is carbon fiber bulletproof | Supreem Carbon Expert Guide
Is Carbon Fiber Bulletproof? Unpacking Ballistic Performance for Industry Professionals
The question, Is carbon fiber bulletproof? often arises, especially in industries seeking advanced material solutions for protection and performance. While carbon fiber is renowned for its exceptional strength-to-weight ratio and stiffness, it's crucial to understand its role in ballistic protection is more complex than simply being 'bulletproof' on its own. Carbon fiber is a high-performance structural material, but for direct ballistic impact resistance, it is typically used as a component within a multi-layered composite system, rather than the primary stopping agent.
Unlike monolithic materials designed to deform or break upon impact (like steel or ceramics), carbon fiber's strength lies in its ability to distribute and absorb energy across its woven structure when combined with appropriate resins and other materials. Its brittleness, however, means a standalone carbon fiber panel might shatter or splinter under a direct ballistic strike without proper reinforcement or hybridization. Therefore, in professional procurement, it's essential to look beyond the simple 'bulletproof' notion and understand carbon fiber's specific contributions to a comprehensive ballistic solution.
How Does Carbon Fiber Compare to Other Ballistic Materials Like Kevlar?
When considering ballistic applications, carbon fiber is often compared to aramid fibers like Kevlar (DuPont's para-aramid synthetic fiber) and ultra-high-molecular-weight polyethylene (UHMWPE) fibers like Dyneema or Spectra. Each material offers distinct advantages:
- Carbon Fiber: Excel in tensile strength, stiffness, and lightweighting for structural applications. It provides excellent rigidity and dimensional stability, making it ideal for structural components that support or encapsulate ballistic layers. Its high strength-to-weight ratio is crucial for reducing overall system weight. However, on its own, carbon fiber lacks the energy absorption and ductility of aramid or UHMWPE fibers for direct ballistic impact.
- Kevlar (Aramid Fibers): These are the workhorses of soft body armor. Kevlar's strength lies in its high energy absorption and impact resistance. Its fibers are designed to stretch and dissipate the projectile's energy across a wider area, preventing penetration. Kevlar is less stiff than carbon fiber and is primarily used for its ballistic properties rather than structural integrity.
- UHMWPE (e.g., Dyneema, Spectra): Known for having one of the highest strength-to-weight ratios of any material, UHMWPE offers superior ballistic performance against high-velocity threats, particularly in terms of blunt trauma reduction. It is often used in hard and soft armor plates. It's lighter than Kevlar but can be more susceptible to high temperatures.
In many advanced ballistic systems, these materials are used synergistically. Carbon fiber might form the structural shell or backing plate due to its stiffness and light weight, while layers of Kevlar or UHMWPE provide the primary ballistic stopping power. This hybrid approach leverages the best properties of each material to create robust, lightweight, and effective protective solutions.
What are the Actual Ballistic Applications of Carbon Fiber?
While not a standalone 'bulletproof' material, carbon fiber plays a vital role in various ballistic and high-performance protective applications:
- Structural Reinforcement in Armored Vehicles: Carbon fiber composites are used to create lightweight yet rigid structural elements in armored vehicles, allowing for greater payload capacity or fuel efficiency. Ballistic ceramics or specialized composite panels (often containing aramid or UHMWPE) are then integrated onto or within these carbon fiber structures.
- Helmet Shells: Modern ballistic helmets frequently incorporate carbon fiber in their shells. Here, carbon fiber contributes to the helmet's structural integrity, rigidity, and lightweight nature, while an inner layer of aramid or UHMWPE provides the primary ballistic protection. The carbon fiber helps distribute impact forces and maintain the helmet's shape.
- Backing Plates for Ceramic Armor: In hard armor plates (e.g., for body armor or vehicle panels), carbon fiber can be used as a backing material behind ceramic strike faces. The ceramic shatters the projectile, and the carbon fiber composite backing then catches the fragments and absorbs residual energy, preventing spalling and penetration.
- Unmanned Aerial Vehicles (UAVs) and Drones: For surveillance or military drones that might face small arms fire, carbon fiber's lightweight and strong properties are invaluable for the airframe, reducing weight while providing some level of inherent resistance against minor impacts or fragmentation.
- Sporting Goods and Protective Gear: While not strictly 'ballistic,' carbon fiber is widely used in protective gear for sports (e.g., motorcycle helmets, cycling gear) where high impact resistance and weight savings are crucial.
In essence, carbon fiber's contribution is often in enhancing the structural integrity, reducing weight, and enabling the integration of other, more specialized ballistic materials, leading to highly optimized protective systems.
What Factors Influence the Ballistic Performance of Carbon Fiber Composites?
For industry buyers, understanding the variables that influence a carbon fiber composite's performance is crucial for informed procurement:
- Fiber Type and Architecture: High-strength (HT) carbon fibers are generally preferred over high-modulus (HM) fibers for impact resistance due to their higher strain-to-failure. The weave pattern (e.g., plain, twill, satin, or unidirectional tapes) significantly affects how energy is absorbed and distributed. Unidirectional (UD) layers, when strategically oriented, can be very effective in ballistic applications due to their ability to transfer energy along the fiber direction.
- Resin System: The matrix resin plays a critical role in binding the fibers and transferring stress. Toughened epoxy resins are often chosen for ballistic applications due to their improved fracture toughness and ability to absorb impact energy without delaminating prematurely. Thermoplastic resins are also gaining traction for their potential in high-performance composites due to their ductility.
- Layer Count and Orientation: Ballistic performance is greatly enhanced by using multiple layers of fabric/prepreg, with fibers oriented in different directions (e.g., 0/90, +/-45 degrees) to create a quasi-isotropic laminate. This cross-plying helps distribute impact energy across multiple layers and prevents localized failure.
- Hybridization with Other Materials: Combining carbon fiber with aramid fibers (Kevlar, Twaron), UHMWPE (Dyneema, Spectra), fiberglass, or ceramic strike plates significantly boosts ballistic performance. The synergy of these materials allows for tailored solutions for specific threat levels.
- Manufacturing Process: Techniques like vacuum infusion, resin transfer molding (RTM), prepreg lay-up and autoclave curing, and filament winding directly impact the composite's quality, void content, and fiber-volume fraction—all critical for consistent performance. Proper curing cycles and consolidation are vital.
- Thickness and Density: As with any protective material, increasing thickness and density generally improves ballistic resistance, but this must be balanced against weight targets and design constraints.
A reputable supplier will be able to guide you through these complex interactions to specify the optimal composite for your application.
What Should Buyers Consider When Procuring Carbon Fiber for High-Performance Applications?
Procuring carbon fiber composites for demanding applications requires a strategic approach. Here are key considerations for industry buyers:
- Define Application-Specific Requirements: Clearly articulate the desired performance criteria, including target ballistic threat levels (e.g., NIJ standards, STANAG 4569 for vehicles), weight constraints, stiffness requirements, environmental operating conditions, and expected lifespan.
- Material Specifications: Work closely with suppliers to specify the exact type of carbon fiber (e.g., 3K, 12K, HTA, T700), weave style, resin system (e.g., epoxy, vinylester, phenolic, thermoplastic), and prepreg or dry fabric format. Ensure compatibility with your manufacturing processes.
- Supplier Expertise and Experience: Choose suppliers with proven experience in your specific application area, especially if it involves high-performance or protective composites. Their R&D capabilities, engineering support, and track record are paramount.
- Testing and Certification: Verify that the supplier can provide materials that meet relevant industry standards and certifications (e.g., ISO, aerospace standards, military specifications). Request material test reports (MTRs) and ensure their quality control processes are robust.
- Quality Control and Consistency: For high-stakes applications, material consistency is non-negotiable. Inquire about the supplier's quality management system, batch traceability, and process controls to ensure repeatable performance from one order to the next.
- Cost vs. Performance Trade-offs: High-performance materials often come with a High Quality. Evaluate the long-term value, including weight savings, improved durability, and enhanced safety, against the initial investment. A reliable supplier can help optimize this balance.
- Supply Chain Reliability: Ensure the supplier has a stable and robust supply chain to meet your production demands consistently and on time.
Partnering with a knowledgeable supplier who understands the nuances of carbon fiber and its composites is critical for successful project outcomes.
Conclusion: The Supreem Carbon Advantage
At Supreem Carbon, we specialize in delivering advanced carbon fiber composite solutions tailored for high-performance and demanding industrial applications. While carbon fiber alone isn't 'bulletproof,' our expertise lies in engineering sophisticated composite structures that integrate seamlessly with ballistic systems, contributing to significant weight reduction and enhanced structural integrity. We leverage cutting-edge manufacturing processes, select optimal fiber and resin systems, and apply rigorous quality control to ensure our products meet the most stringent specifications. Whether your project requires lightweight structural components, rigid backing plates for ballistic armor, or custom composite solutions for aerospace and defense, Supreem Carbon offers the technical prowess and reliable partnership to transform your concepts into high-performing realities, ensuring superior material properties and consistent quality for your procurement needs.

Asia's Top Carbon Fiber Motorcycle Accessory Brand
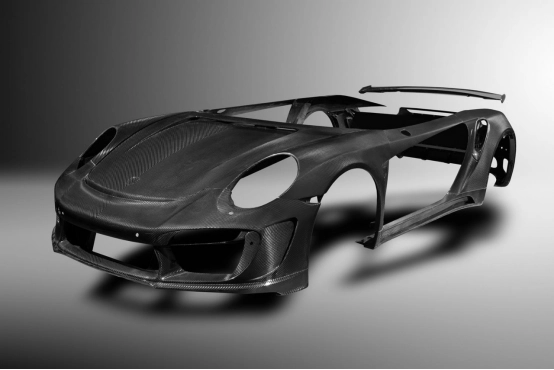
Application Advantages of Carbon Fiber in Automobile Chassis Brackets
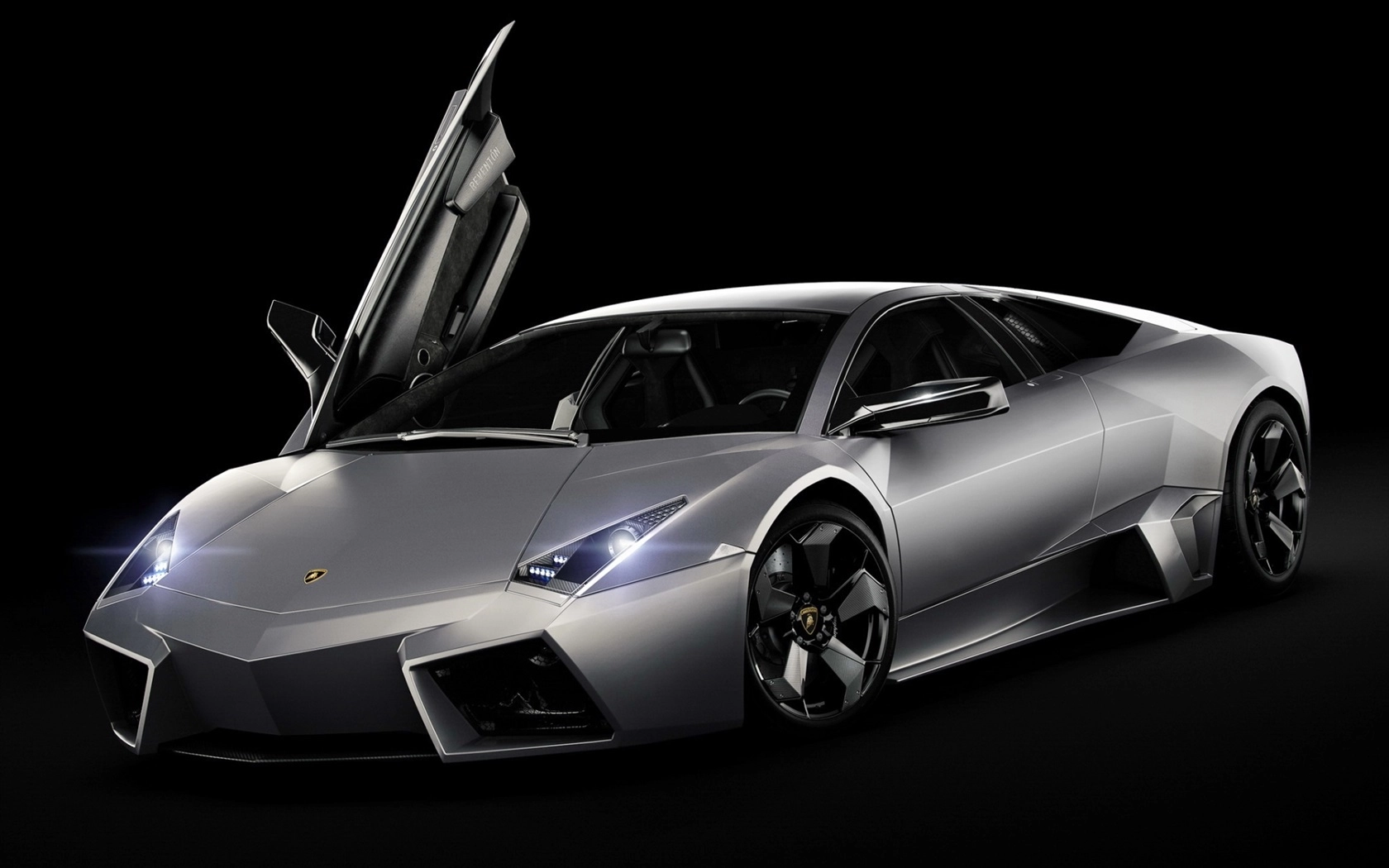
Understanding the Difference Between Dry Carbon and Wet Carbon Products
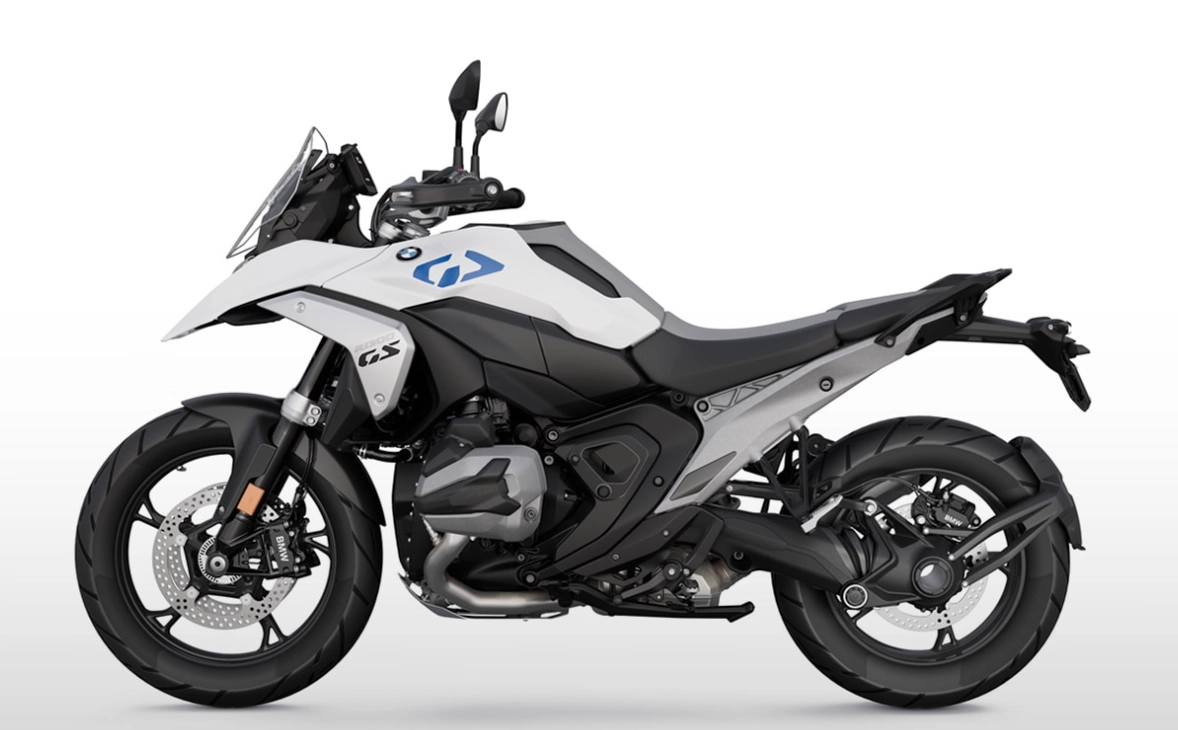
Supreem Carbon New Motorcycle Carbon Parts Development Plan.
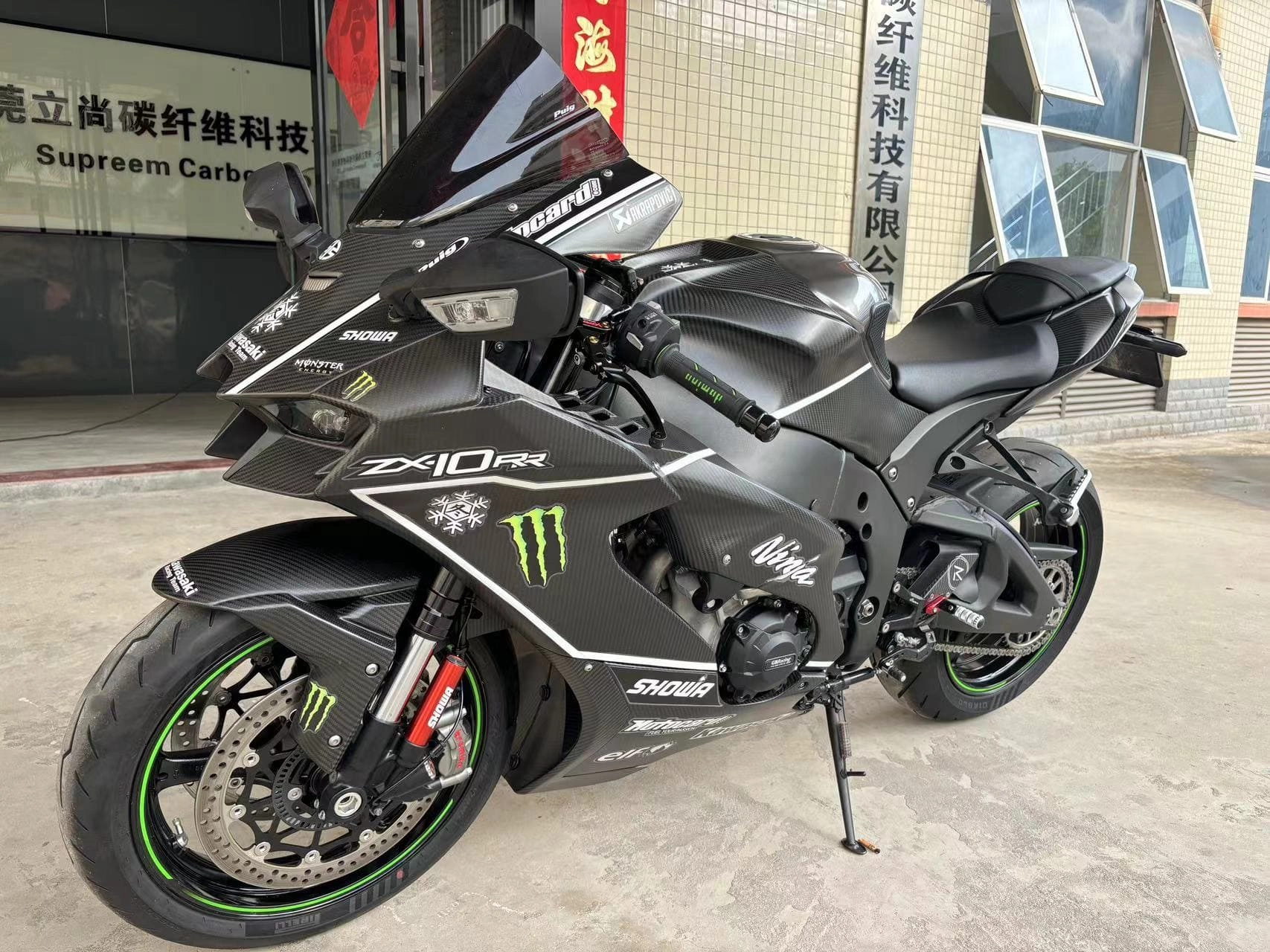
Kawasaki ZX10R Carbon Fiber New Pattern Look.

How to Choose High-Performance Carbon Fiber Materials: Supreem Carbon’s Expert Guide
For Products
Which surface could you provide for the carbon parts?
Gloss finish, matte finish, satin finish. Some color coating as the customer needs.
Are you parts have UV protected?
Absolutely! We use multiple layers of premium quality automotive clear (or matt) coats on our products, which ensure that they will remain super pretty for years to come.
For Customized Service
What can be customized in addition to customized carbon fiber parts?
You can customize your company logo, packaging, even the color of coating and so on.
What custom customer need to prepare?
1. Send Your Design/Idea/3D drawing.
2. Supplier Quotation Confirmation.
3. Firts Sample Feedback.
For Facotry
How many employees of Supreem carbon?
We have over 50 employees, including over 40 skilled workers, 3 R&D designers, and 5 QC professionals and so on.
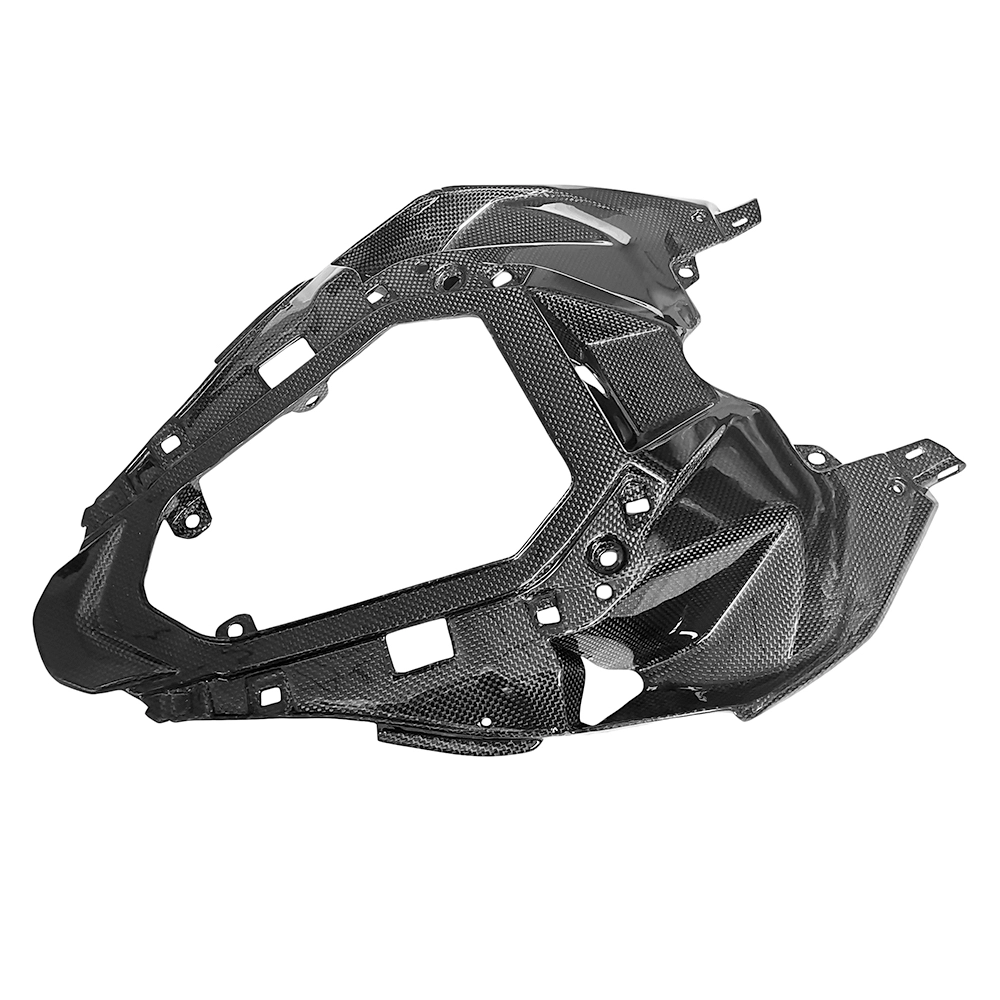
BMW S1000R Carbon Fiber Rear Seat Upper Fairing

Honda CBR1000RR-R Carbon Fiber Side Fairing
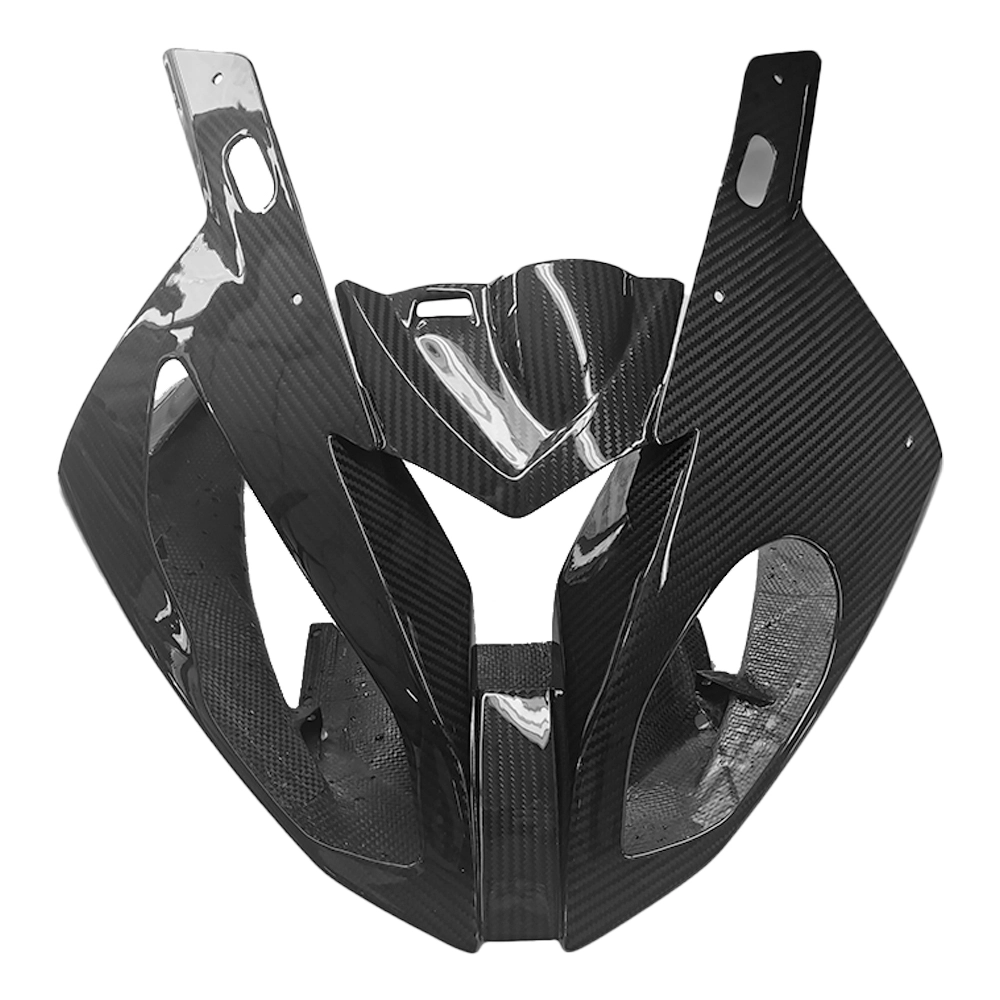
BMW S1000RR Carbon Fiber Front Fairing Cowls Custom

BMW S1000RR S1000R Carbon Fiber Front Fender
Leave a message
Have a question or inquiry about our carbon fiber composite products? Leave us a message here and our team will get back to you promptly.
Whether you're interested in custom orders, technical specifications, or partnership opportunities, we're here to assist you.
Please fill out the fields above with your name, email address, and message.
© 2024 Supreem Carbon All Rights Reserved.
Facebook
Pinterest
LinkedIn
Instagram