Why is carbon fiber stronger than steel? | Supreem Carbon Expert Guide
Why Carbon Fiber Outperforms Steel in Strength-to-Weight?
For industry professionals making critical material procurement decisions, understanding the fundamental differences between carbon fiber and steel is paramount. While steel has been the backbone of industrial infrastructure for centuries, carbon fiber composites have emerged as a revolutionary alternative, particularly due to their exceptional strength-to-weight ratio. It's not simply about raw strength, but how much strength you get for a given weight.
Steel, typically with a density around 7.8 g/cm³, offers impressive tensile strength. However, carbon fiber, with a density ranging from approximately 1.7 to 1.9 g/cm³, is up to five times lighter. When comparing specific strength (strength divided by density) or specific modulus (stiffness divided by density), carbon fiber composites often demonstrate values that are 5 to 10 times higher than those of high-strength steel alloys. This means you can achieve equivalent or superior performance with significantly less material weight, leading to substantial gains in efficiency, fuel economy, and payload capacity in applications from aerospace to automotive.
What Specific Mechanical Properties Differentiate Carbon Fiber from Steel?
To truly grasp carbon fiber's advantages, a look at the hard numbers is essential:
- Tensile Strength: While high-strength steel alloys can reach tensile strengths of 1-2 GPa (Gigapascals), advanced carbon fiber composites can exhibit tensile strengths ranging from 3 GPa for standard modulus fibers to over 7 GPa for ultra-high strength grades. This makes carbon fiber incredibly resistant to stretching or breaking under tension.
- Tensile Modulus (Stiffness): Steel typically has a Young's Modulus of around 200 GPa. Carbon fibers, depending on the grade, can have moduli ranging from 230 GPa (standard modulus) up to 800 GPa (ultra-high modulus), making them exceptionally stiff. This stiffness is crucial for maintaining structural integrity and precision in demanding applications.
- Density: As mentioned, steel's density is about 7.8 g/cm³, whereas carbon fiber composites are significantly lighter at 1.7-1.9 g/cm³. This fundamental difference underpins the superior specific properties of carbon fiber.
It's also vital to consider that carbon fiber composites are anisotropic, meaning their properties vary with direction due to fiber orientation. Steel, being a metal, is largely isotropic. This anisotropy in carbon fiber allows for highly optimized designs where strength and stiffness can be precisely aligned with expected load paths, further enhancing performance.
How Does Carbon Fiber's Durability and Fatigue Resistance Compare to Steel's for Industrial Applications?
For long-term industrial applications, durability and fatigue resistance are critical. Carbon fiber composites generally exhibit excellent fatigue resistance, meaning they can withstand repeated loading and unloading cycles without significant degradation, often outperforming steel in this regard under specific conditions. Unlike metals that can deform plastically, carbon fiber composites tend to fail suddenly once their strength is reached, which requires careful design and monitoring.
Furthermore, carbon fiber is inherently resistant to corrosion, a common issue with steel that necessitates protective coatings or more expensive stainless steel alloys. This makes carbon fiber an ideal choice for harsh environments where moisture, chemicals, or saltwater exposure are concerns, significantly extending part lifespan and reducing maintenance costs.
However, carbon fiber composites can be more susceptible to localized impact damage due to their brittle nature compared to steel's ductility. Proper design, including strategic reinforcement and material selection for the matrix, is essential to mitigate this.
When Should Industry Professionals Choose Carbon Fiber Over Steel?
The decision to opt for carbon fiber over steel often boils down to a cost-benefit analysis beyond the initial material price. Carbon fiber becomes the superior choice in applications where:
- Weight Reduction is Critical: Aerospace, high-performance automotive (Formula 1, electric vehicles), robotics, drones, and portable equipment where reduced mass translates to increased efficiency, speed, or maneuverability.
- High Stiffness and Precision are Required: Manufacturing tooling, robotic arms, satellite components, and sports equipment where minimal deflection under load is essential.
- Corrosion Resistance is Paramount: Marine applications, chemical processing equipment, and infrastructure in harsh environmental conditions.
- Fatigue Life is a Key Performance Indicator: Components subjected to repetitive stress, such as rotating parts or vibratory elements.
While the initial cost of carbon fiber is generally higher than steel, the operational savings (e.g., fuel efficiency, reduced maintenance, increased payload) and performance gains often lead to a lower total cost of ownership over the product's lifespan.
What Are the Key Design and Manufacturing Considerations for Carbon Fiber Parts?
For repeat procurement of carbon fiber parts, understanding design and manufacturing nuances is crucial:
- Anisotropic Properties: Designers must account for the directional strength and stiffness, optimizing fiber orientation to align with anticipated stress vectors. This requires specialized simulation tools (e.g., Finite Element Analysis).
- Tooling and Molds: Precision molds are required, often machined from metals or composites, to shape the carbon fiber fabric and resin. The tooling cost can be significant for initial setup but amortizes over repeat production runs.
- Curing Processes: Carbon fiber parts are typically manufactured using processes like autoclave curing, vacuum bagging, or resin transfer molding (RTM) to ensure proper resin impregnation and curing, which dictates part quality and performance.
- Joining Techniques: Unlike steel, welding carbon fiber is not an option. Parts are often joined using adhesive bonding, mechanical fasteners (with careful consideration to avoid stress concentrations), or co-curing techniques.
- Quality Control: Non-destructive testing (NDT) methods such as ultrasonic inspection and thermography are critical for ensuring internal integrity, detecting voids, or delaminations in finished parts.
Professional suppliers with expertise in composite design and manufacturing are indispensable for ensuring high-quality, repeatable carbon fiber component production.
Supreem Carbon: Your Partner for Advanced Carbon Fiber Solutions
When seeking a reliable partner for your carbon fiber component needs, Supreem Carbon stands out. We specialize in delivering high-performance carbon fiber parts, leveraging cutting-edge manufacturing techniques and stringent quality control. Our advantages include:
- Expert Engineering & Design: Our team possesses deep expertise in composite design, optimizing fiber orientation and layups for peak performance and durability tailored to your specific application.
- Precision Manufacturing: We utilize advanced processes like autoclave curing and RTM, ensuring exceptional part consistency, minimal voids, and superior mechanical properties for every component.
- Customization & Scalability: From prototypes to high-volume production, we offer bespoke solutions, adapting to your unique project requirements and ensuring seamless integration into your supply chain.
- Unwavering Quality: Every Supreem Carbon part undergoes rigorous quality checks, including NDT, to guarantee the highest standards of reliability and performance, reducing your operational risks and costs.
- Cost-Effective Long-Term Value: By focusing on optimized design and manufacturing efficiency, we provide carbon fiber solutions that deliver superior long-term value, offsetting initial investment with significant operational benefits.
Choose Supreem Carbon for your next project and experience the difference that true composite expertise can make.
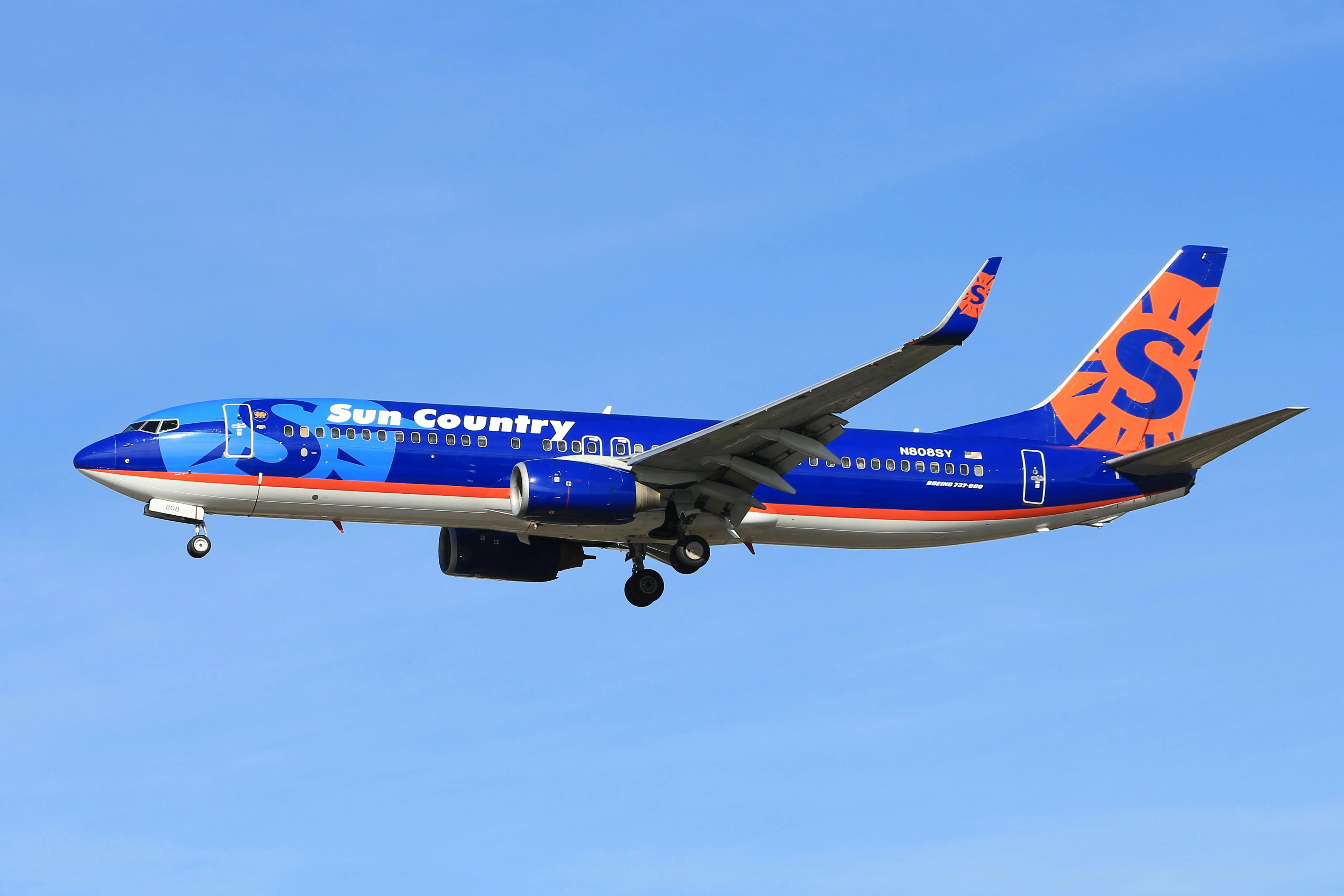
The Ultimate Guide to Carbon Fiber in Aerospace Applications
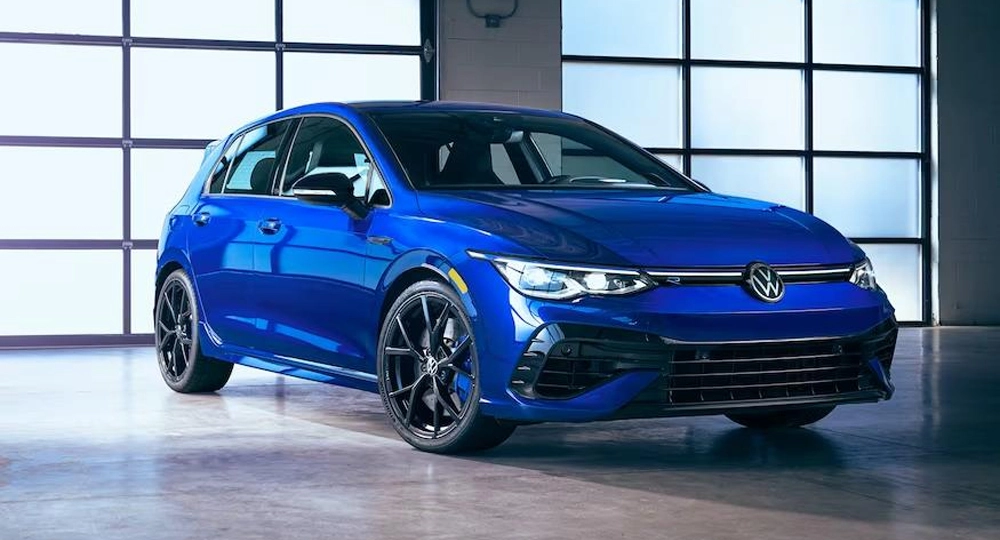
Supreem Carbon Auto parts new arrivals!

How to Choose High-Performance Carbon Fiber Materials: Supreem Carbon’s Expert Guide

How Long Does Carbon Fiber Last? Unveiling the Durability of a Tech Marvel

Ducati monster 937 and BM S1000RR 2016+ new arrivals released!

New arrivals---Carbon Fiber Slam Panel Replacement for BMW M3 M4
For Products
Which carbon fiber material you can provide in production?
1*1 plain /2*2 twill / forged carbon / honeycomb / kevlar and so on.
Which surface could you provide for the carbon parts?
Gloss finish, matte finish, satin finish. Some color coating as the customer needs.
Supreem Carbon parts produce by 100% carbon?
Yes,all products are made from full carbon with dry carbon.
For Order Delivery
What is the shipping time for the different ways?
Express delivery 5-7 days.
20-25 days by sea.
15 days by air.
For Carbon Fiber Material
What are the advantages of carbon fiber?
High Strength-to-Weight Ratio
It is stronger than many traditional materials, such as steel and aluminum.This high strength-to-weight ratio allows for the creation of lightweight components that maintain structural integrity and durability.
Lightweight
One of the most significant advantages of carbon fiber is its low density, contributing to lightweight structures. This property is particularly crucial in industries where weight reduction is a priority, such as aerospace, automotive, and sports equipment.
Resistant to corrosion and chemicals
Carbon fiber is inherently resistant to corrosion, making it an ideal material for applications exposed to harsh environments or corrosive substances. This property contributes to the longevity of components and reduces maintenance requirements. Carbon fiber has good chemical resistance, making it suitable for use in environments where exposure to chemicals or harsh solvents is a concern. This resistance enhances the material's durability in various industrial settings.
Tolerant of high temperature
Carbon fiber exhibits excellent thermal stability and resistance to high temperatures. This makes it suitable for applications where components are exposed to elevated temperatures, such as in the aerospace and automotive industries.
Low thermal expansion
Carbon fiber has a low coefficient of thermal expansion, meaning it expands or contracts minimally with changes in temperature. This property contributes to dimensional stability, making carbon fiber components reliable in varying temperature conditions.
Aesthetic Appeal
Carbon fiber has a modern and high-tech appearance, contributing to its aesthetic appeal. This property is leveraged in consumer goods, automotive components, and sporting equipment where visual appeal is important.

Ducati Monster 937 Carbon Fiber Engine Protect Cover

Honda NSX Carbon Fiber Center Dash Panel Replacement
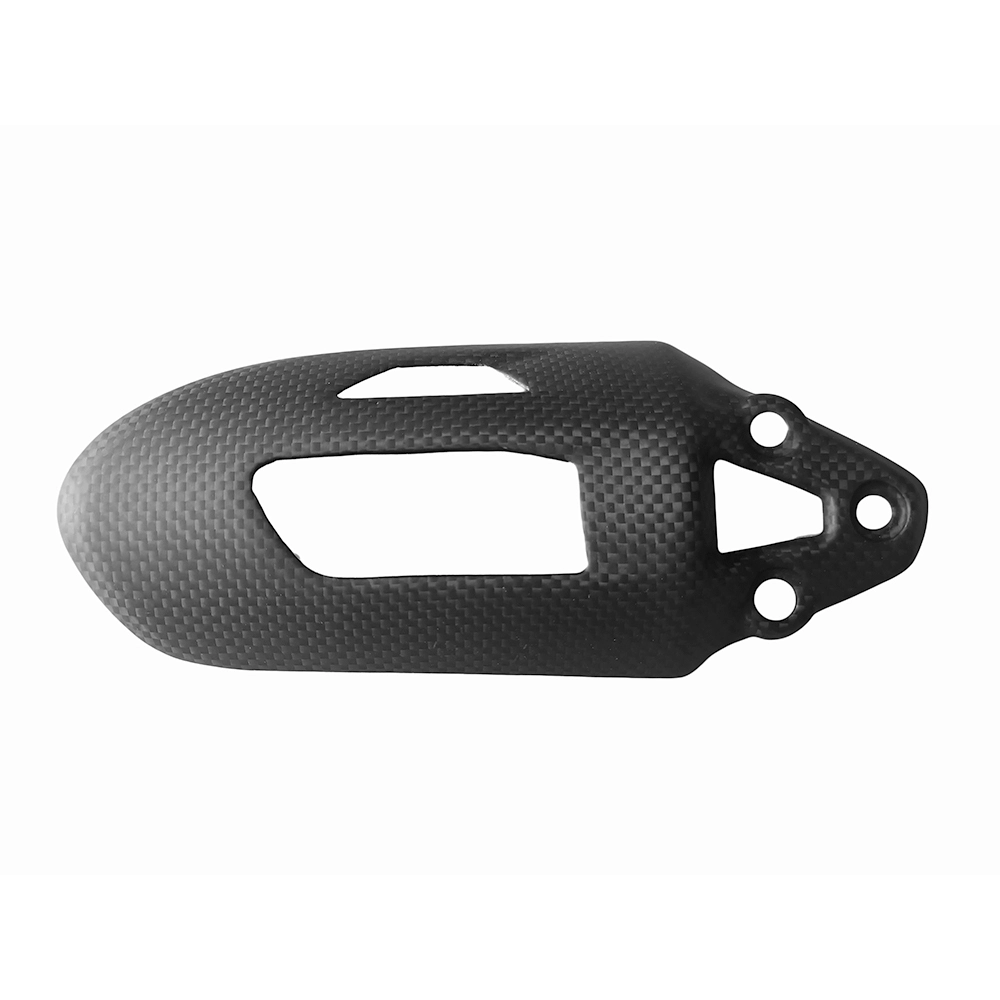
Ducati Panigale 1199 1299 899 959 V2 Carbon Fiber Suspension Cover
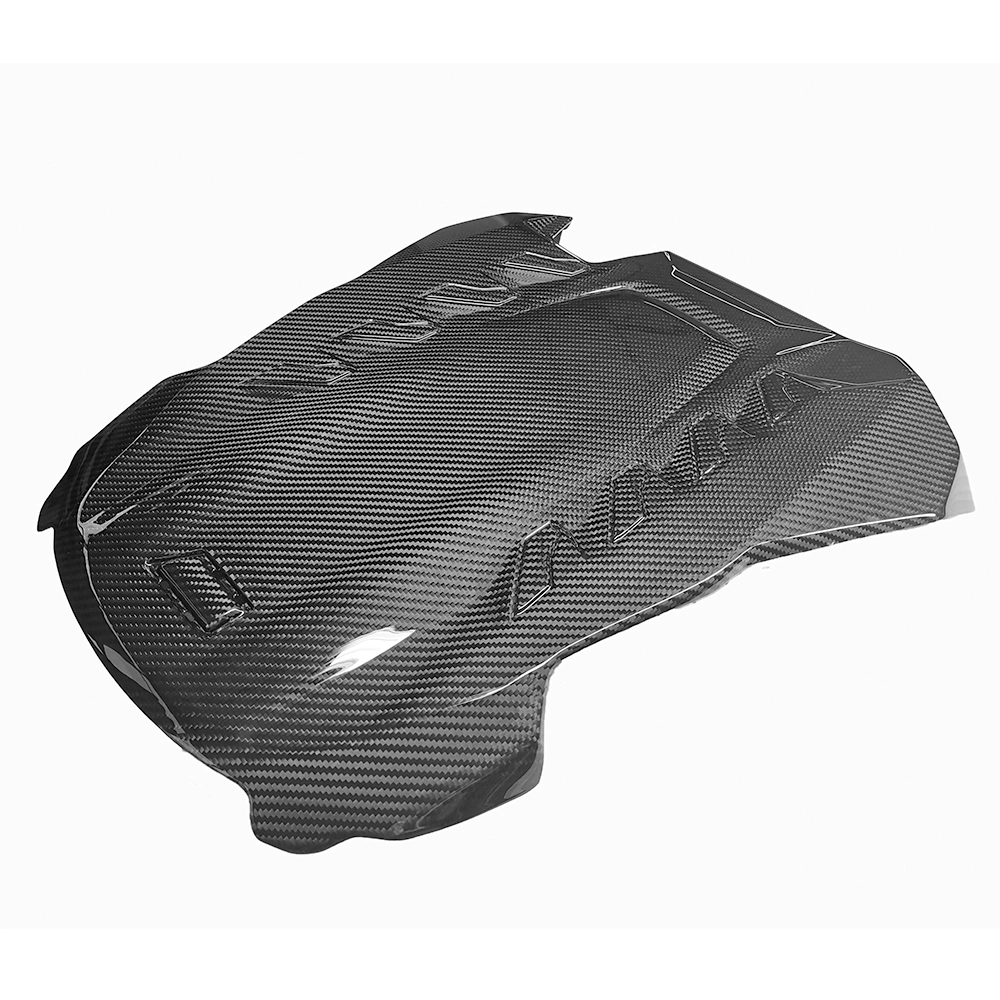
BMW F85/ F86 Carbon Fiber Interior Engine Cover Replacement
Leave a message
Have a question or inquiry about our carbon fiber composite products? Leave us a message here and our team will get back to you promptly.
Whether you're interested in custom orders, technical specifications, or partnership opportunities, we're here to assist you.
Please fill out the fields above with your name, email address, and message.
© 2024 Supreem Carbon All Rights Reserved.
Facebook
Pinterest
LinkedIn
Instagram