what is carbon fiber made of | Supreem Carbon Expert Guide
When considering carbon fiber parts for industrial applications, understanding the foundational aspects—from raw materials to manufacturing—is crucial for making informed procurement decisions. It's not just about the final product; it's about the material's origin, the process it undergoes, and how these factors influence performance and cost. Let's delve into the core questions surrounding carbon fiber's composition and production.
1. What are the primary raw materials of carbon fiber?
The vast majority of commercially produced carbon fiber, especially for high-performance applications, originates from Polyacrylonitrile (PAN). PAN is a synthetic polymer that, in its raw form, resembles a white, fluffy powder. It's chosen as the preferred precursor due to its high carbon yield and ability to form a stable, ordered structure during processing.
While PAN is dominant, other precursors exist:
- Pitch-based carbon fiber: Derived from petroleum pitch, these fibers typically offer higher modulus (stiffness) but lower tensile strength than PAN-based fibers. They are often used in applications requiring high stiffness and thermal conductivity, like brake pads and structural components.
- Rayon-based carbon fiber: Less common today for structural applications, rayon was historically one of the earliest precursors. Its use is limited due to lower carbon yield and properties compared to PAN or pitch.
2. How is carbon fiber manufactured from these raw materials?
The transformation of PAN into carbon fiber is a multi-stage, energy-intensive thermochemical process:
- Stabilization (Oxidation): PAN fibers are slowly heated in an oxygen atmosphere (air) at temperatures typically between 200-300°C for several hours. This process converts the linear PAN molecular chains into a more thermally stable, ladder-like structure by adding oxygen. This prevents melting during subsequent high-temperature carbonization.
- Carbonization: The stabilized fibers are then heated in an inert (oxygen-free) atmosphere, such as nitrogen or argon, at temperatures ranging from 1000-3000°C. During this stage, non-carbon atoms (hydrogen, nitrogen, oxygen) are driven off, leaving behind a carbon content of over 90%, often exceeding 95%. The temperature dictates the final properties; higher temperatures lead to higher modulus (stiffness).
- Graphitization (Optional): For ultra-high modulus (UHM) fibers, carbonized fibers may undergo a further heat treatment at temperatures exceeding 2000°C (up to 3000°C). This step promotes the growth and alignment of graphite crystallites, further increasing stiffness.
- Surface Treatment: The surface of the carbon fiber is chemically or electrochemically etched to improve adhesion with the polymer matrix (resin). This creates a rougher surface and introduces active chemical groups, enhancing the mechanical bond.
- Sizing: A protective coating, known as sizing or finish, is applied to the fibers. This coating protects the fibers from damage during handling and processing, and importantly, ensures compatibility and good bonding with the specific resin system (e.g., epoxy, polyester) used in the composite part.
Each step is meticulously controlled to achieve the desired mechanical properties and ensure consistent quality, which is paramount for industrial applications.
3. What makes carbon fiber so strong and lightweight?
Carbon fiber's exceptional strength-to-weight ratio stems from its unique atomic structure and manufacturing process:
- Atomic Structure: Carbon atoms are arranged in a hexagonal lattice, similar to graphite sheets. These sheets are highly oriented along the fiber's axis, and the strong covalent bonds between carbon atoms within these sheets provide immense strength.
- Small Crystal Size & Orientation: The manufacturing process results in very small, imperfect graphite crystallites that are highly aligned parallel to the fiber's length. This alignment allows the fiber to efficiently carry loads along its axis.
- High Aspect Ratio: Carbon fiber comes in long, thin filaments (typically 5-7 micrometers in diameter). When these filaments are embedded in a resin matrix to form a composite, the load is transferred efficiently from the matrix to the high-strength fibers.
- Low Density: Despite its strength, carbon fiber has a very low density, typically ranging from 1.7 to 1.9 g/cm³, which is significantly lighter than steel (~7.85 g/cm³) or aluminum (~2.7 g/cm³), while offering superior specific strength and stiffness.
This combination of factors allows carbon fiber composites to achieve remarkable performance, enabling lightweighting without compromising structural integrity, critical in sectors like aerospace and high-performance automotive.
4. What are the different types of carbon fiber and their common applications?
Carbon fibers are classified based on their mechanical properties, primarily tensile modulus (stiffness) and tensile strength. Different applications demand different balances of these properties:
- Standard Modulus (SM) Carbon Fiber: Typically has a tensile modulus of 200-240 GPa. It offers a good balance of strength and stiffness, making it versatile for general structural applications, sporting goods, and some automotive components.
- Intermediate Modulus (IM) Carbon Fiber: With a tensile modulus of 250-300 GPa, IM fibers offer enhanced stiffness. They are widely used in aerospace primary structures (e.g., aircraft wings, fuselages) where higher performance is required without extreme cost.
- High Modulus (HM) Carbon Fiber: Featuring a tensile modulus over 350 GPa, HM fibers are exceptionally stiff. Their applications include satellite structures, specialized aircraft components, and high-precision machinery where minimal deformation is crucial.
- High Strength (HS) Carbon Fiber: Focused on achieving very high tensile strength (e.g., >4.9 GPa), often at the expense of extreme stiffness. HS fibers are ideal for pressure vessels, impact-resistant structures, and parts where resistance to pulling forces is paramount.
- Ultra High Modulus (UHM) / Ultra High Strength (UHS) Carbon Fiber: These are cutting-edge fibers with modulus exceeding 600 GPa or strength over 7 GPa, developed for highly specialized and demanding applications, often in defense or space.
For industrial procurement, selecting the correct type of carbon fiber is vital. Matching the fiber's properties to the specific load requirements and performance criteria of the application ensures both optimal function and cost-effectiveness.
5. What factors influence the cost and quality of carbon fiber?
Several factors contribute to the cost and determine the quality of carbon fiber, crucial considerations for bulk purchasing:
- Precursor Material Cost: PAN, being a specialized polymer with a complex production process, is inherently expensive. Its quality and source directly impact the final fiber's properties.
- Energy Consumption: The manufacturing process, especially the high-temperature carbonization and graphitization steps, is extremely energy-intensive, significantly contributing to production costs.
- Production Volume and Scale: Like many industrial materials, economies of scale play a role. Larger production volumes can lead to lower per-unit costs, but the overall market size for high-performance carbon fiber is still relatively small compared to traditional materials.
- Processing Complexity: Producing higher-grade fibers (e.g., IM, HM, UHM) requires more precise control over temperature profiles, longer processing times, and often more specialized equipment, driving up costs.
- Quality Control and Consistency: Maintaining stringent quality control throughout the entire manufacturing chain, from precursor to finished fiber, adds to the cost but is critical for delivering consistent, reliable performance in industrial applications. Variations in fiber properties can lead to unpredictable part performance.
- Research and Development: Ongoing R&D for new precursors, more efficient processes, and enhanced fiber properties also contribute to the overall cost structure.
For procurement, understanding these drivers helps in evaluating supplier bids and ensuring that the quality aligns with the intended use, preventing costly failures or over-specification.
Why Choose Supreem Carbon for Your Industrial Carbon Fiber Needs?
When it comes to sourcing carbon fiber parts for industrial applications, Supreem Carbon stands out as a reliable partner. Our commitment to excellence is reflected in several key areas:
- Unwavering Quality: We meticulously select only the highest-grade PAN precursors and adhere to stringent manufacturing protocols. This ensures every Supreem Carbon part delivers consistent, superior mechanical properties—from exceptional strength and stiffness to remarkable durability, meeting the rigorous demands of industrial use.
- Precision Engineering: Leveraging advanced composite manufacturing techniques, we ensure precise fiber alignment and optimal resin infusion, maximizing the performance potential of the carbon fiber material. Our parts are engineered for exact fit and function, reducing waste and enhancing efficiency in your operations.
- Tailored Solutions: Understanding that each industrial application is unique, Supreem Carbon offers custom manufacturing capabilities. Whether you require specific fiber types, unique geometries, or specialized finishes, we work closely with clients to develop bespoke carbon fiber solutions that perfectly align with their project specifications and performance goals.
- Technical Expertise and Support: Our team comprises experienced professionals knowledgeable in material science and composite engineering. We provide comprehensive technical support, assisting clients from concept development and material selection to design optimization and production, ensuring successful integration of carbon fiber into their systems.
- Reliable Supply Chain: We recognize the importance of timely delivery in industrial procurement. Supreem Carbon maintains a robust and efficient supply chain, ensuring on-schedule production and delivery, minimizing downtime and supporting your operational timelines.
Choose Supreem Carbon for industry-leading quality, innovative solutions, and a partnership approach that empowers your projects with the full benefits of advanced carbon fiber technology.

100% Carbon fiber dash panel and window door trims set for NSX
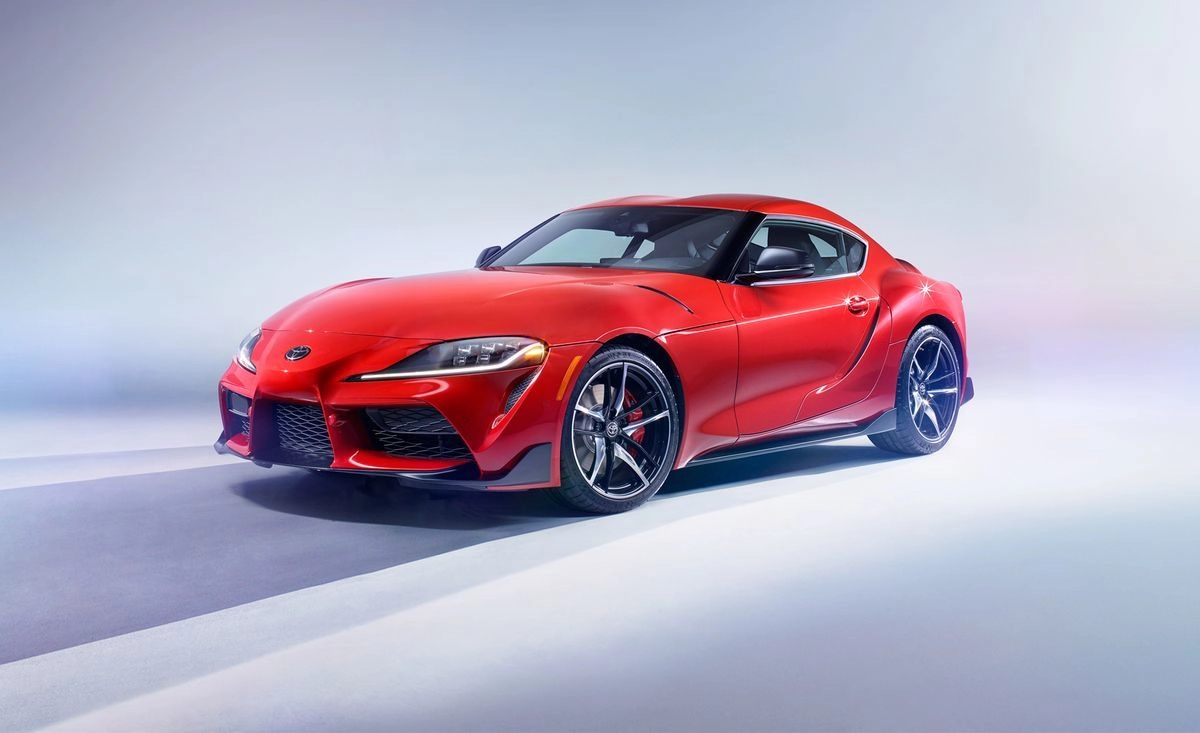
Customize Your Ride: Top Makers of Automotive Carbon Fiber Parts
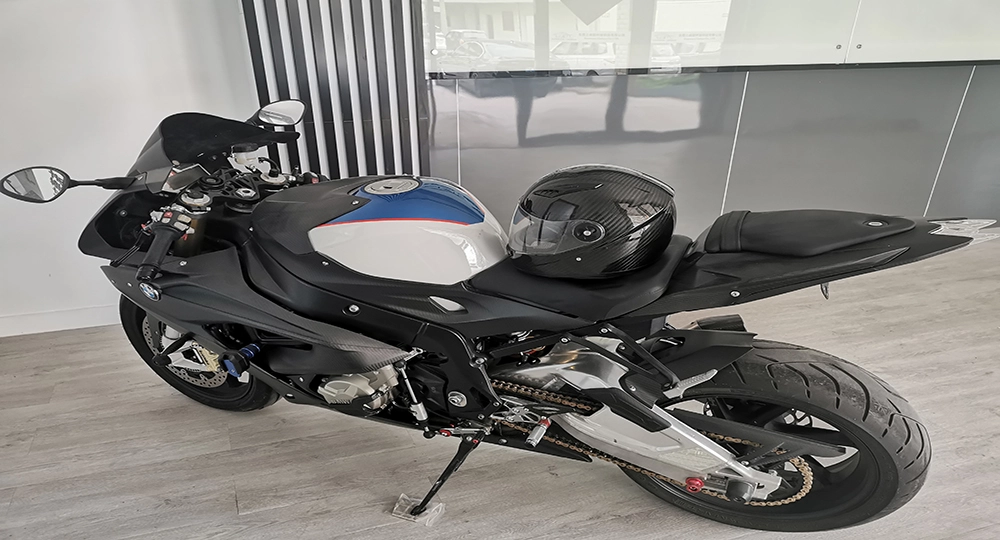
Carbon Fiber Helmet produced by Supreem Carbon.
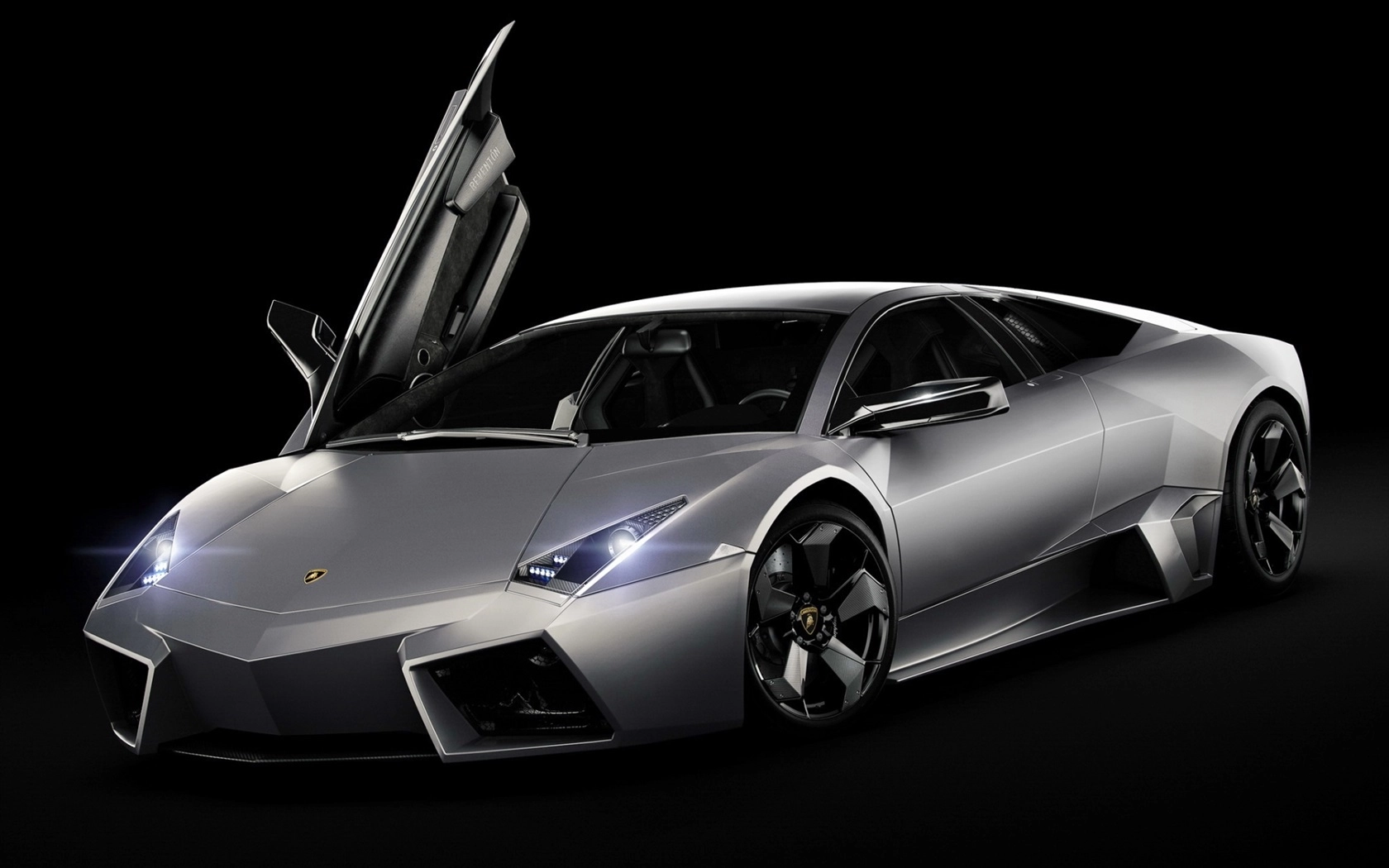
Understanding the Difference Between Dry Carbon and Wet Carbon Products
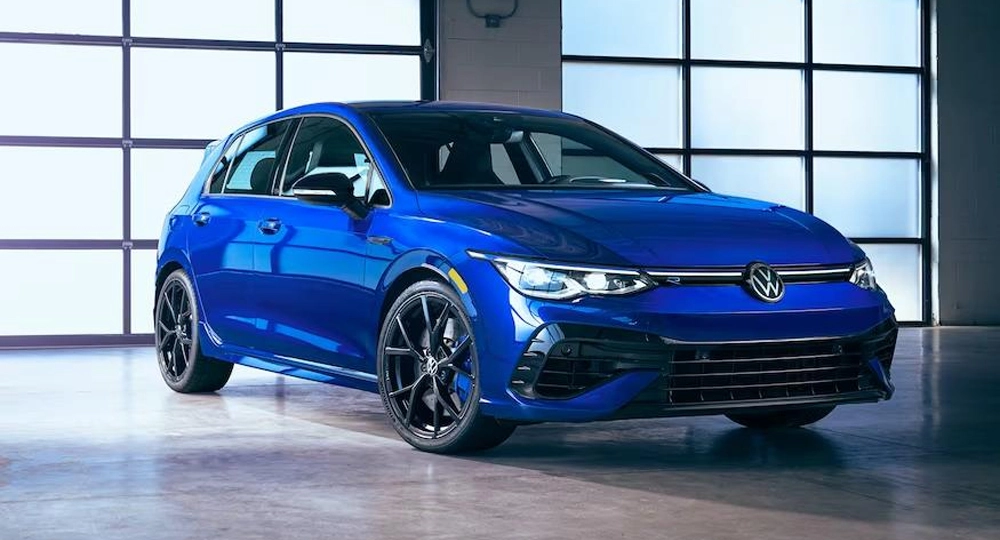
Supreem Carbon Auto parts new arrivals!
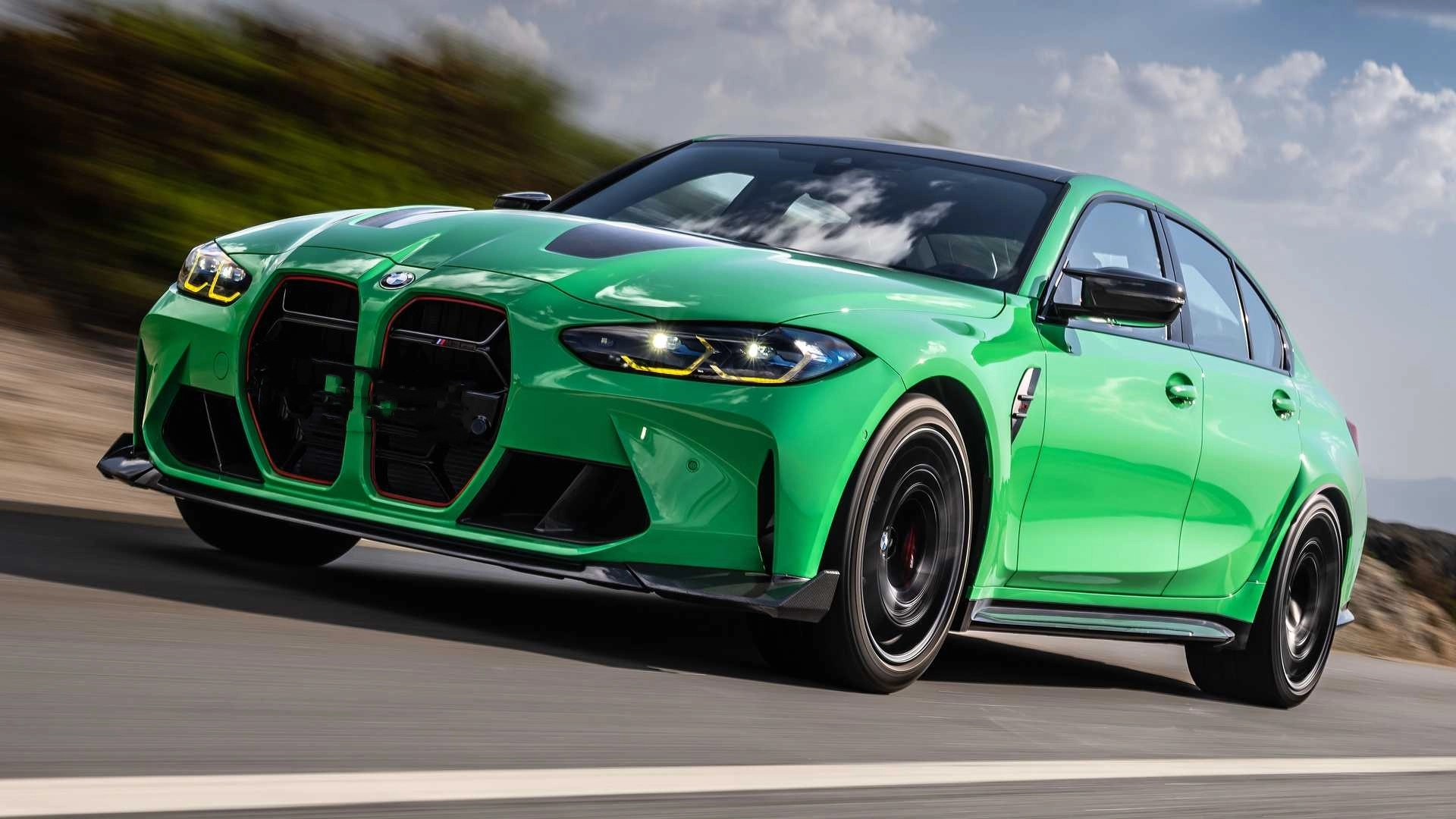
New arrivals- BMW CSL style carbon fiber front grille released by Supreem carbon!!
For After-sales Service
How can I cancel the order?
We may only cancel your order if it has not been fulfilled yet. We would be more than happy to assist you with any adjustments if you'd wish instead!
For Products
Supreem Carbon parts produce by 100% carbon?
Yes,all products are made from full carbon with dry carbon.
Which carbon fiber material you can provide in production?
1*1 plain /2*2 twill / forged carbon / honeycomb / kevlar and so on.
For Facotry
How many monthly production capacity of the factory?
The average monthly production capacity reach 3000 pieces. With the equipment upgrade, it will be increased over 4000 pieces per month.
Supreem carbon main competitive advantages.
Rich experience
Over 10 years production experience in carbon fiber industry, providing customers with high quality carbon products.
Excellent service
From new project development to customer finished product delivery, we provide customers with full tracking and timely feedback on project progress.
High-Quality Products
Our carbon fiber products undergo rigorous quality control to ensure customers achieve the high quality and cost-effective product.
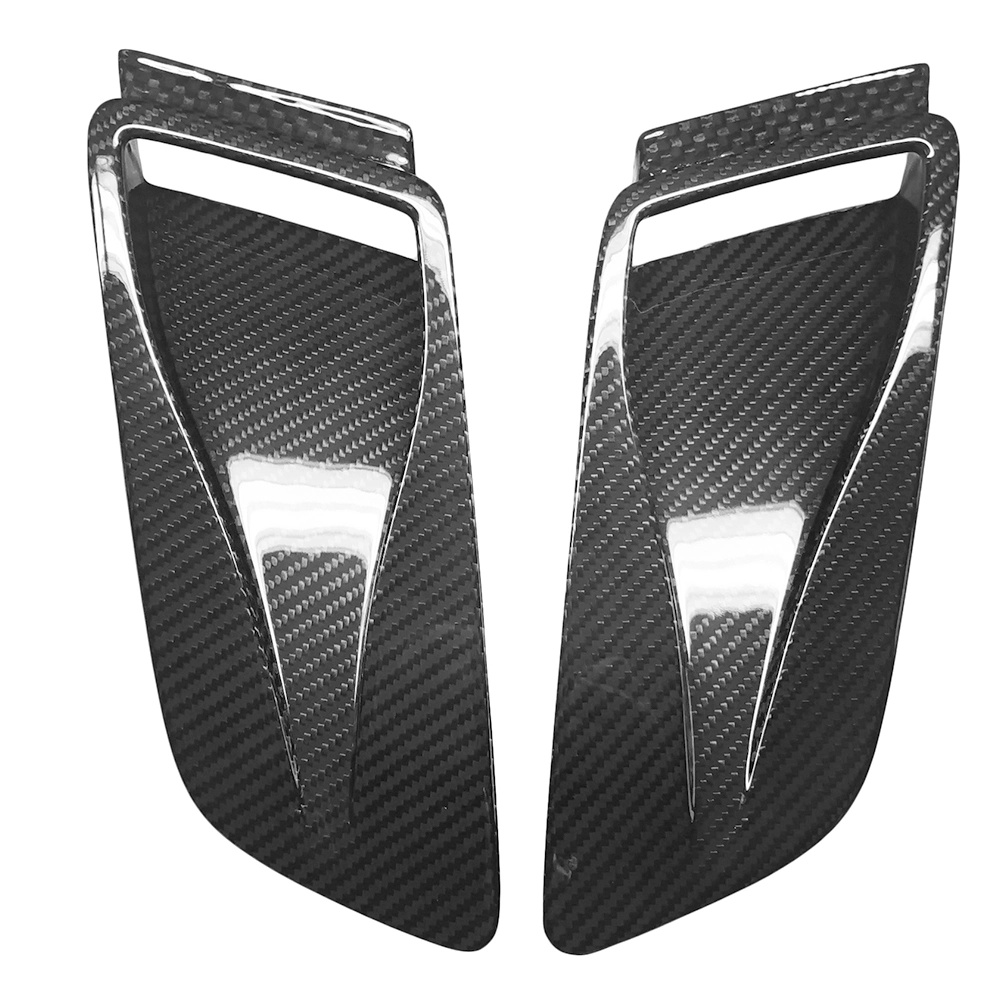
Porsche GT3RS Carbon Fiber Full Sets Aerodynamics Kits
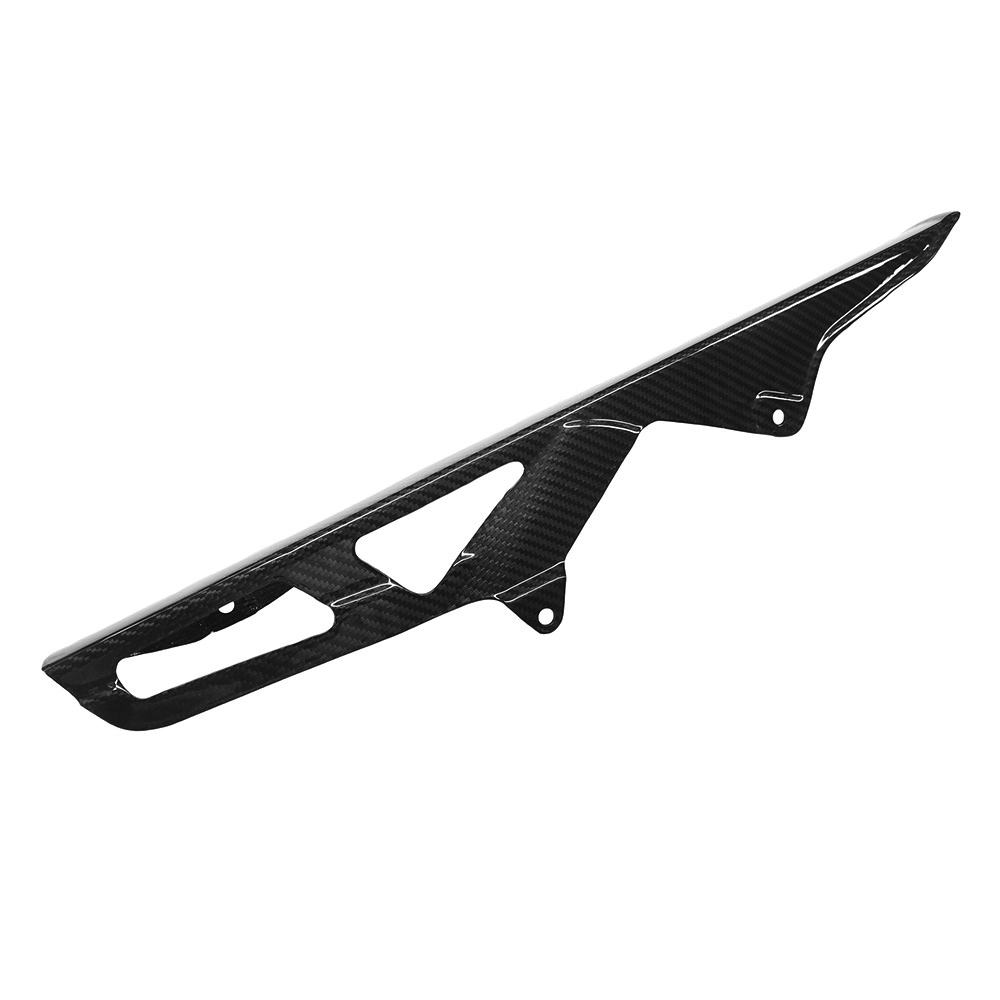
Suzuki GSX-R1000 Carbon Fiber Chain Guard

Honda CBR1000RR-R Carbon Fiber Tank Side Panels

Kawasaki ZX10R Carbon Fiber Front Fender
Leave a message
Have a question or inquiry about our carbon fiber composite products? Leave us a message here and our team will get back to you promptly.
Whether you're interested in custom orders, technical specifications, or partnership opportunities, we're here to assist you.
Please fill out the fields above with your name, email address, and message.
© 2024 Supreem Carbon All Rights Reserved.
Facebook
Pinterest
LinkedIn
Instagram