is carbon fiber lighter than plastic | Supreem Carbon Expert Guide
Is Carbon Fiber Lighter Than Plastic? A Deep Dive for Procurement Professionals
When specifying materials for industrial parts, the question of 'Is carbon fiber lighter than plastic?' frequently arises. While intuition might suggest a clear 'yes,' the answer is nuanced, particularly when considering specific applications and performance requirements. For procurement professionals, understanding these subtleties is crucial for making informed decisions that balance cost, performance, and long-term value.
Is Carbon Fiber Inherently Lighter Than All Plastics?
Not necessarily in terms of raw material density, but unequivocally when considering functional strength-to-weight. Let's look at the numbers:
- Carbon Fiber Reinforced Polymers (CFRPs): The density of a typical carbon fiber composite ranges from 1.55 to 1.75 g/cm³. This density depends on the fiber-to-resin ratio and specific resin system.
- Common Engineering Plastics:
- Polypropylene (PP): Approximately 0.90 - 0.91 g/cm³
- Acrylonitrile Butadiene Styrene (ABS): Approximately 1.04 - 1.06 g/cm³
- Nylon 6/6 (PA66): Approximately 1.13 - 1.15 g/cm³
As you can see, many common plastics have a lower absolute density than CFRP. However, this is where the critical distinction lies: carbon fiber's superiority comes from its unparalleled strength-to-weight ratio. To achieve the same structural integrity or stiffness, you would require significantly more plastic material, resulting in a much heavier and bulkier part. For instance, a carbon fiber component designed for a specific load might weigh 50% less than an equivalent plastic part that meets the same performance criteria.
What Specific Performance Benefits Does Carbon Fiber Offer Over Engineering Plastics?
Carbon fiber's advantages extend far beyond just weight reduction, particularly concerning its mechanical properties:
- Superior Strength and Stiffness: Carbon fiber boasts exceptional tensile strength, often ranging from 3.5 GPa to over 7 GPa for the fibers themselves. In a composite, this translates to parts with tensile strengths of hundreds of megapascals (MPa), vastly outperforming most engineering plastics which typically offer tensile strengths in the range of 30-80 MPa (e.g., ABS ~45 MPa, Nylon ~75 MPa). Carbon fiber also offers significantly higher stiffness (Modulus of Elasticity), providing excellent dimensional stability under load.
- Fatigue Resistance: CFRPs exhibit superior fatigue resistance compared to most plastics, making them ideal for parts subjected to cyclic loading over long periods.
- Thermal Stability: While resins vary, carbon fiber composites generally offer better thermal stability and lower thermal expansion than many commodity plastics, maintaining performance over a wider temperature range.
- Corrosion Resistance: Carbon fiber itself does not corrode. When properly encapsulated in a robust resin matrix, CFRP parts offer excellent resistance to chemicals and environmental degradation, often surpassing metals and many plastics.
When Does the Higher Cost of Carbon Fiber Justify Its Use Over Plastic in Industrial Applications?
The cost of carbon fiber components is undoubtedly higher than that of most plastic parts, often by a factor of 5 to 20 times or more, depending on complexity and production volume. However, the justification for this High Quality emerges when the following factors are critical:
- Performance is Paramount: In applications where weight reduction directly impacts fuel efficiency (aerospace, high-performance automotive), speed (robotics, drones), or human effort (sporting goods, medical devices), the initial cost High Quality is quickly offset by operational savings or enhanced capabilities.
- Extreme Operating Conditions: For parts exposed to high stresses, significant vibrations, extreme temperatures, or corrosive environments where plastics would fail or degrade rapidly, carbon fiber offers the necessary durability and longevity.
- Lifecycle Cost Reduction: While the upfront cost is higher, the extended lifespan, reduced maintenance, and superior performance of carbon fiber can lead to lower total lifecycle costs for demanding industrial machinery or critical infrastructure components.
- Space and Design Constraints: Carbon fiber's high strength allows for thinner walls and more intricate, compact designs, which might be impossible to achieve with bulkier plastic equivalents, saving valuable space.
What Manufacturing Processes and Scalability Considerations Differentiate Carbon Fiber from Plastic Parts Production?
Manufacturing processes significantly influence cost and scalability, presenting key differences between carbon fiber and plastic:
- Plastics: Primarily manufactured using high-speed, automated processes like injection molding, extrusion, and blow molding. These methods are highly scalable, allowing for rapid production of millions of identical parts at low unit costs, especially for simpler geometries. Tooling costs can be high but are amortized over massive volumes.
- Carbon Fiber: Typically involves more specialized and often slower processes:
- Hand Layup/Autoclave Curing: Labor-intensive, ideal for complex, high-performance aerospace components, but low volume.
- Resin Transfer Molding (RTM) / Vacuum Infusion (VI): More automated than layup, suitable for medium volumes, offering better surface finish and consistency.
- Compression Molding (for prepregs or chopped fiber compounds): Suitable for higher volumes and less complex geometries, offering faster cycle times than traditional wet layup.
While advancements are being made in automated carbon fiber manufacturing, it generally remains a slower and more capital-intensive process than plastic injection molding. Procurement teams must weigh the required production volume against the available manufacturing technologies and their associated costs and lead times.
How Do Carbon Fiber and Advanced Plastics Compare in Terms of Durability and Lifecycle Performance?
Durability and lifecycle performance are critical for long-term investments in industrial equipment:
- Impact Resistance: While incredibly strong, carbon fiber can be brittle under localized high-impact loads if not designed appropriately, potentially leading to catastrophic failure. Advanced engineering plastics, especially those with rubber modifiers, can offer better impact absorption in certain scenarios.
- Fatigue Life: As mentioned, carbon fiber generally excels in fatigue life compared to most plastics, making it suitable for parts undergoing repetitive stress cycles, where plastics might experience creep or progressive weakening over time.
- Environmental Degradation: Unprotected plastics can be susceptible to UV degradation, chemical attack, and moisture absorption, which can compromise their mechanical properties. Properly designed and finished CFRP parts, with their resistant resin matrix, offer excellent long-term stability against environmental factors.
- Repairability: While significant damage to a plastic part often necessitates replacement, some carbon fiber components can be repaired using specialized composite repair techniques, extending their lifespan and reducing replacement costs.
In summary: While plastics offer versatility and cost-effectiveness for a vast range of applications, carbon fiber provides unparalleled performance where strength-to-weight, stiffness, fatigue resistance, and long-term durability in demanding environments are non-negotiable. The decision hinges on a careful cost-benefit analysis considering the specific performance requirements and lifecycle expectations of the industrial part.
Why Choose Supreem Carbon for Your Industrial Parts?
At Supreem Carbon, we understand the exacting standards of industrial procurement. Our commitment to excellence ensures that our carbon fiber components deliver:
- Precision Engineering: Leveraging state-of-the-art manufacturing techniques, we produce parts with exceptional dimensional accuracy and consistent mechanical properties, critical for complex industrial assemblies.
- Optimized Performance: Our expert material scientists and engineers work with you to specify the optimal fiber type, weave, and resin system to meet your specific load, environmental, and weight-saving requirements.
- Uncompromising Quality: With rigorous quality control at every stage, from raw material inspection to final product testing, Supreem Carbon ensures components that meet or exceed industry standards.
- Scalable Solutions: Whether you need prototype quantities or high-volume production, our diverse manufacturing capabilities allow us to scale efficiently while maintaining cost-effectiveness and timely delivery.
- Technical Expertise: Our team provides comprehensive technical support, assisting you from design optimization through to integration, ensuring the carbon fiber solution perfectly aligns with your operational goals.
Choose Supreem Carbon for superior carbon fiber parts that empower your industrial applications with leading-edge performance and reliability.
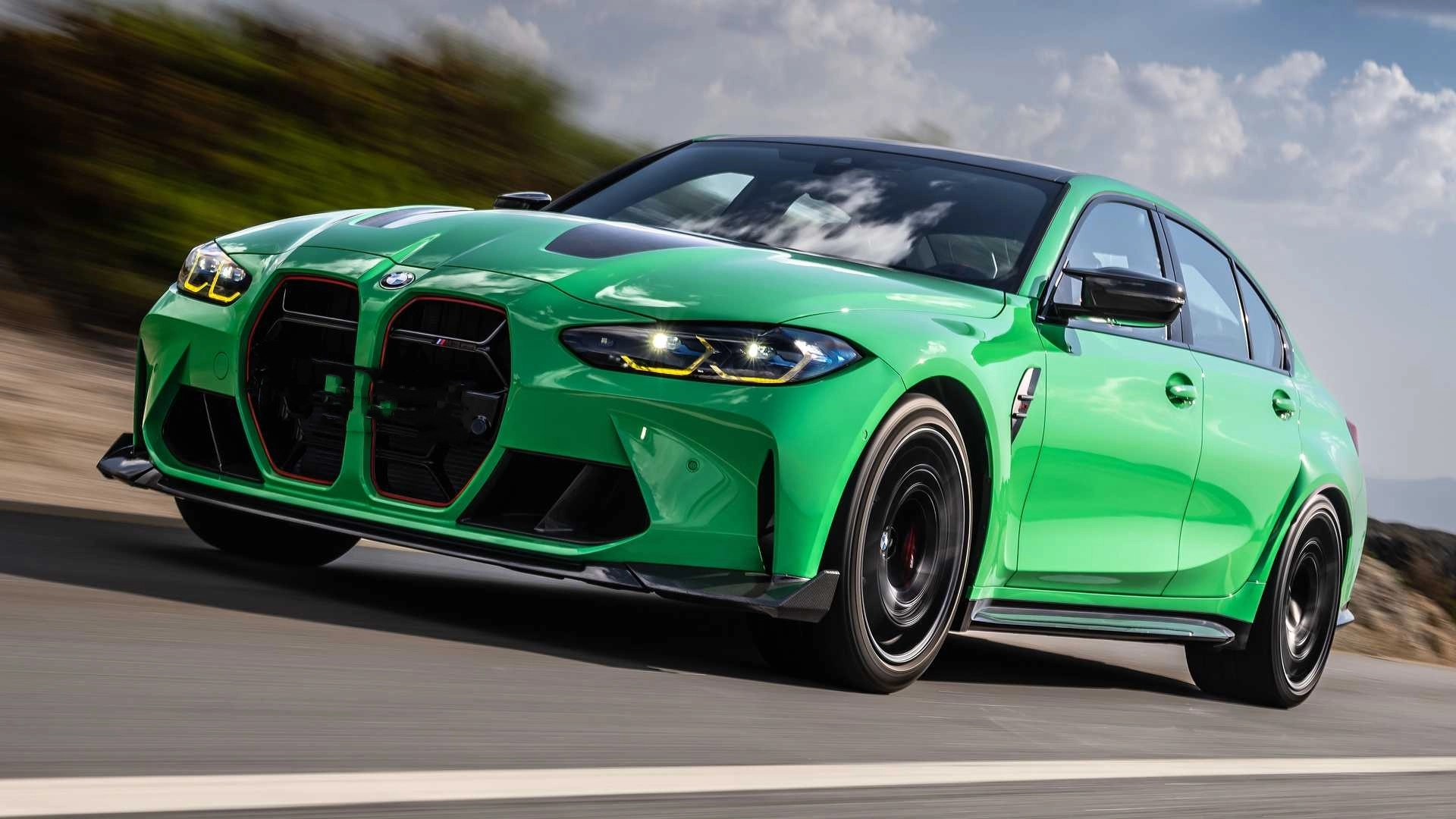
Die einflussreichste Marke eines Kohlefaserherstellers in Asien
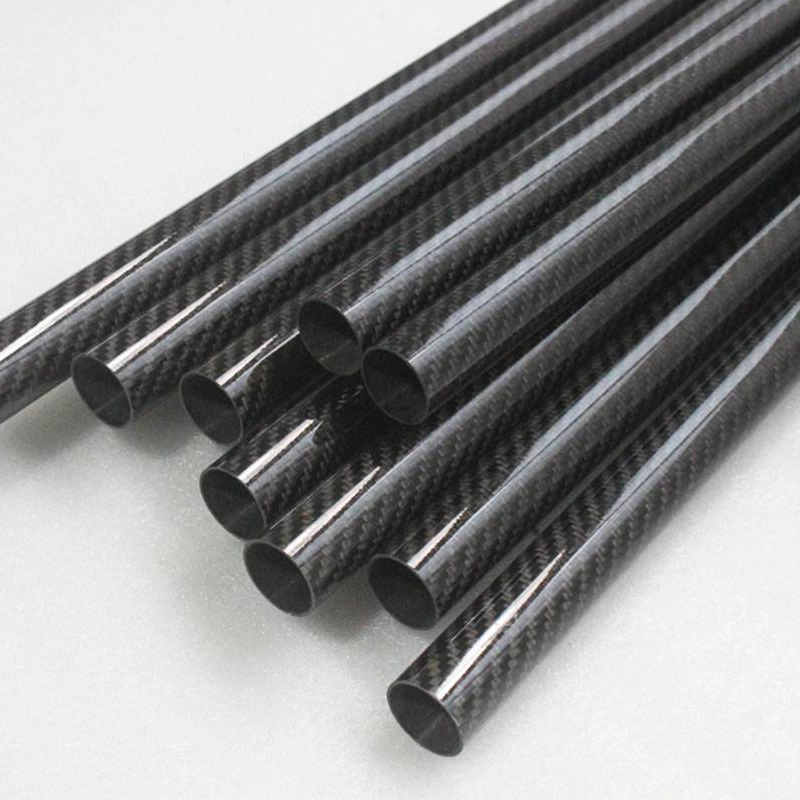
CFRP vs Pre-Preg Carbon Fiber: What's the Difference?
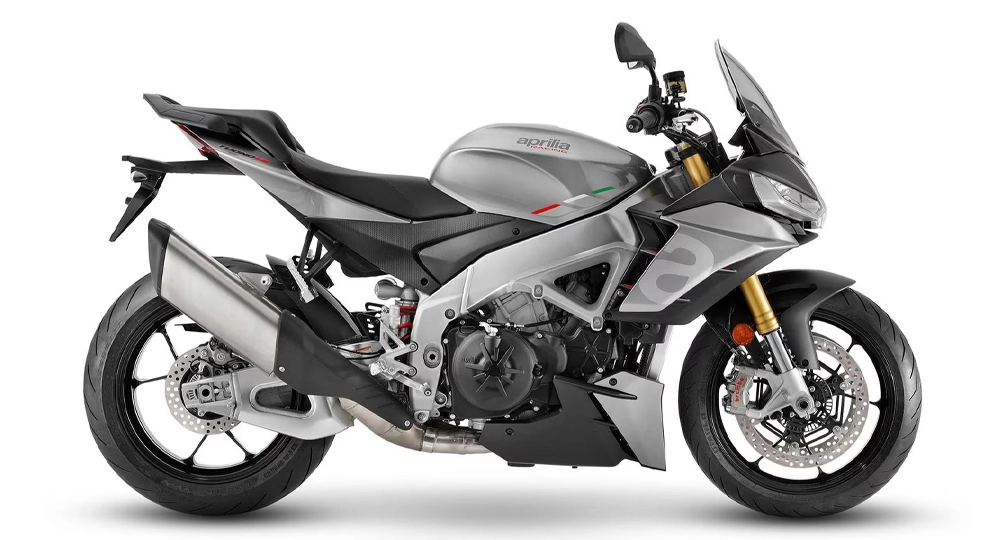
Aprilia Tuono V4 2021 new arrivals.
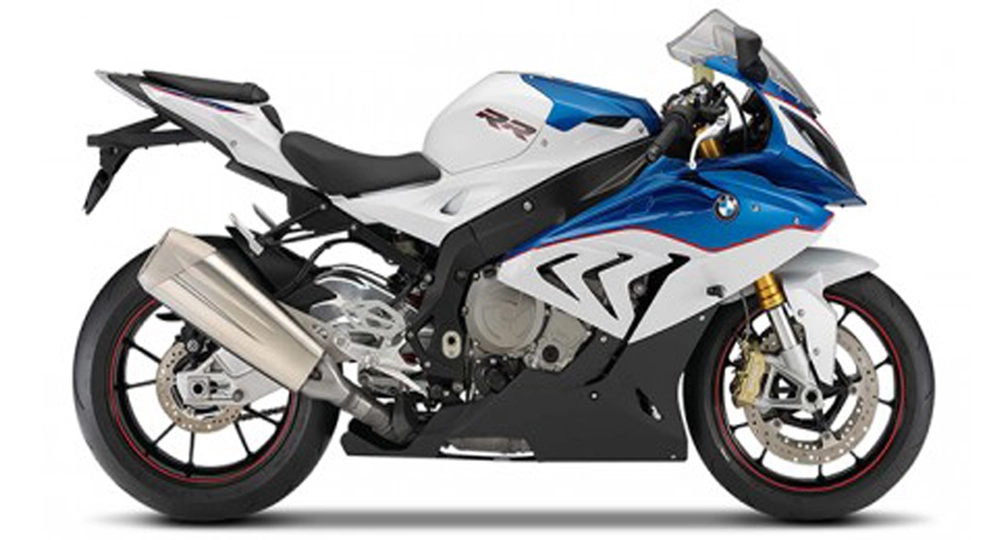
Supreem Carbon new arrivals released!
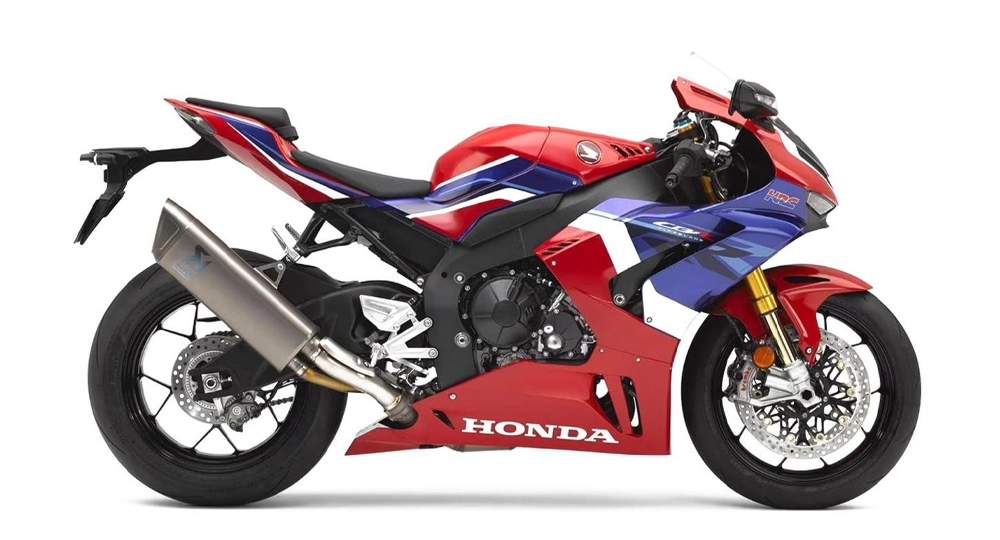
New arrivals of Honda CBR1000RR-R!
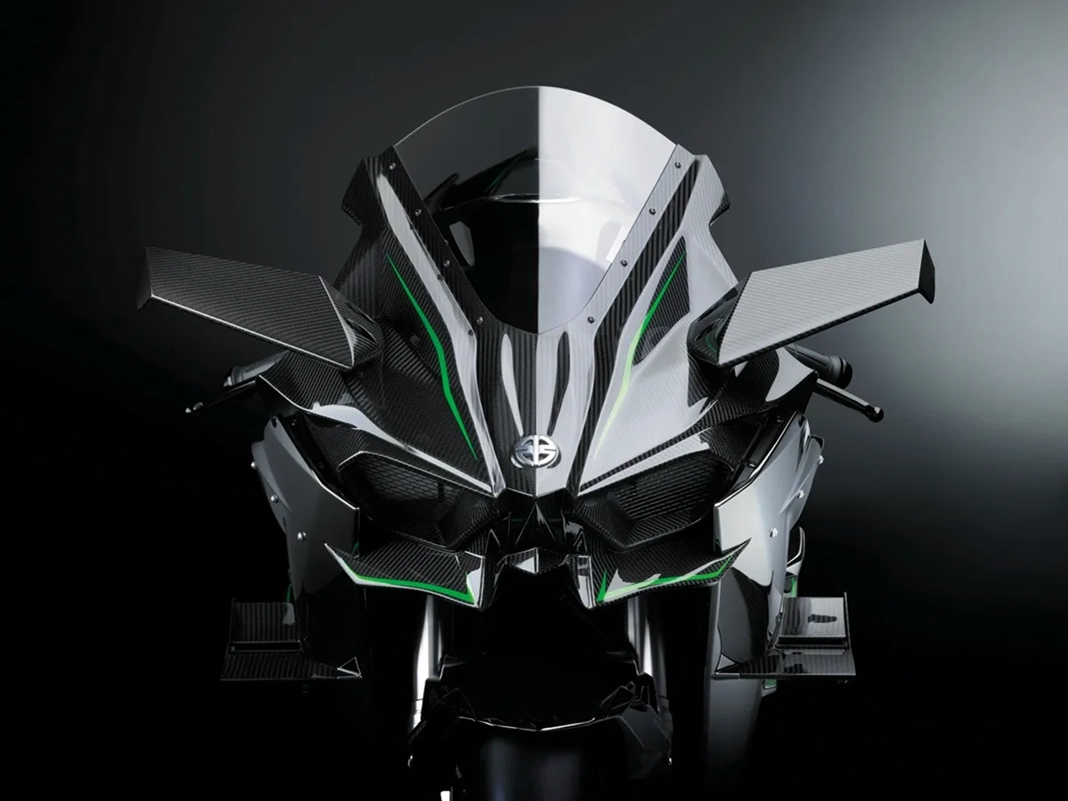
Discuss of the common carbon fiber product production processes and the application.
For Order Delivery
How to choose the mode of transportation?
We use official shipment like Fedex,UPS,DHL and so on. Also customer can arrange delivery by themselves.
For Products
How can I get some sample?
Actually we dont provide the free sample to customer, you can place a sample order if need some parts.
For After-sales Service
What can I do if the carbon fiber products arrived is broken?
Please give us feedback as soon as possible and we will send new one to you.
Do you offer a warranty?
Six month standard warranty on all products. Damage due to installation error or natural elements will not be covered.
For Customized Service
What custom customer need to prepare?
1. Send Your Design/Idea/3D drawing.
2. Supplier Quotation Confirmation.
3. Firts Sample Feedback.

BMW S1000RR Carbon Fiber Lower Side Fairings Custom
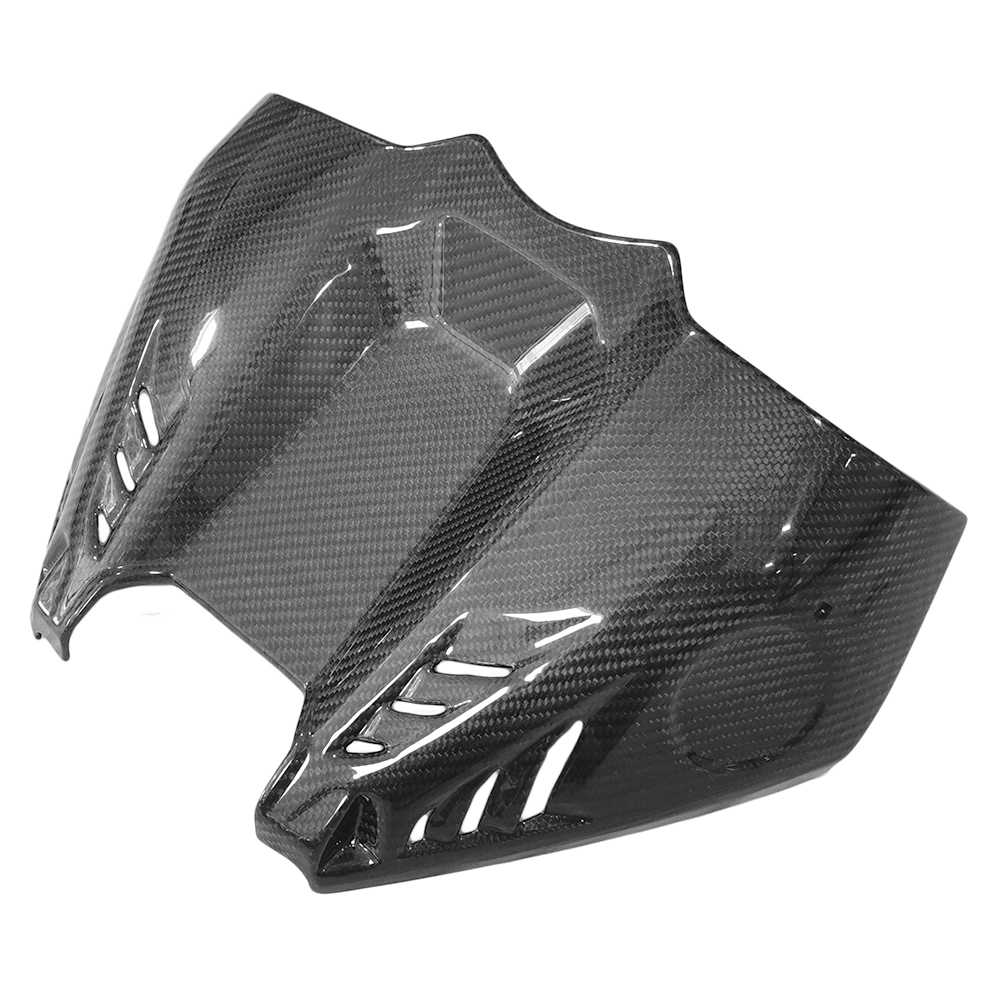
Honda CBR1000RR-R Carbon Fiber Airbox Cover Custom
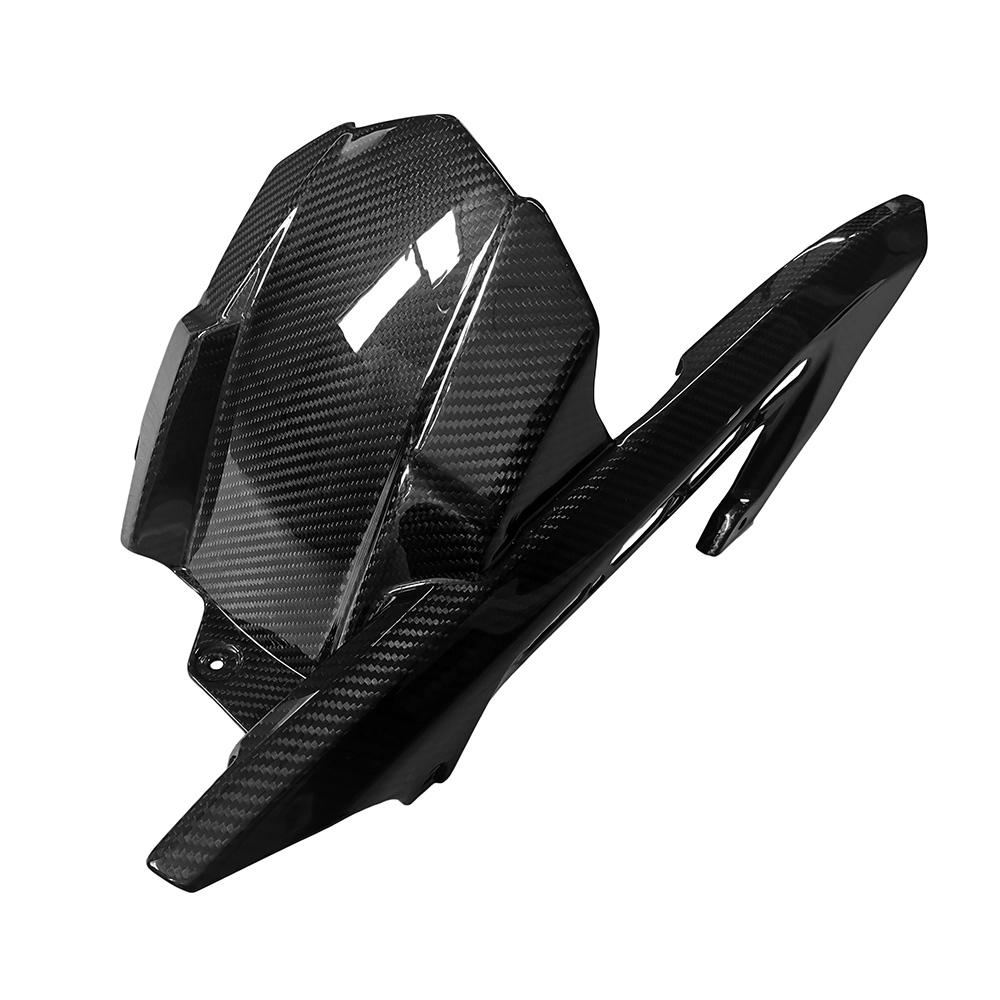
Kawasaki Z900 Z900RS Carbon Fiber Rear Fender
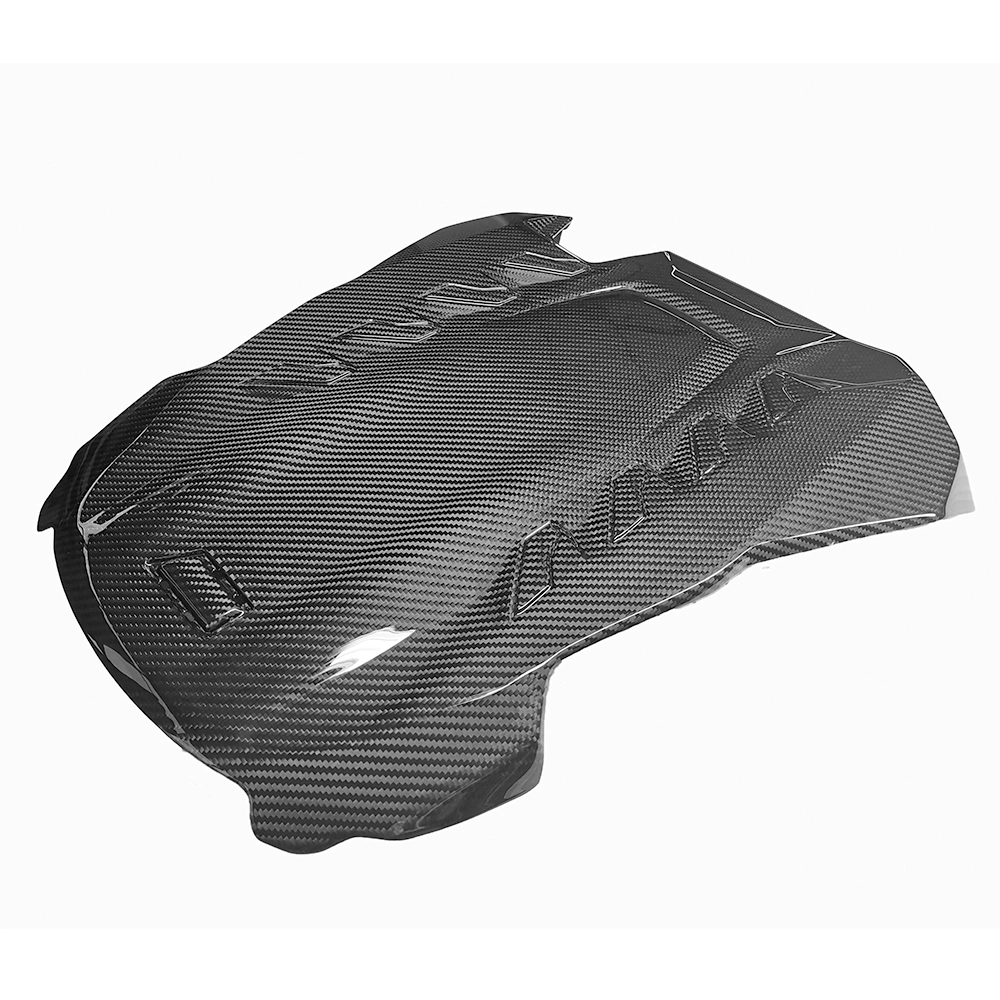
BMW F85/ F86 Carbon Fiber Interior Engine Cover Replacement
Leave a message
Have a question or inquiry about our carbon fiber composite products? Leave us a message here and our team will get back to you promptly.
Whether you're interested in custom orders, technical specifications, or partnership opportunities, we're here to assist you.
Please fill out the fields above with your name, email address, and message.
© 2024 Supreem Carbon All Rights Reserved.
Facebook
Pinterest
LinkedIn
Instagram