how much is a carbon fiber wrap corvette | Supreem Carbon Expert Guide
Unraveling the Cost and Value of Carbon Fiber for Your Corvette and Beyond
Carbon fiber has become synonymous with performance, luxury, and advanced engineering, especially in the automotive world. For Corvette enthusiasts, the allure of carbon fiber is undeniable, whether it's through an aesthetic wrap or functional lightweight components. This article delves into common questions surrounding carbon fiber applications for Corvettes and provides professional insights for industry procurement of carbon fiber parts, ensuring you make informed decisions.
How Much Does a Carbon Fiber Wrap for a Corvette Cost?
The cost of applying a carbon fiber vinyl wrap to a Corvette can vary significantly based on several factors, including the model of the Corvette, the quality of the vinyl material (e.g., 3M, Avery Dennison, KPMF), the complexity of the vehicle's contours, the extent of the wrap (full car vs. accents), and the installer's reputation and location. Generally, a high-quality full carbon fiber vinyl wrap for a Corvette can range from $2,500 to $8,000+. Partial wraps, such as for the hood, roof, or mirrors, would naturally be less expensive, typically ranging from a few hundred to over a thousand dollars. It’s crucial to obtain quotes from certified installers who offer warranties on both the material and their workmanship.
Carbon Fiber Wrap vs. Real Carbon Fiber Parts: What's the Difference?
This is a common point of confusion. A carbon fiber wrap is a vinyl film designed to mimic the appearance of woven carbon fiber. It's a cosmetic upgrade that is relatively affordable and reversible. It adds no significant structural integrity or weight reduction. In contrast, real carbon fiber parts are components actually manufactured from carbon fiber composite materials. These parts offer genuine performance benefits, including:
- Significant Weight Reduction: Real carbon fiber components can be 50-70% lighter than equivalent steel parts, dramatically improving power-to-weight ratios, handling, and fuel efficiency. For instance, high-performance Corvettes like the Z06 or ZR1 often utilize true carbon fiber for body panels, aero components, and even structural elements to shave critical pounds.
- Superior Strength and Stiffness: Carbon fiber boasts an exceptional strength-to-weight ratio, making parts incredibly rigid and durable, enhancing structural integrity and safety.
- Authentic Aesthetic: Genuine carbon fiber offers a unique, deep weave pattern and optical depth that a vinyl wrap cannot fully replicate. It often has a clear coat finish that highlights its intricate structure.
- Cost: Real carbon fiber parts are significantly more expensive than wraps due to complex manufacturing processes, high raw material costs, and specialized labor.
While a wrap is an excellent choice for a visual upgrade, real carbon fiber is chosen for performance enhancements and authenticity.
What is the Durability and Maintenance for Carbon Fiber Wraps?
The durability of a carbon fiber vinyl wrap largely depends on the quality of the material and the installation, as well as environmental factors and maintenance. High-quality vinyl wraps from reputable brands typically last anywhere from 5 to 7 years, while cheaper alternatives might only last 2-3 years. Exposure to harsh UV rays, extreme temperatures, and improper cleaning can shorten its lifespan.
Maintaining a carbon fiber wrap is similar to caring for car paint: gentle hand washing with pH-neutral car soap, avoiding abrasive cleaners or brushes, and immediate removal of contaminants like bird droppings or tree sap. It's also advisable to avoid automatic car washes, which can damage the wrap over time.
Why Choose Real Carbon Fiber Parts in Automotive Applications?
Beyond the aesthetic appeal, the adoption of real carbon fiber in the automotive industry, particularly in high-performance vehicles like the Corvette, is driven by its unparalleled functional advantages:
- Lightweighting: This is the primary driver. In an era of increasing fuel efficiency standards and the push for electric vehicles, reducing vehicle weight is paramount. Carbon fiber allows for substantial weight savings without compromising strength, directly translating to improved acceleration, braking, handling, and reduced emissions.
- Enhanced Performance: Lighter vehicles can accelerate faster, corner more sharply due to reduced unsprung mass, and stop in shorter distances. The stiffness of carbon fiber also contributes to better chassis dynamics and reduced body flex.
- Durability and Corrosion Resistance: Unlike metals, carbon fiber does not rust or corrode, making it ideal for components exposed to harsh environments.
- Design Flexibility: Composites can be molded into complex geometries, enabling innovative designs that are difficult or impossible to achieve with traditional metal stamping.
The global carbon fiber market continues to grow, valued at approximately USD 5.7 billion in 2022 and projected to expand significantly, driven largely by demand from the aerospace and automotive sectors for lightweighting solutions.
Essential Professional Knowledge for Procuring Carbon Fiber Parts
For industry professionals involved in procuring carbon fiber components, understanding the nuances of these advanced materials is critical for successful projects. Here are key considerations:
- Material Types and Forms: Understand the difference between PAN-based (polyacrylonitrile) and Pitch-based carbon fibers, which offer different properties (e.g., standard modulus vs. ultra-high modulus). Consider the form of the material required: continuous tow, woven fabrics, unidirectional tapes, or prepregs, which affect the manufacturing process and final part properties.
- Manufacturing Processes: The method of manufacturing significantly impacts cost, quality, and production volume. Common methods include:
- Autoclave Curing: Produces the highest quality, lowest void content parts, often used for aerospace and high-performance automotive. High tooling and energy costs.
- Resin Transfer Molding (RTM): Faster cycle times, good for medium to high volume, lower void content than open molding.
- Compression Molding: High volume production, often used for structural automotive components.
- Hand Lay-up/Vacuum Bagging: Cost-effective for prototyping or very low volume, but labor-intensive and prone to higher void content.
- Quality Control and Testing: Specify strict quality control measures. This includes mechanical property testing (tensile, compression, shear strength), void content analysis, and non-destructive testing (NDT) methods like ultrasonic inspection. Requesting supplier certifications (e.g., AS9100 for aerospace, IATF 16949 for automotive) is crucial.
- Cost Drivers: Be aware that raw material cost (carbon fiber tow and resin systems), tooling expenses, labor, energy consumption, and scrap rates are significant contributors to the final part cost. Higher volumes can often amortize tooling costs and reduce per-part prices.
- Supply Chain Management: Carbon fiber is a global commodity, and supply chain disruptions can impact lead times and pricing. Diversify suppliers if possible, and understand geopolitical factors affecting raw material availability. Intellectual property protection for proprietary designs and processes is also vital.
- Sustainability and Lifecycle: While carbon fiber offers performance benefits, its end-of-life recycling is challenging. Inquire about your suppliers' sustainability initiatives, including efforts in recycling carbon fiber composites through pyrolysis or solvolysis, and life cycle assessment data.
By understanding these complexities, industry professionals can navigate the carbon fiber market more effectively, ensuring the procurement of high-quality, cost-effective, and performance-optimized components for their applications.
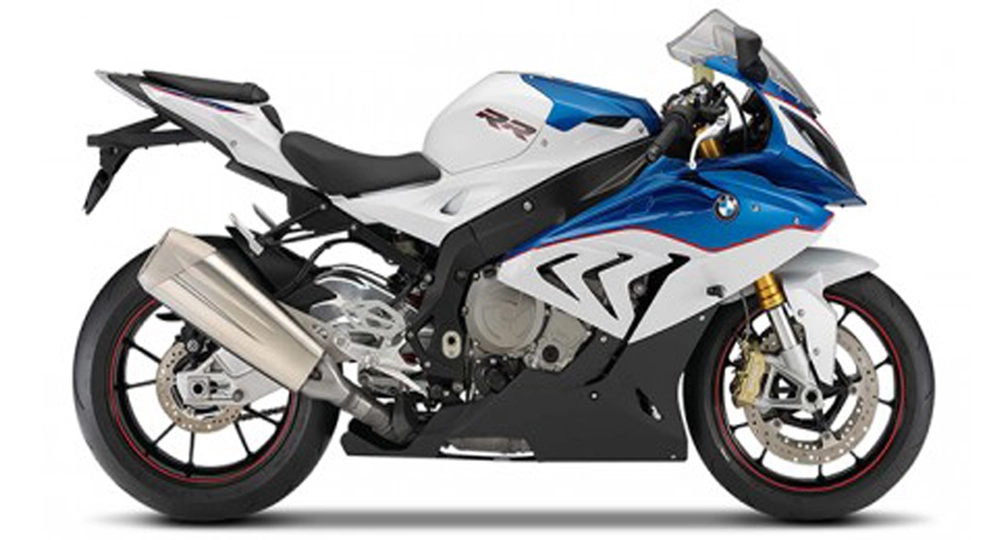
Supreem Carbon new arrivals released!

Ducati DesertX 2022 new arrivals!
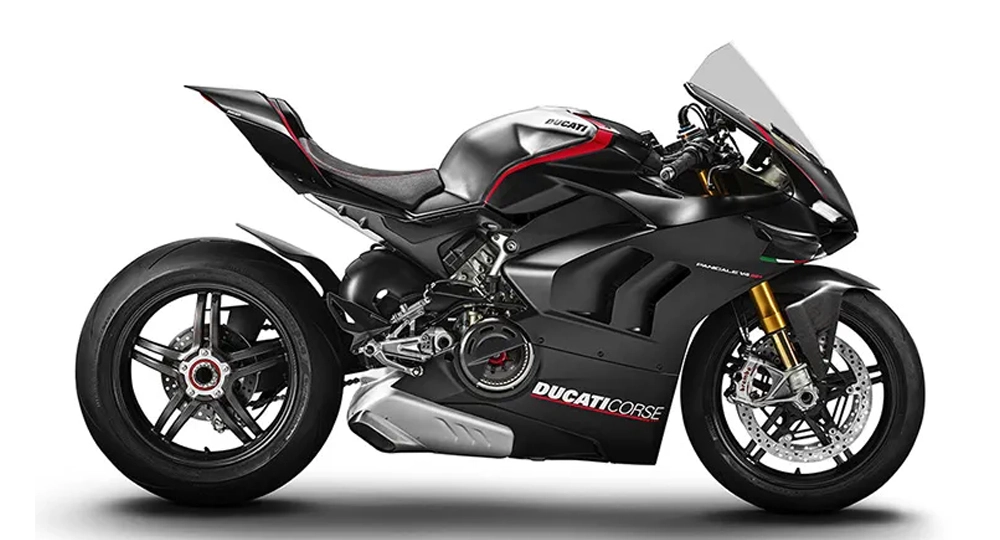
Great News!!! Ducati V4 SP new arrivals released.
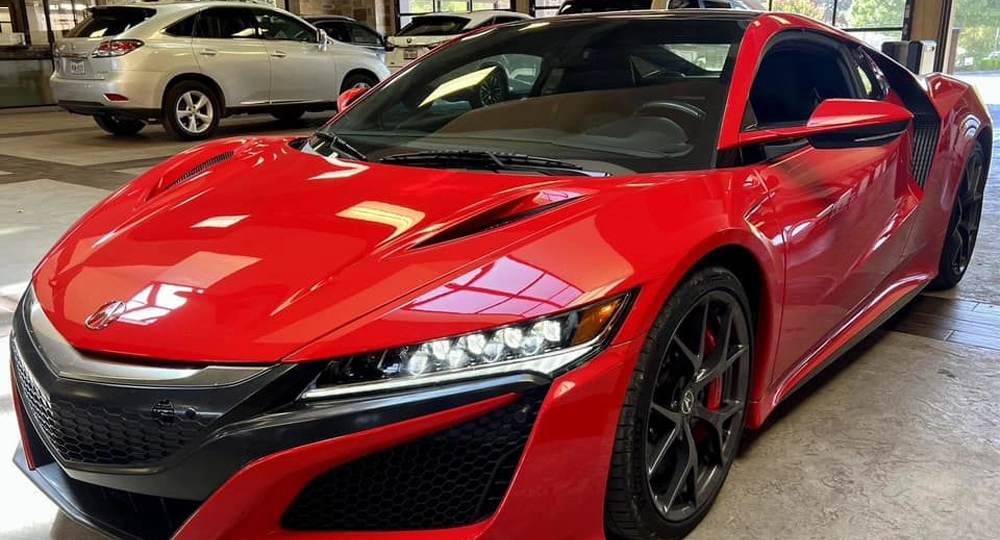
Supreem carbon Honda-NSX 100% Fiber Door Handle released!

Supreem carbon new carbon fiber engine cover for GR Yaris.
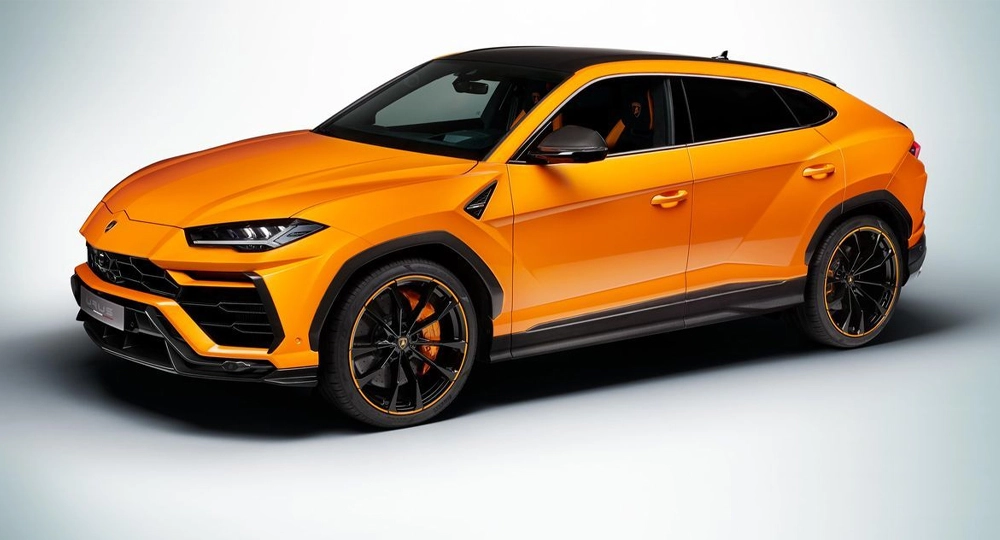
Supreem Carbon new engine cover released!
For Facotry
How many employees of Supreem carbon?
We have over 50 employees, including over 40 skilled workers, 3 R&D designers, and 5 QC professionals and so on.
For Order Delivery
What is the shipping time for the different ways?
Express delivery 5-7 days.
20-25 days by sea.
15 days by air.
For Customized Service
How long does the customized products order take?
This depends on the complexity and mold production cycle of the product. The first sample will be ready in 2-3 weeks after mold finished.
For Products
Which carbon fiber material you can provide in production?
1*1 plain /2*2 twill / forged carbon / honeycomb / kevlar and so on.
For After-sales Service
What can I do if the carbon fiber products arrived is broken?
Please give us feedback as soon as possible and we will send new one to you.

BMW S1000R/M1000RR Carbon Fiber Rear Seat Panel
Transform your BMW S1000RR/M1000RR with a premium carbon fiber rear seat upper fairing. Replace the stock plastic for a weight reduction and a sophisticated, racing-inspired aesthetic. This ultra-strong fairing offers superior protection while enhancing your bike's overall look. Choose between a glossy or matte finish for a perfect match.

KTM 1290 Super Duke R Carbon Fiber Rear Fender
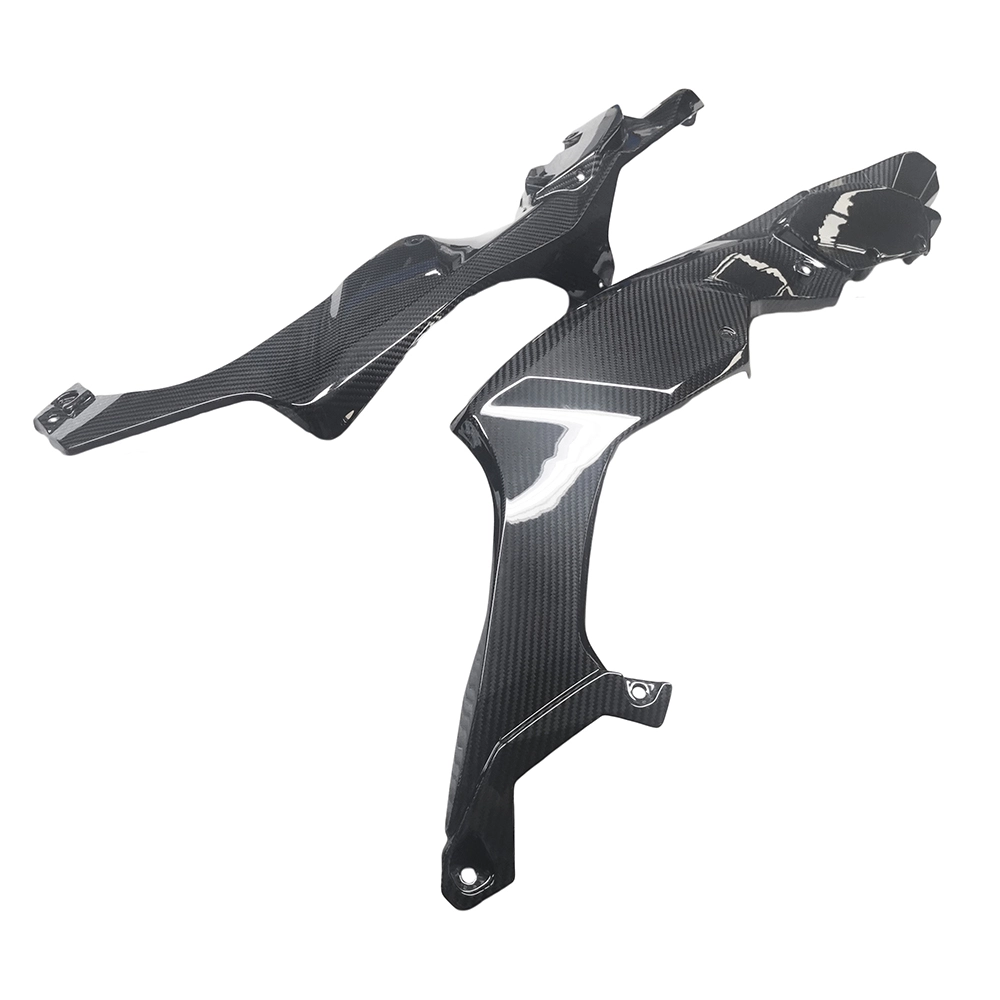
Kawasaki ZX10R Carbon Fiber Long Side Panels

Honda NSX Carbon Fiber Interior Door Handles Replacement
Leave a message
Have a question or inquiry about our carbon fiber composite products? Leave us a message here and our team will get back to you promptly.
Whether you're interested in custom orders, technical specifications, or partnership opportunities, we're here to assist you.
Please fill out the fields above with your name, email address, and message.
© 2024 Supreem Carbon All Rights Reserved.
Facebook
Pinterest
LinkedIn
Instagram