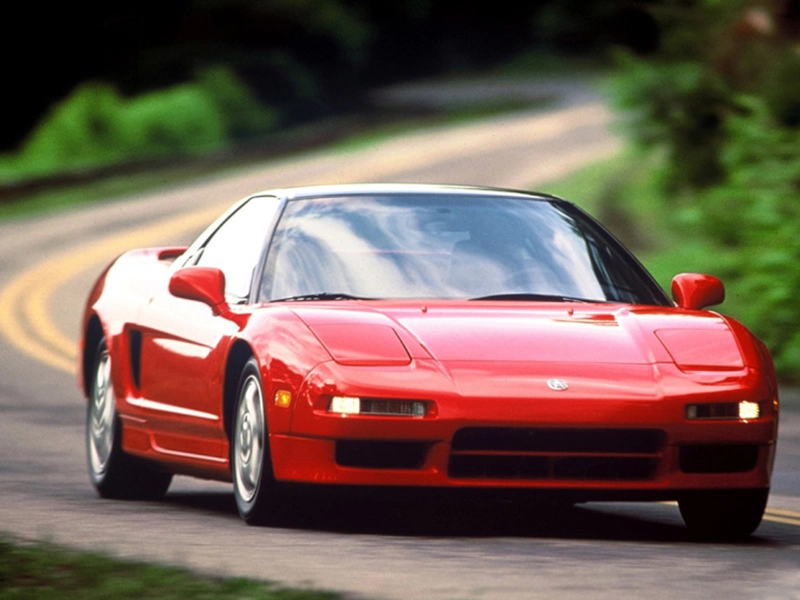
Chinese Carbon Fiber Manufacturer Brands: Supreem Carbon in the Spotlight

Lamborghini Urus engine compartment carbon fiber kit released by Supreem Carbon.
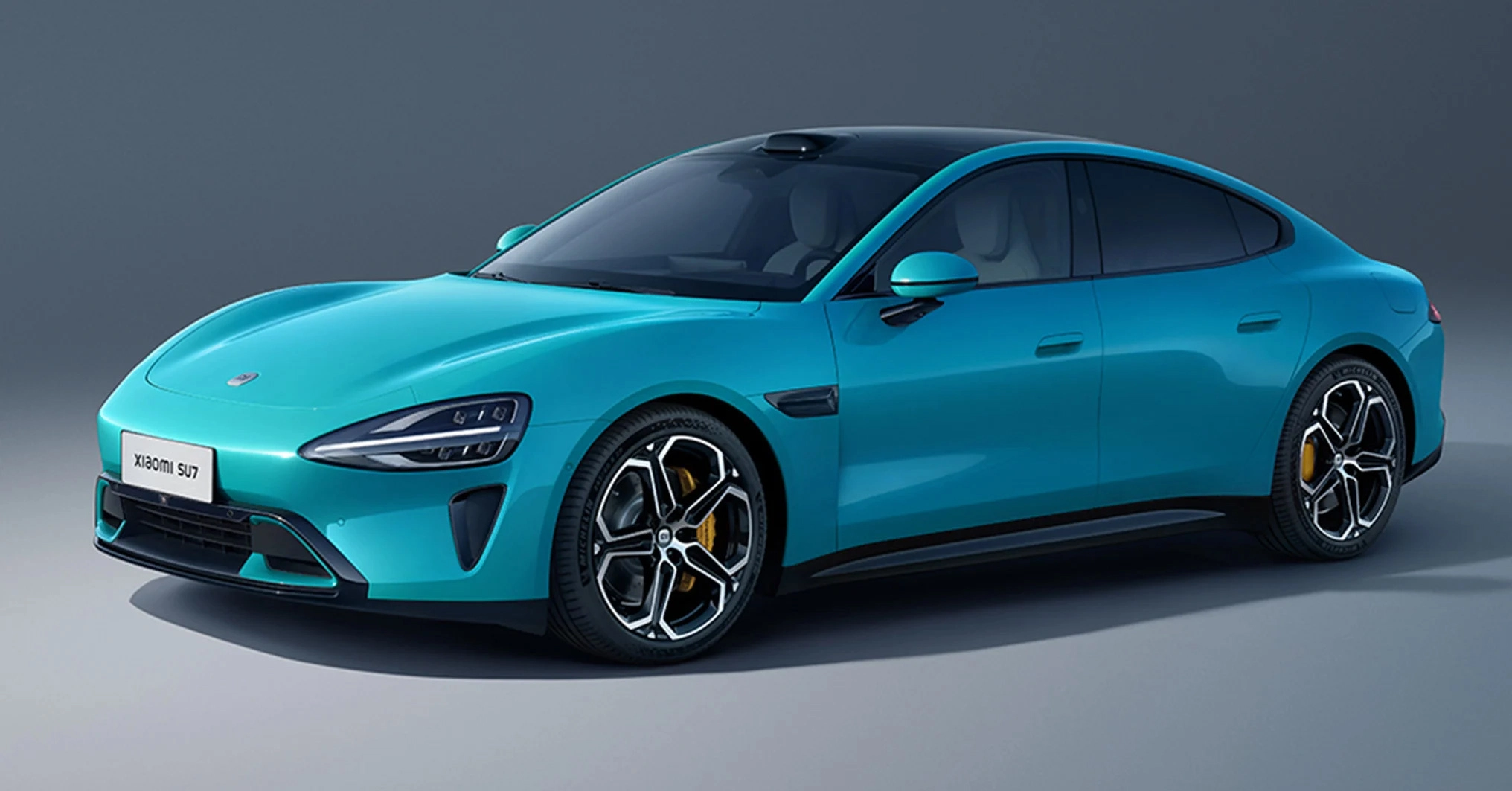
Custom Xiaomi SU7 Carbon Fiber Parts – Supreem Carbon
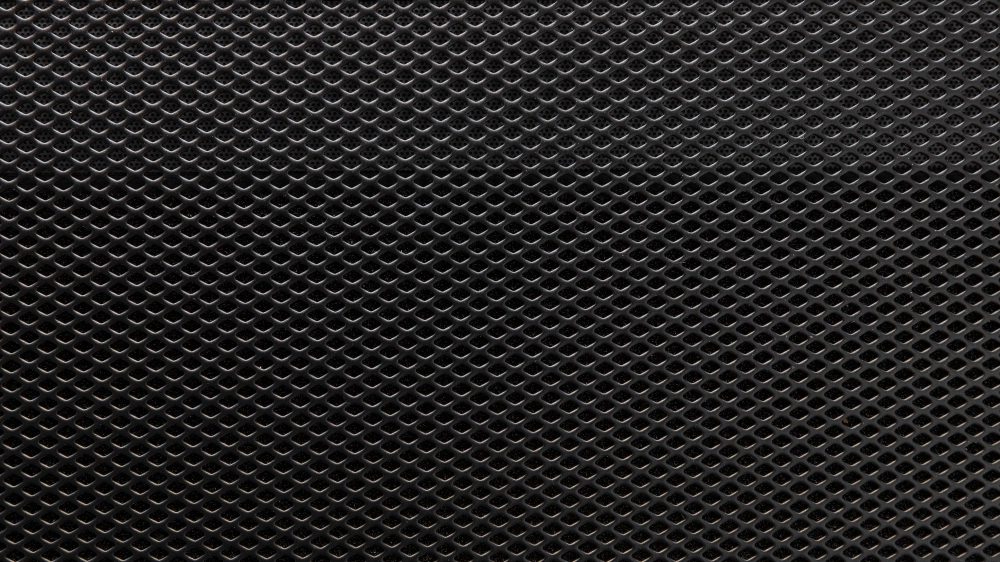
Carbon Fibers: What Are They and Why Are They Everywhere? (Production, Properties, and Uses Explained)
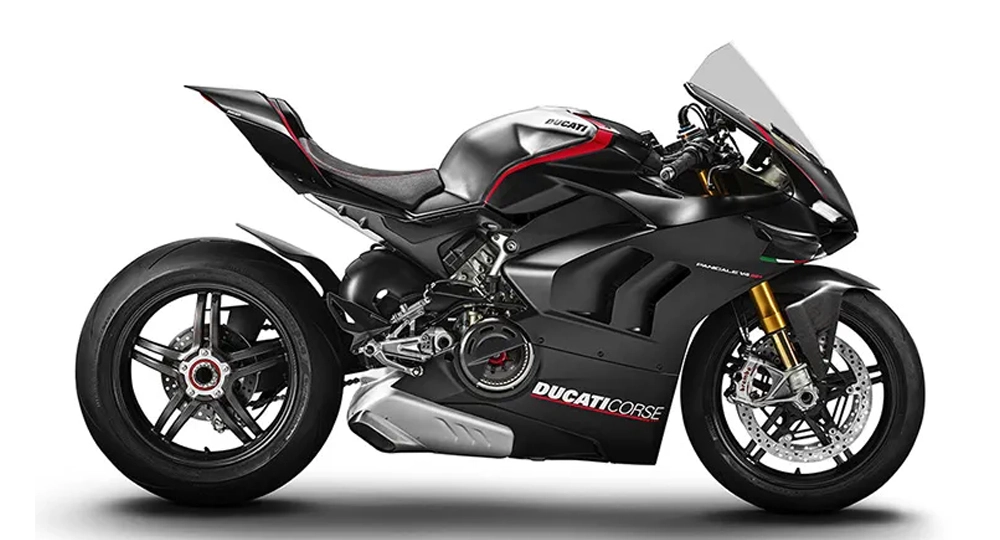
Great News!!! Ducati V4 SP new arrivals released.

2025 Ducati Panigale V4/V4S Carbon Fiber Body Kit released by Supreem Carbon.
For Customized Service
How long does the customized products order take?
This depends on the complexity and mold production cycle of the product. The first sample will be ready in 2-3 weeks after mold finished.
What custom customer need to prepare?
1. Send Your Design/Idea/3D drawing.
2. Supplier Quotation Confirmation.
3. Firts Sample Feedback.
For Products
Which carbon fiber material you can provide in production?
1*1 plain /2*2 twill / forged carbon / honeycomb / kevlar and so on.
Are you parts have UV protected?
Absolutely! We use multiple layers of premium quality automotive clear (or matt) coats on our products, which ensure that they will remain super pretty for years to come.
For After-sales Service
Do you offer a warranty?
Six month standard warranty on all products. Damage due to installation error or natural elements will not be covered.

BMW S1000RR Carbon Fiber Heel Plates Custom
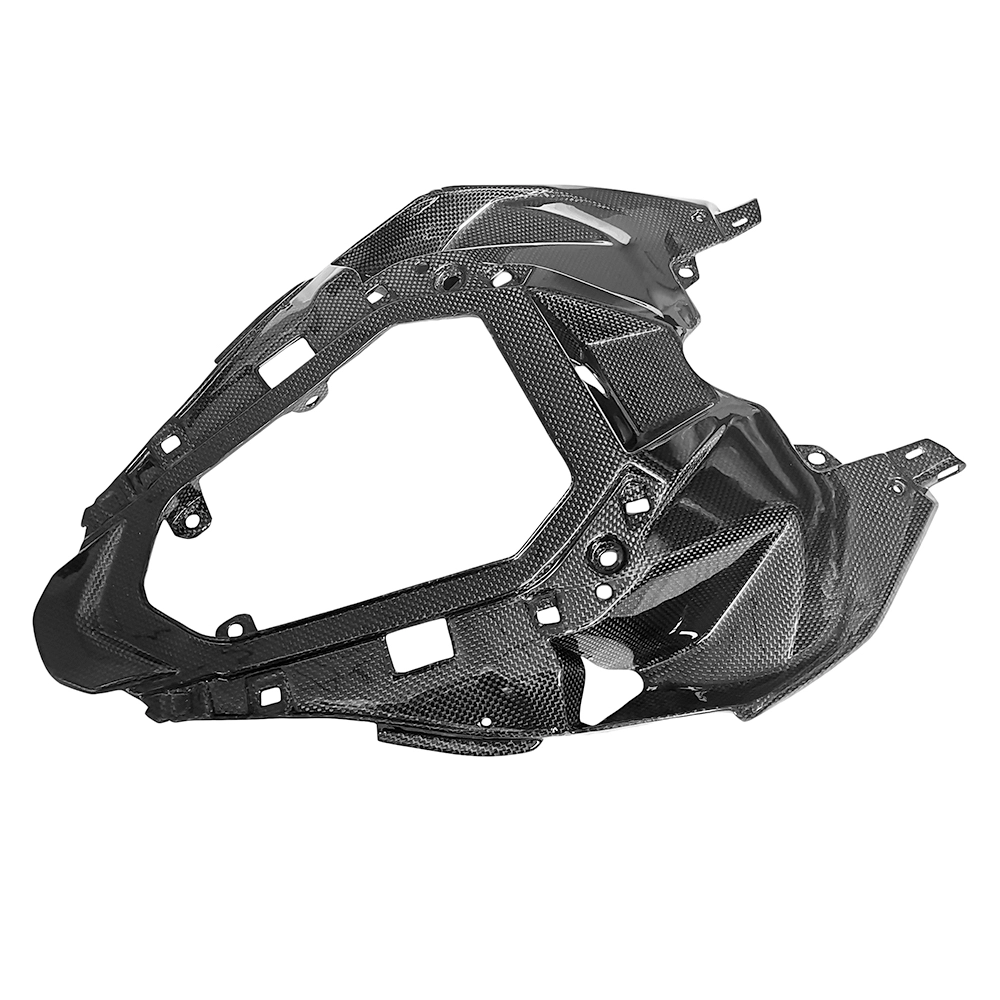
BMW S1000R Carbon Fiber Rear Seat Upper Fairing

Yamaha R1 Carbon Fiber Airbox Tank Cover
Introducing the Supreem Carbon Fiber Airbox Tank Cover for Yamaha R1. Crafted with precision and expertise, this tank cover is designed to elevate the performance and aesthetics of your R1. Made from high-quality carbon fiber, this tank cover is not only lightweight but also incredibly durable, providing optimal protection for your motorcycle.

Honda NSX Carbon Fiber Center Dash Panel Replacement
Leave a message
Have a question or inquiry about our carbon fiber composite products? Leave us a message here and our team will get back to you promptly.
Whether you're interested in custom orders, technical specifications, or partnership opportunities, we're here to assist you.
Please fill out the fields above with your name, email address, and message.
© 2024 Supreem Carbon All Rights Reserved.
Facebook
Pinterest
LinkedIn
Instagram