is carbon fiber a composite | Supreem Carbon Expert Guide
Is Carbon Fiber a Composite? Understanding the Material for Industrial Procurement
For procurement professionals in the advanced materials sector, understanding the fundamental nature of carbon fiber is crucial. The direct answer is unequivocally yes, carbon fiber is a composite material. This distinction is vital because its composite nature is precisely what imbues it with its remarkable properties, making it an indispensable material across a myriad of high-performance industrial applications.
What Exactly Makes Carbon Fiber a Composite Material?
A composite material is defined as a material made from two or more constituent materials with significantly different physical or chemical properties that remain separate and distinct at the macroscopic or microscopic level within the finished structure. In the case of carbon fiber, it typically consists of two primary components:
- Carbon Fibers (Reinforcement): These are extremely thin, strong, and stiff filaments of carbon, typically 5-10 micrometers in diameter. They provide the exceptional strength and stiffness.
- Resin Matrix (Binder): This is a polymeric material, often epoxy, vinyl ester, or polyester, that binds the carbon fibers together. The matrix protects the fibers from damage, transfers loads between fibers, and provides the part's shape and surface finish.
The combination of these two elements leverages the strengths of each, creating a material superior to its individual components.
What are the Key Components of Carbon Fiber Composites?
Beyond the fundamental fibers and matrix, understanding the nuances of these components is key for procurement:
- Carbon Fibers: The performance of the final composite is heavily dependent on the type of carbon fiber used. These can vary in strength (e.g., High Strength - HS, Intermediate Modulus - IM, High Modulus - HM) and tow size (e.g., 3K, 6K, 12K, 24K, representing thousands of filaments per tow). Torayca T800S or T1000G are examples of high-performance fibers.
- Resin Matrix:
- Epoxy Resin: Most common due to excellent adhesion, mechanical properties, and chemical resistance. Used widely in aerospace and high-performance automotive parts.
- Vinyl Ester Resin: Offers good chemical and corrosion resistance, and better impact strength than polyester, often used in marine and industrial applications.
- Polyester Resin: More cost-effective, but with lower mechanical properties compared to epoxy. Suitable for less demanding applications.
- Thermoplastic Matrices (e.g., PEEK, PEI): Offer higher toughness, impact resistance, and recyclability, gaining traction in high-temperature and structural applications.
- Additives: Tougheners, UV stabilizers, fire retardants, and processing aids can be added to the resin to enhance specific properties.
What are the Primary Advantages of Carbon Fiber Composites for Industrial Applications?
The benefits of carbon fiber composites translate directly into performance and cost efficiencies for industrial procurement:
- Exceptional Strength-to-Weight Ratio: Carbon fiber composites are significantly lighter than traditional metals while offering comparable or superior strength. For example, carbon fiber composites typically have densities ranging from 1.5 to 1.8 g/cm³, compared to aluminum at ~2.7 g/cm³ and steel at ~7.85 g/cm³. This leads to fuel efficiency in transport, reduced inertia in moving parts, and easier handling.
- High Stiffness: With high Young's Modulus values (e.g., standard carbon fibers can range from 230 to 250 GPa, while some HM fibers exceed 600 GPa), carbon fiber parts exhibit minimal deformation under load, crucial for precision machinery and structures.
- Corrosion Resistance: Carbon fibers themselves are chemically inert and do not corrode. When paired with appropriate resins, the composite exhibits excellent resistance to chemicals, moisture, and extreme environments, extending product lifespan and reducing maintenance.
- Fatigue Resistance: Carbon fiber composites generally have superior fatigue properties compared to metals, meaning they can withstand repetitive loading cycles for longer periods without failure, critical for components in dynamic applications.
- Low Thermal Expansion: Their low coefficient of thermal expansion contributes to dimensional stability across varying temperatures, important for precision instruments and aerospace components.
What are the Different Types of Carbon Fiber Composites Available for Procurement?
Understanding the common forms helps in selecting the right material for a specific application:
- Unidirectional (UD) Composites: All fibers run in a single direction, maximizing strength and stiffness along that axis. Ideal for components requiring strength primarily in one direction, like spars or beams.
- Woven Composites: Fibers are woven into fabrics (e.g., plain weave, twill weave, satin weave). These offer good bi-directional strength, drapeability, and aesthetic appeal. Common weave patterns include 2x2 twill or plain weave.
- Chopped Fiber Composites: Short, chopped carbon fibers are mixed with resin and can be compression molded or injection molded. Offers isotropic properties (strength in all directions) but generally lower mechanical properties than continuous fiber composites. Useful for complex shapes and mass production.
- Prepregs: Pre-impregnated materials where fibers are pre-coated with a precisely measured amount of resin, providing excellent consistency and mechanical properties. Typically require curing in an autoclave or oven.
How Do Carbon Fiber Composites Compare to Traditional Metals (e.g., Steel, Aluminum) in Industrial Use?
When considering material selection, a direct comparison is often necessary:
- Strength-to-Weight Ratio: Carbon fiber composites outperform both steel and aluminum significantly. For instance, high-strength carbon fiber composites can have specific strengths 5 to 10 times higher than steel and 2 to 3 times higher than aluminum.
- Stiffness: While steel generally has a higher absolute Young's Modulus, carbon fiber's specific stiffness (stiffness-to-weight) is vastly superior. This allows for lighter, yet equally stiff, structures.
- Corrosion: Metals like steel are prone to rust and aluminum can corrode in certain environments, requiring protective coatings. Carbon fiber composites are inherently corrosion-resistant, reducing long-term maintenance costs.
- Fatigue Life: Carbon fiber composites typically exhibit excellent fatigue resistance, often outperforming metals in applications with cyclic loading.
- Manufacturing Complexity & Cost: Initial material costs for carbon fiber are generally higher than metals. However, complex parts can often be manufactured as a single piece with composites (part consolidation), reducing assembly costs, welding, and fasteners. For instance, a complex metal assembly might require multiple stamping and welding steps, whereas a carbon fiber part could be molded in one go. Tooling costs can be higher for composites, but unit costs can decrease with higher volumes due to efficient molding processes.
- Damping Properties: Carbon fiber composites have better vibration damping characteristics than metals, which can be beneficial in machinery to reduce noise and wear.
ly, the choice between carbon fiber composites and metals depends on the specific application's requirements for weight, strength, stiffness, environmental resistance, and long-term cost-effectiveness.
Conclusion: Carbon fiber's identity as a composite material is fundamental to its high-performance capabilities. For procurement professionals, a deep understanding of its constituent parts, manifold advantages, and diverse forms is essential for making strategic material selections. By leveraging the unique properties of carbon fiber composites, industries can achieve significant advancements in performance, efficiency, and durability of their products.
Why Choose Supreem Carbon for Your Procurement Needs?
Supreem Carbon stands as a leader in providing high-quality carbon fiber parts for industrial applications. We understand the stringent demands of modern manufacturing and offer solutions that deliver on performance and reliability. Our advantages include:
- Expertise & Customization: Deep technical knowledge to assist in material selection and provide custom carbon fiber solutions tailored to your specific engineering requirements and application needs.
- Uncompromising Quality: Utilizing High Quality carbon fibers and state-of-the-art manufacturing processes to ensure superior mechanical properties, dimensional accuracy, and consistent performance across all parts.
- Reliable Supply Chain: A robust and efficient supply chain ensures timely delivery, minimizing downtime and supporting your production schedules seamlessly.
- Cost-Effectiveness in the Long Run: While focusing on quality, we also emphasize providing solutions that offer optimal total cost of ownership through enhanced durability, reduced weight, and improved performance of your end products.
- Technical Support: Our team of engineers and material specialists is available to provide comprehensive technical support, from design consultation to post-delivery assistance, ensuring you harness the full potential of carbon fiber composites.
Partner with Supreem Carbon to elevate your industrial products with the power of advanced carbon fiber composites.

New arrivals---Carbon Fiber Slam Panel Replacement for BMW M3 M4
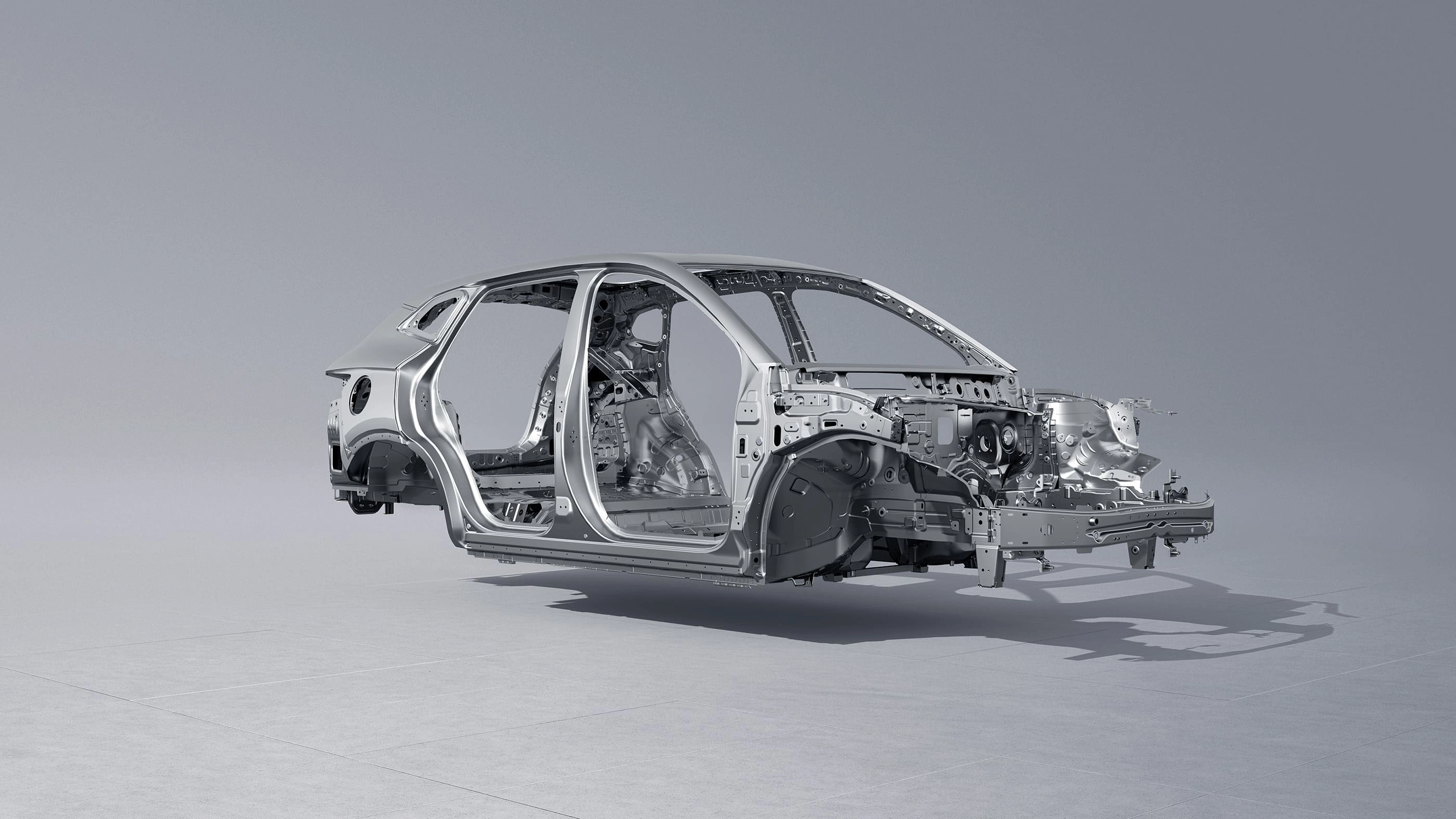
How to Make Carbon Fiber Car Parts?
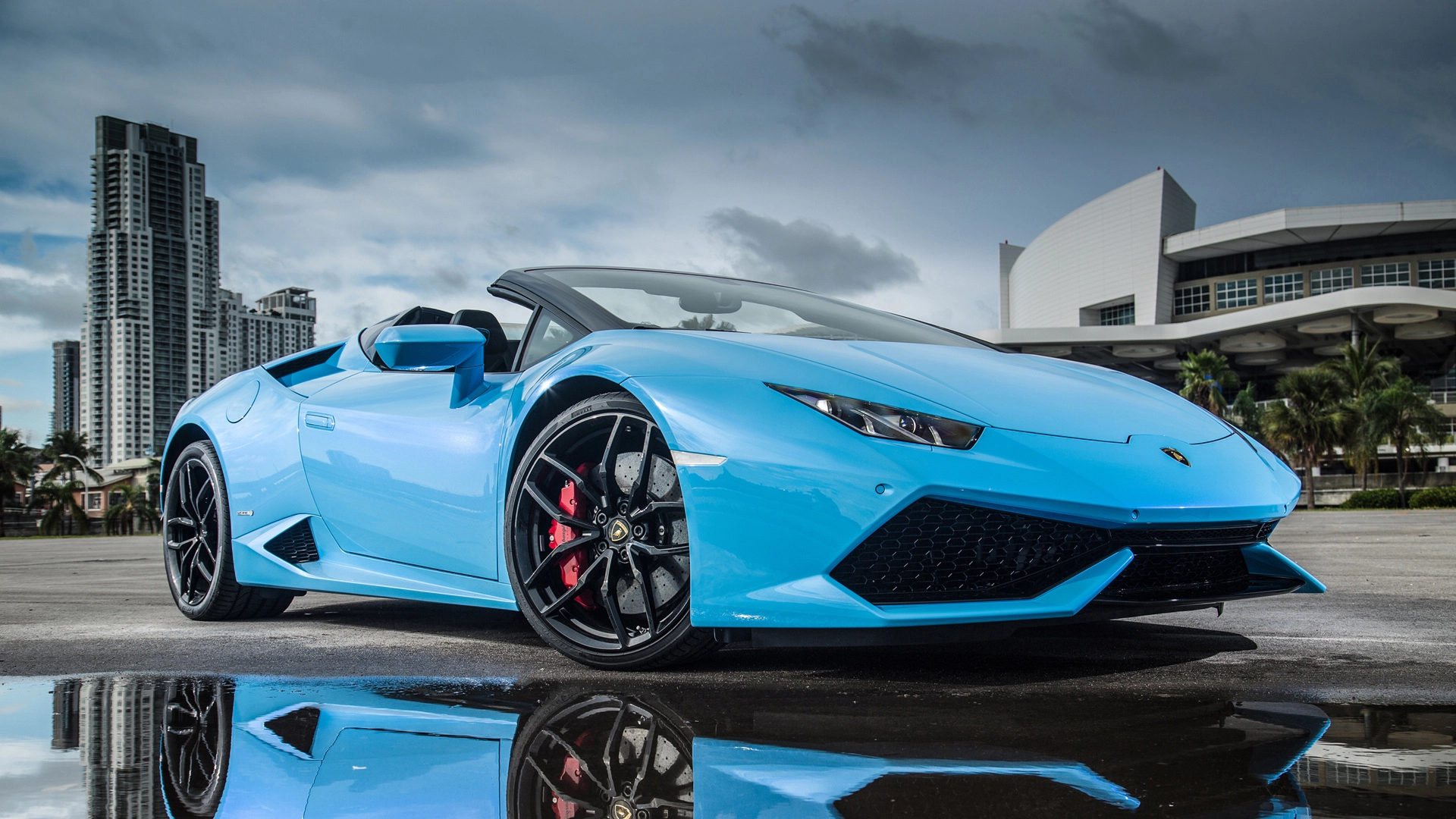
Research on the Causes of Yellowing of Carbon Fiber Products.

Le fabricant leader de fibre de carbone personnalisée en Europe
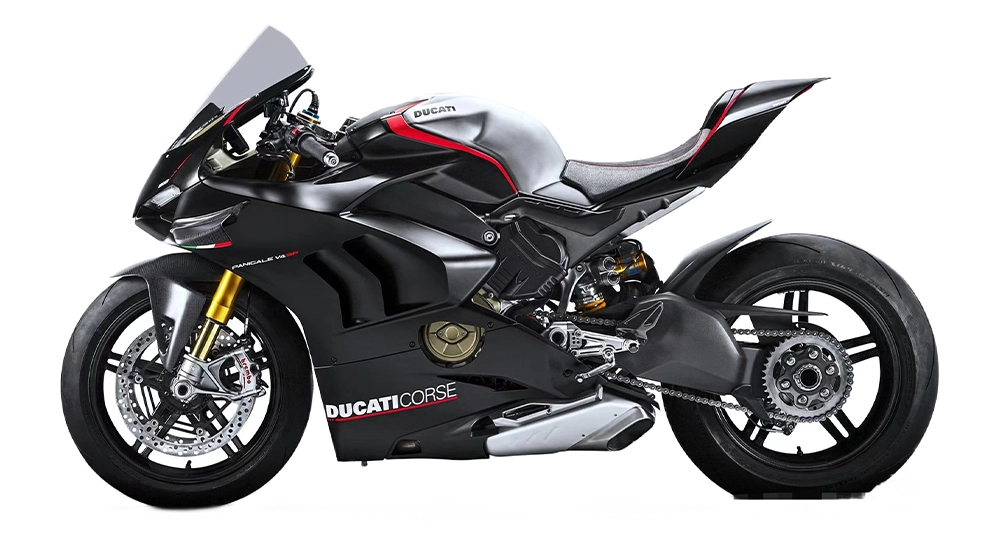
Supreem Carbon New arrivals alert!
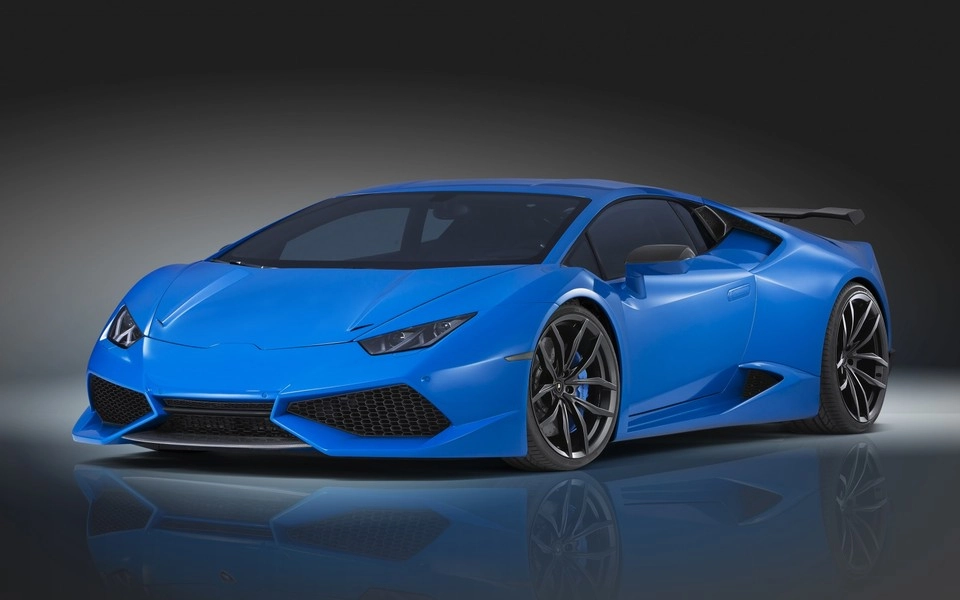
Is carbon fiber good for cars?
For Products
Which surface could you provide for the carbon parts?
Gloss finish, matte finish, satin finish. Some color coating as the customer needs.
For Customized Service
How long does the customized products order take?
This depends on the complexity and mold production cycle of the product. The first sample will be ready in 2-3 weeks after mold finished.
What is the customization process of carbon fiber products?
1. Customer provide 3D drawing, design requirement or idea
2. Technician evaluate project feasibility and provide a quotation
3. Project confirmation and arrange sample production
4. Delivery and customer feedback
5. Big scale orders production
For After-sales Service
How can I cancel the order?
We may only cancel your order if it has not been fulfilled yet. We would be more than happy to assist you with any adjustments if you'd wish instead!
For Order Delivery
What is the shipping time for the different ways?
Express delivery 5-7 days.
20-25 days by sea.
15 days by air.

Chevrolet Corvette C8 Carbon Fiber Paddle Shifters
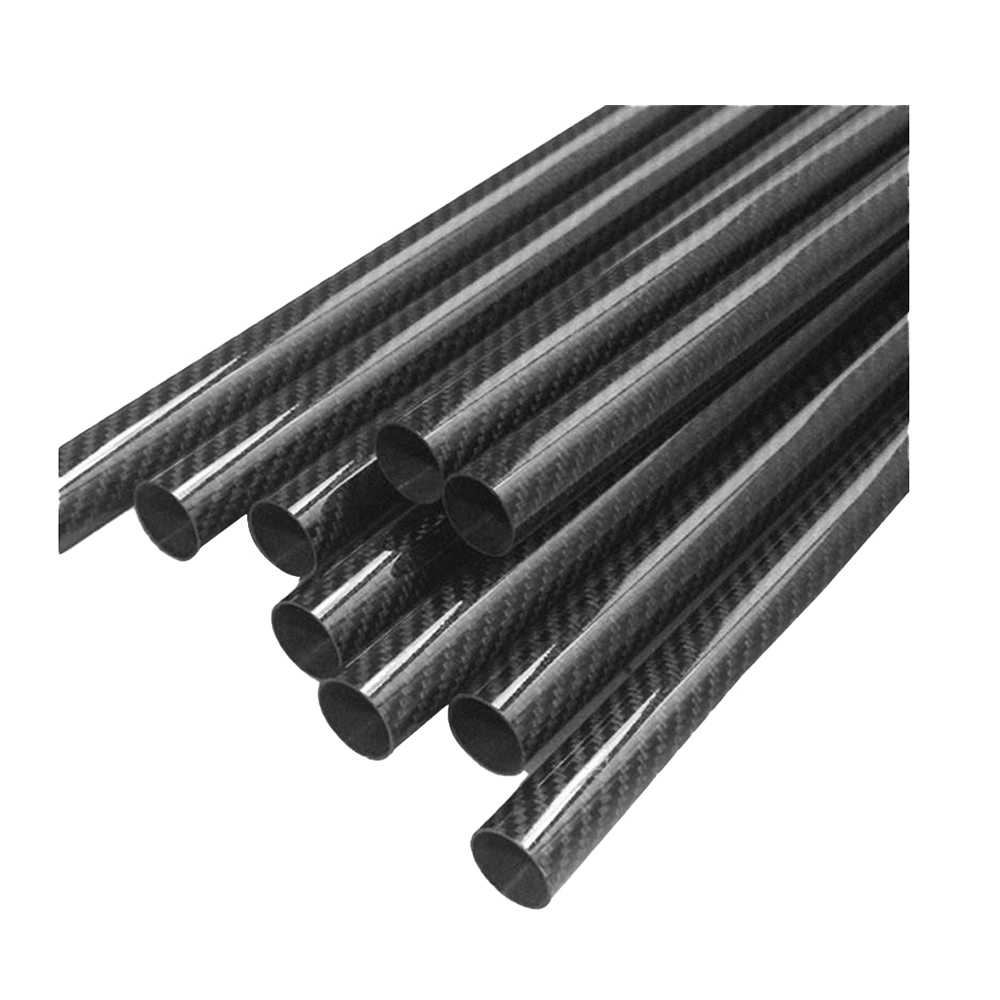
Carbon Fiber Sheet and Tube Custom

KTM 1290 Super Duke R Carbon Fiber Rear Fender

Honda CBR1000RR-R Carbon Fiber Belly Pan Lower Side Fairings
Leave a message
Have a question or inquiry about our carbon fiber composite products? Leave us a message here and our team will get back to you promptly.
Whether you're interested in custom orders, technical specifications, or partnership opportunities, we're here to assist you.
Please fill out the fields above with your name, email address, and message.
© 2024 Supreem Carbon All Rights Reserved.
Facebook
Pinterest
LinkedIn
Instagram