What are the disadvantages of carbon fiber in cars? | Supreem Carbon Expert Guide
<!DOCTYPE >< lang=en>
Carbon fiber has undeniably transformed the automotive landscape, pushing boundaries in performance and efficiency through radical weight reduction. From hypercars to performance trims, its lightweight strength offers unparalleled stiffness-to-weight ratios. However, for industry professionals involved in the procurement and long-term planning of automotive components, understanding the inherent disadvantages of carbon fiber is as crucial as recognizing its benefits. This article delves into the top five considerations for those making informed purchasing decisions in the carbon fiber parts industry.
What Are the Disadvantages of Carbon Fiber in Cars?
1. Why is Carbon Fiber So Expensive for Automotive Applications?
The most significant barrier to widespread carbon fiber adoption in the automotive sector remains its exorbitant cost. This high price point stems from several factors:
- Raw Material Cost: The primary precursor for carbon fiber, polyacrylonitrile (PAN), is itself an expensive material. The process of converting PAN into carbon fiber involves multiple energy-intensive steps, including oxidation, carbonization, and surface treatment, which are costly. While the cost has seen some reduction over the years, high-grade aerospace or automotive carbon fiber can still be upwards of $100 per kilogram, significantly more than steel (around $1-2/kg) or aluminum (around $3-5/kg).
- Manufacturing Complexity: Production of carbon fiber parts is intricate and time-consuming. Processes like hand lay-up, resin transfer molding (RTM), or autoclave curing require specialized equipment, high temperatures, and immense pressures. These processes are slow, limit production volume, and demand highly skilled labor, all contributing to elevated unit costs.
- Scrap Rates: Due to the precision required and the unforgiving nature of the material, scrap rates can be higher than with traditional metals, leading to wasted material and increased overall costs.
2. Is Carbon Fiber Easily Damaged, and How Difficult/Costly is it to Repair?
While exceptionally strong and stiff, carbon fiber composites are known for their brittleness and unique failure modes, which complicate repair:
- Brittle Failure: Unlike ductile metals that deform or crumple upon impact, carbon fiber tends to shatter, crack, or delaminate (layers separating) under localized stress. This means even minor impacts can cause significant damage that isn't always visible on the surface.
- Complex Repair Procedures: Repairing carbon fiber is a highly specialized skill. It often involves grinding away damaged layers, laying new carbon fiber plies, and re-curing the area, sometimes requiring specific resins and curing conditions. This process is time-consuming, labor-intensive, and requires specialized tools and facilities.
- High Repair Costs: Due to the complexity and specialized nature, carbon fiber repairs can be prohibitively expensive. Anecdotal evidence and insurance claims often show that repairing a carbon fiber panel can cost 5 to 10 times more than repairing a comparable steel or aluminum part, sometimes necessitating full panel replacement rather than localized repair. For example, a minor bumper crack on a carbon fiber component could easily run into several thousands of dollars for repair or replacement.
3. What are the Manufacturing Challenges for Carbon Fiber Car Parts?
Beyond material cost, the fabrication of carbon fiber automotive components presents significant manufacturing hurdles:
- Tooling Investment: Molds for carbon fiber parts are expensive, often made from precision-machined steel or invar, capable of withstanding high temperatures and pressures. This upfront tooling cost is a major barrier for new product lines.
- Slow Cycle Times: Traditional high-performance carbon fiber production methods, particularly autoclave curing, involve long cycle times (hours per part for curing alone). This drastically limits the production volume compared to rapid metal stamping or casting. While out-of-autoclave (OOA) processes and faster-curing resins are emerging, they often come with their own trade-offs in terms of material properties or tooling complexity.
- Quality Control: Ensuring uniform fiber impregnation, void-free laminates, and precise part dimensions is critical. Defects like voids, delaminations, or fiber misalignment can severely compromise the part's structural integrity, requiring rigorous and often costly non-destructive testing (NDT).
4. How Does Carbon Fiber Perform in Crashes Compared to Metal?
Carbon fiber's crash performance is a nuanced topic. While excellent for structural rigidity and lightweighting, its energy absorption characteristics differ from metals:
- Different Energy Absorption: Metals absorb crash energy by deforming plastically (crumpling), which dissipates kinetic energy over a controlled distance. Carbon fiber, being brittle, absorbs energy by fracturing and shattering. While it can absorb significant energy through this fragmentation, designing predictable crumple zones is more challenging.
- Impact on Occupant Safety: Modern vehicle safety relies on carefully engineered crumple zones. Integrating carbon fiber into these zones requires sophisticated design and simulation to ensure predictable energy absorption and protect occupants, which adds to engineering complexity and cost. Advances in braided carbon fiber structures and hybrid metal-composite designs are being explored to combine the best properties of both materials for crashworthiness.
5. Are There Environmental Concerns with Carbon Fiber Production and Disposal?
The environmental footprint of carbon fiber is a growing concern for sustainability-minded companies:
- High Energy Consumption: The production of carbon fiber, particularly the carbonization process, is highly energy-intensive. For instance, the energy required to produce carbon fiber can be significantly higher per unit mass compared to steel or aluminum.
- Recycling Challenges: Most carbon fiber composites use thermoset resins, which cannot be melted down and reformed like thermoplastics or metals. This makes traditional recycling difficult. Current recycling methods like pyrolysis (burning off the resin) or solvolysis (chemical dissolution of resin) are still nascent, expensive, and often degrade the fiber quality, limiting their widespread adoption. Consequently, a significant amount of carbon fiber waste ends up in landfills.
- Non-Biodegradable: Carbon fiber itself is not biodegradable, meaning discarded parts persist in the environment indefinitely.
Supreem Carbon: Navigating the Challenges, Delivering Superior Solutions
While the disadvantages of carbon fiber are clear, leading manufacturers like Supreem Carbon are actively working to mitigate these challenges, offering compelling value for professional buyers:
- Optimized Cost-Effectiveness: Supreem Carbon leverages advanced manufacturing techniques, including automated fiber placement and efficient resin systems, to reduce production costs and offer competitive pricing for bulk and recurring orders, making high-performance parts more accessible without compromising quality.
- Enhanced Durability & Repairability: Through rigorous R&D, Supreem Carbon engineers products with improved resin matrices and weave patterns that enhance impact resistance and, where possible, facilitate more localized repairs, reducing downtime and costs for end-users. Our components are designed with an understanding of real-world application stresses.
- Streamlined Manufacturing & Quality: Utilizing state-of-the-art facilities and stringent quality control protocols, Supreem Carbon ensures consistent, high-quality output with minimized defects and optimized cycle times. This means reliable supply and superior part performance for your production lines.
- Innovative Crashworthiness Design: Our engineering team employs advanced simulation and design methodologies to develop carbon fiber components that integrate seamlessly with modern vehicle architectures, contributing to overall safety and performance, not just weight savings.
- Commitment to Sustainability: Supreem Carbon is actively investing in research for more sustainable manufacturing processes and exploring end-of-life solutions, demonstrating a commitment to reducing the environmental footprint of carbon fiber composites.
Choosing Supreem Carbon means partnering with a leader dedicated to pushing the boundaries of carbon fiber technology, providing you with not just parts, but integrated solutions that address the inherent challenges of this advanced material, ensuring long-term value and performance for your automotive applications.
</>
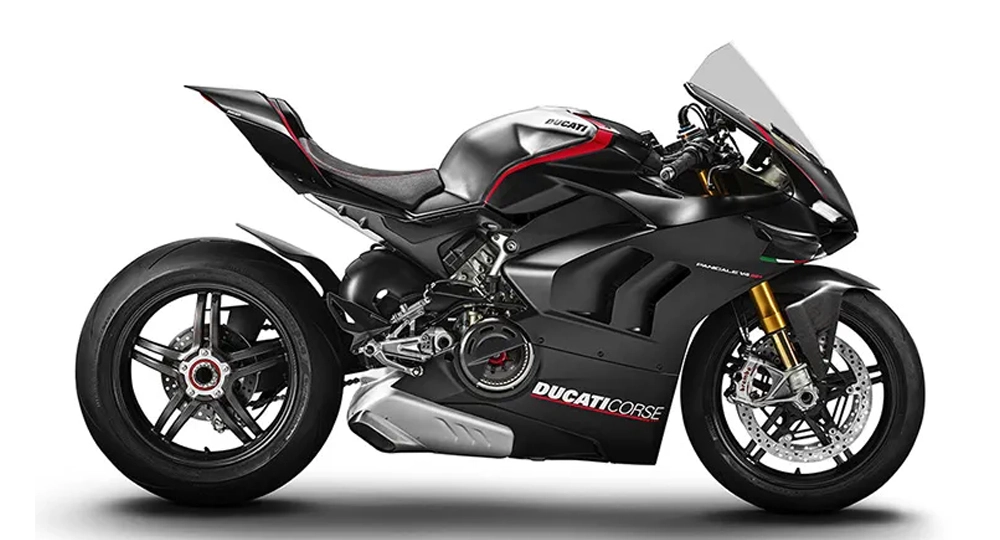
Great News!!! Ducati V4 SP new arrivals released.
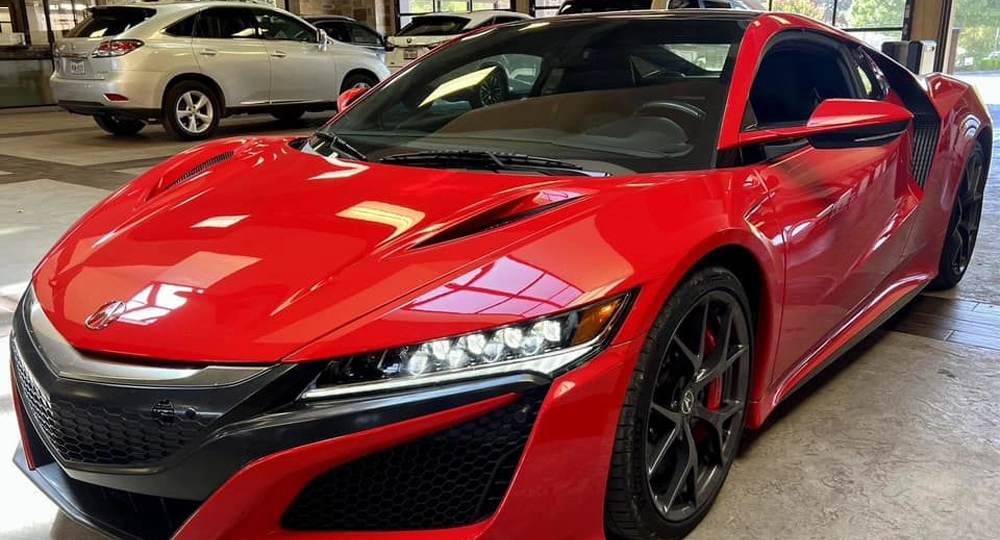
Supreem carbon Honda-NSX 100% Fiber Door Handle released!
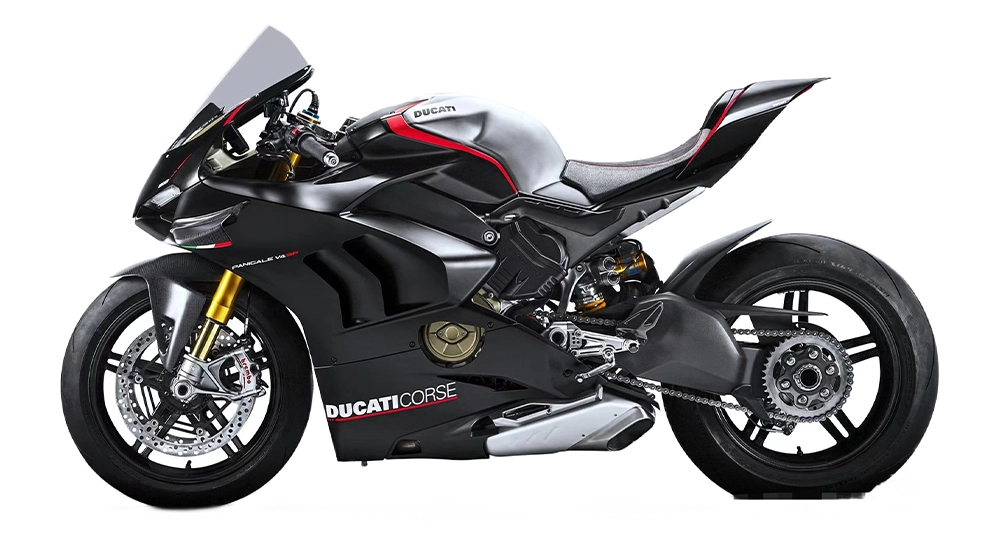
Supreem Carbon New arrivals alert!

New Arrivals of BMW S1000RR 2020+ full carbon fiber sets.
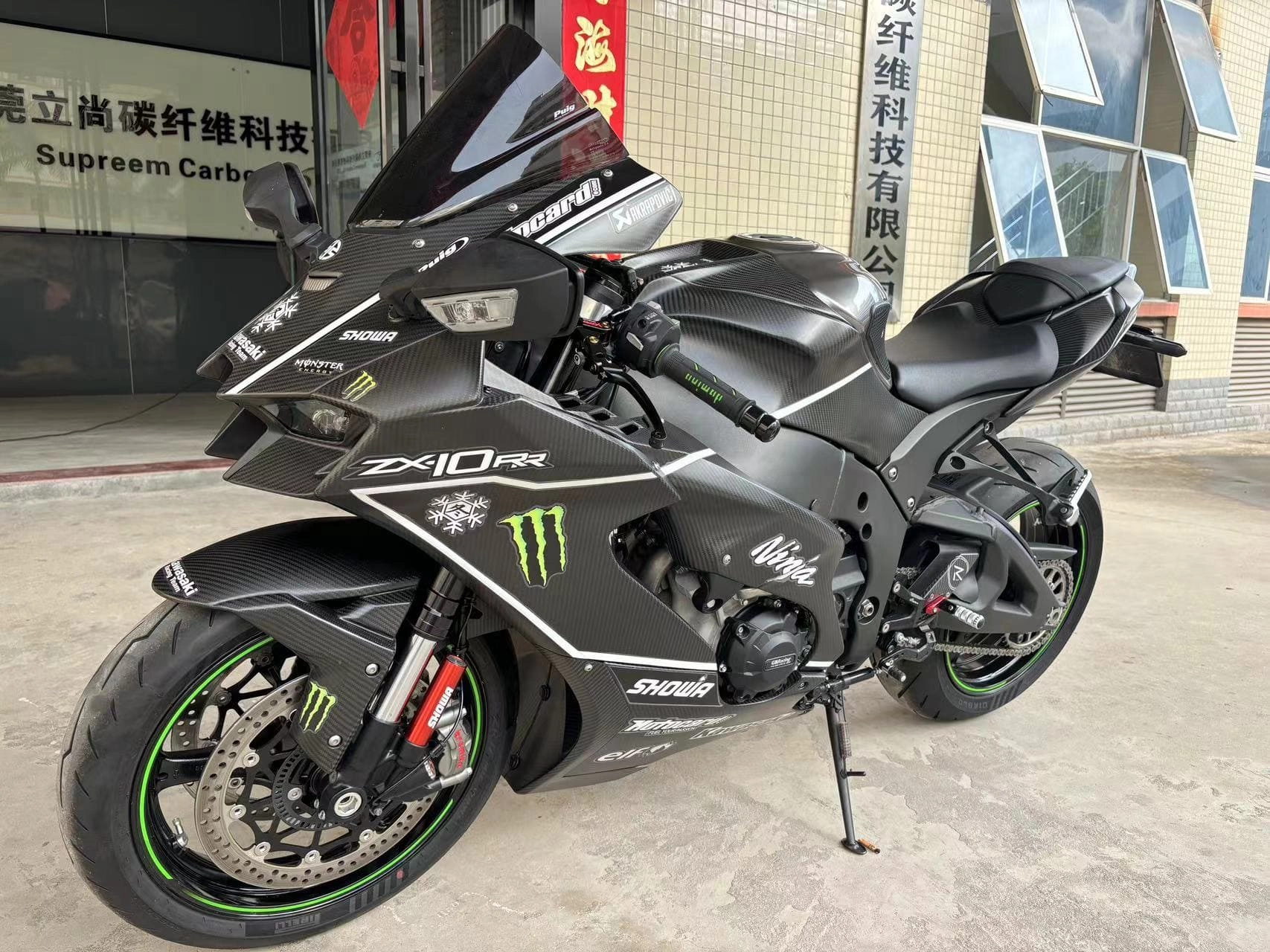
Kawasaki ZX10R Carbon Fiber New Pattern Look.
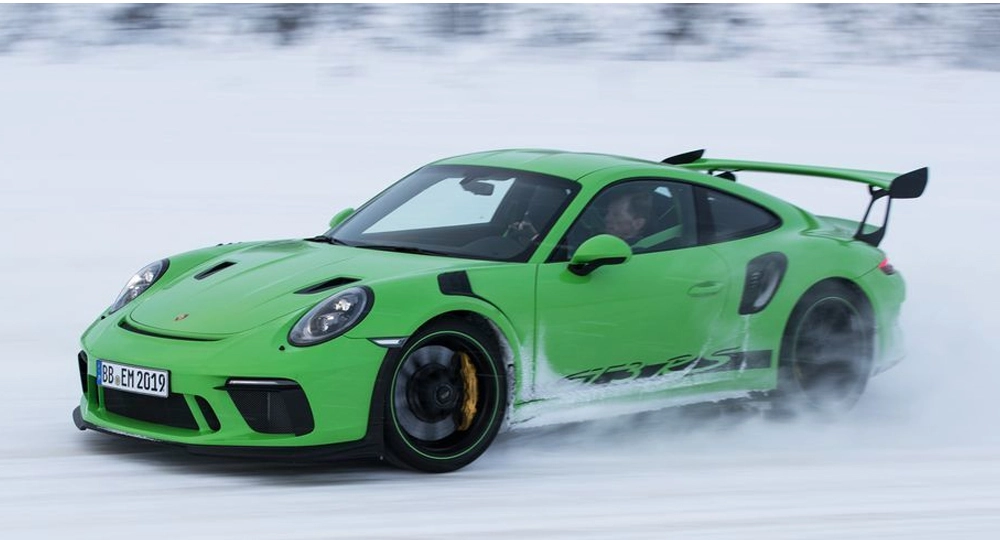
Supreem carbon Auto part new arrivals!
For Facotry
Can I visit your company?
Of course, we are in QiaoTou Town, Dongguan City, Guangdong Province, China.
For Products
How can I get some sample?
Actually we dont provide the free sample to customer, you can place a sample order if need some parts.
For After-sales Service
Do you offer a warranty?
Six month standard warranty on all products. Damage due to installation error or natural elements will not be covered.
For Customized Service
What can be customized in addition to customized carbon fiber parts?
You can customize your company logo, packaging, even the color of coating and so on.
How long does the customized products order take?
This depends on the complexity and mold production cycle of the product. The first sample will be ready in 2-3 weeks after mold finished.

Kawasaki H2 Carbon Fiber Front Fairing

Yamaha MT-07 Carbon Fiber Tank Cover

Ducati Monster 937 Carbon Fiber Sprocket Cover

KTM 1290 Super Duke R Carbon Fiber Rear Fender
Leave a message
Have a question or inquiry about our carbon fiber composite products? Leave us a message here and our team will get back to you promptly.
Whether you're interested in custom orders, technical specifications, or partnership opportunities, we're here to assist you.
Please fill out the fields above with your name, email address, and message.
© 2024 Supreem Carbon All Rights Reserved.
Facebook
Pinterest
LinkedIn
Instagram